EIPC Winter Conference, Day 2
April 3, 2019 | Alun Morgan, EIPCEstimated reading time: 8 minutes
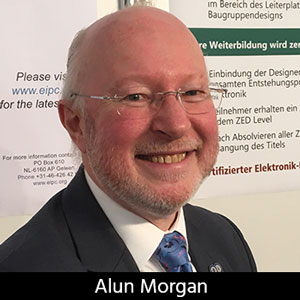
After the papers from the first day of the EIPC Winter Conference in Milan on February 14–15, the delegates were hosted at a reception and plant tour of Elga Europe at their nearby production facility. CEO Georgio Favini CEO described that Elga was founded in 1973 and had had three important joint ventures in its history—first with Lea Ronal, then Tokyo Ohka, and Eternal currently. Favini explained that Elga Europe is the European leader in dry-film photoresist for PCB fabrication and the only remaining European producer with a capacity of 15 million m2/year.
Favini described the dry-film production process in detail. Then, the delegates were treated to a comprehensive plant tour, including all the stages of manufacturing through mixing, coating, drying, in-line inspection, testing, and slitting. The delegates greatly appreciated the hospitality shown by Elga Europe and felt privileged to have been shown around the impressive facility by such knowledgeable staff.
The delegates then went back to downtown Milan for a gastronomic dinner in the very chic deli/restaurant called “Eataly.” Suitably refreshed after the excellent networking dinner, the delegates took their places for day two of the programme.
Sessions and Papers
The opening session titled “New Developments in PCB Technology: DFM and Cost-effective Supply Chain Management” was chaired by EIPC Board Member Michele Stampanoni who introduced the first speaker, Robrecht Belis of Elsyca. Belis introduced a PCB plating performance simulation system that allows plating layer thickness distribution prognosis before the start of production.
Belis explained that the PCB plating process is very sensitive to panel size, pattern, holes, plating infrastructure, and the electrolyte. The system characterises the plating process using infrastructure and electrolyte data and utilises the specific circuit design to build a simulation of plating distribution.
Belis went on to describe how design modifications, copper balancing, and layout optimisation can then be performed before production starts. Belis concluded with a case study carried out at EuroCircuits where he demonstrated the resulting optimised layout, time savings, and better-quality deposition uniformity over manual techniques.
Roland Valentini of Gardien Group was next to present on “The Impact on Supply Chain Management: Final PCB Yield and Profitability.” Valentini started his presentation from the premise that there had been a major change in the industry from analogue to digital, and that this had brought new challenges for manufacturing and test. He further argued that traceability is going to be one of the key requirements to fulfil in high-reliance markets, identifying the sectors as automotive, space, aerospace and military, medical, industrial, network and 5G base stations, mobile communications, and home automation.
Valentini also described the Gardien-managed supply chain process whereby the supply chain between the purchasing manager and PCB fabricator is kept as lean as possible with steps non-value-added steps being eliminated. The presentation concluded with a Chinese PCB sourcing example with the potential to effectively double the number of potential PCB suppliers, and a description of the Gardien test service to the PCB industry to improve quality, reliability, and total productivity.
Page 1 of 2
Suggested Items
Driving Innovation: Direct Imaging vs. Conventional Exposure
07/01/2025 | Simon Khesin -- Column: Driving InnovationMy first camera used Kodak film. I even experimented with developing photos in the bathroom, though I usually dropped the film off at a Kodak center and received the prints two weeks later, only to discover that some images were out of focus or poorly framed. Today, every smartphone contains a high-quality camera capable of producing stunning images instantly.
Hands-On Demos Now Available for Apollo Seiko’s EF and AF Selective Soldering Lines
06/30/2025 | Apollo SeikoApollo Seiko, a leading innovator in soldering technology, is excited to spotlight its expanded lineup of EF and AF Series Selective Soldering Systems, now available for live demonstrations in its newly dedicated demo room.
Indium Corporation Expert to Present on Automotive and Industrial Solder Bonding Solutions at Global Electronics Association Workshop
06/26/2025 | IndiumIndium Corporation Principal Engineer, Advanced Materials, Andy Mackie, Ph.D., MSc, will deliver a technical presentation on innovative solder bonding solutions for automotive and industrial applications at the Global Electronics A
Fresh PCB Concepts: Assembly Challenges with Micro Components and Standard Solder Mask Practices
06/26/2025 | Team NCAB -- Column: Fresh PCB ConceptsMicro components have redefined what is possible in PCB design. With package sizes like 01005 and 0201 becoming more common in high-density layouts, designers are now expected to pack more performance into smaller spaces than ever before. While these advancements support miniaturization and functionality, they introduce new assembly challenges, particularly with traditional solder mask and legend application processes.
Knocking Down the Bone Pile: Tin Whisker Mitigation in Aerospace Applications, Part 3
06/25/2025 | Nash Bell -- Column: Knocking Down the Bone PileTin whiskers are slender, hair-like metallic growths that can develop on the surface of tin-plated electronic components. Typically measuring a few micrometers in diameter and growing several millimeters in length, they form through an electrochemical process influenced by environmental factors such as temperature variations, mechanical or compressive stress, and the aging of solder alloys.