IPC Working to Revive Lead-Free R&D in High-Reliability Sectors
April 10, 2019 | Chris Mitchell, IPC VP, Global Government RelationsEstimated reading time: 3 minutes
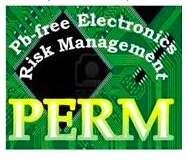
Ask yourself the following question: Why is it that the aerospace, defense and high performance (ADHP) electronics sectors remain reliant on lead solders and components even as the commercial sector has largely phased out their use?
The short answer is that lead-free electronics do not offer the performance and reliability assurances that the ADHP sectors require, but the longer answer is that key stakeholders, including government entities, have not invested in the science to understand how to achieve symmetry and interchangeability between lead and lead-free electronics.
IPC is working to change that and we need your help.
Essential R&D Delayed by Budget Cuts
Over the last 15 years, the commercial electronics industry has largely phased out its use of lead (Pb) in the manufacture of electronic components and circuit assemblies. The transition to Pb-free electronics was driven by the European Union’s Restriction of Hazardous Substances Directive (RoHS), which placed new restrictions on the use of lead in commercial products.
Though initiated in Europe, RoHS has had a global impact on the electronics industry. Other countries have followed Europe’s lead and manufacturers are now obligated to eliminate the use of lead in their goods for markets around the world.
The migration to Pb-free electronics has been successful in the commercial markets, but the ADHP electronics sectors have been slower to abandon the traditional tin-lead solder used in the production of components and circuit assemblies. ADHP products have more demanding performance requirements than consumer electronics; they need to perform flawlessly in harsh environments and in safety-related applications; and there is not enough data on the performance of Pb-free products to support the move.
Enter the Pb-Free Electronics Risk Management (PERM) Council, comprised of subject matter experts from government, industry, academia, and other stakeholders. Founded in 2008 and housed by IPC since 2012, the PERM Council provides leadership and coordination of Pb-free electronics risk management activities in both government and industry.
A major focus of the PERM Council has been gathering enough detailed engineering knowledge to underpin the conversion from tin-lead solder to Pb-free in the ADHP sectors. In 2009, PERM supported an effort funded by the U.S. Department of Defense (DoD) to identify the knowledge gaps and estimate the cost to fill them. The cost estimate this “Pb-Free Manhattan Project” was about $110 million over three years, broken down into more than 100 “bite-size chunks” from $100,000 to $5 million.
Unfortunately, due to DoD budget cuts in the last decade, the “Manhattan Project” was never fully funded, although some companies and universities continued to work on the smaller chunks. In 2014, IPC completed a “re-baseline” and estimated that about $40-50 million was still needed to complete the knowledge base. To date, the R&D project is still incomplete.
Now, in 2019, IPC and a consortium of manufacturers and academic institutions are working with more than a dozen congressional offices to secure $15 million in federal funding to put the R&D back on track. The formal funding requests have been filed; congressional deliberations on defense spending are underway; and Congress is expected to send a defense appropriations bill to the president for his signature by late summer, at which time we will know whether we have been successful.
A great deal of policymaker education and advocacy will be necessary to achieve this goal in 2019 and to keep the momentum going in 2020 and beyond. The IPC Government Relations team will be working on the issue 24/7, but members of Congress are most interested in hearing from IPC members, i.e. the front-line business leaders in their states and congressional districts.
To learn more and contribute your expertise to IPC’s Pb-free electronics efforts, please visit the PERM Council page on IPC’s website and contact me at ChrisMitchell@ipc.org to join our Advocacy Team.
Suggested Items
Indium’s Karthik Vijay to Present on Dual Alloy Solder Paste Systems at SMTA’s Electronics in Harsh Environments Conference
05/06/2025 | Indium CorporationIndium Corporation Technical Manager, Europe, Africa, and the Middle East Karthik Vijay will deliver a technical presentation on dual alloy solder paste systems at SMTA’s Electronics in Harsh Environments Conference, May 20-22 in Amsterdam, Netherlands.
SolderKing Achieves the Prestigious King’s Award for Enterprise in International Trade
05/06/2025 | SolderKingSolderKing Assembly Materials Ltd, a leading British manufacturer of high-performance soldering materials and consumables, has been honoured with a King’s Award for Enterprise, one of the UK’s most respected business honours.
Knocking Down the Bone Pile: Gold Mitigation for Class 2 Electronics
05/07/2025 | Nash Bell -- Column: Knocking Down the Bone PileIn electronic assemblies, the integrity of connections between components is paramount for ensuring reliability and performance. Gold embrittlement and dissolution are two critical phenomena that can compromise this integrity. Gold embrittlement occurs when gold diffuses into solder joints or alloys, resulting in mechanical brittleness and an increased susceptibility to cracking. Conversely, gold dissolution involves the melting away of gold into solder or metal matrices, potentially altering the electrical and mechanical properties of the joint.
'Chill Out' with TopLine’s President Martin Hart to Discuss Cold Electronics at SPWG 2025
05/02/2025 | TopLineBraided Solder Columns can withstand the rigors of deep space cold and cryogenic environments, and represent a robust new solution to challenges facing next generation large packages in electronics assembly.
BEST Inc. Reports Record Demand for EZReball BGA Reballing Process
05/01/2025 | BEST Inc.BEST Inc., a leader in electronic component services, is pleased to announce they are experiencing record demand for their EZReball™ BGA reballing process which greatly simplifies the reballing of ball grid array (BGA) and chip scale package (CSP) devices.