-
-
News
News Highlights
- Books
Featured Books
- design007 Magazine
Latest Issues
Current IssueAll About That Route
Most designers favor manual routing, but today's interactive autorouters may be changing designers' minds by allowing users more direct control. In this issue, our expert contributors discuss a variety of manual and autorouting strategies.
Creating the Ideal Data Package
Why is it so difficult to create the ideal data package? Many of these simple errors can be alleviated by paying attention to detail—and knowing what issues to look out for. So, this month, our experts weigh in on the best practices for creating the ideal design data package for your design.
Designing Through the Noise
Our experts discuss the constantly evolving world of RF design, including the many tradeoffs, material considerations, and design tips and techniques that designers and design engineers need to know to succeed in this high-frequency realm.
- Articles
- Columns
- Links
- Media kit
||| MENU - design007 Magazine
Estimated reading time: 2 minutes
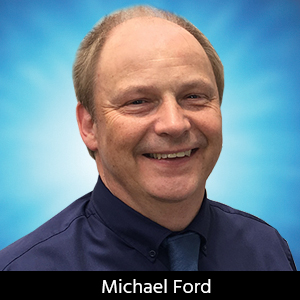
Accelerating Tech: Standards-driven, Digital Design Flow for Industry 4.0
The term “fragmented manufacturing” is a good way to describe current assembly manufacturing challenges in an Industry 4.0 environment. Even in Germany, productivity reportedly continues to decline. To reach the upside of Industry 4.0, data flows relating to design play a major role—one that brings significant opportunity to the overall assembly business.
The assembly sector always complains about the increasing mix of products that are being scheduled together with lower volumes. It’s ironic when we consider the massive growth in the application of electronics into virtually every device that we use. Surely, that means that volumes overall should be going up.
Unfortunately, the industry has become like an old, mechanical hard disk. We are trying to squeeze through more and more data into a device that appears to be working more slowly, but the files on the disk have become fragmented. Instead of the data being stored in one long group record, files are split up into many pieces and stored in different places on the disk. It is as if instead of going to the supermarket, you have to pick up groceries from many shops on the high street, one by one. Windows 10 now turns on periodic hard-disk defragmentation automatically, so most people don’t even notice this issue anymore. Can we do the same in our assembly manufacturing plants?
Assemblers have been driven to reduce or eliminate finished goods stock from the warehouse all the way through to the customer with direct shipping preferred over the investment of stock in an expansive distribution chain and risk of depreciation as market demands change. This is in part a great opportunity for the resurgence of local manufacturing and a key driver of Industry 4.0. The assembly schedule, therefore, has to meet the almost daily requirements of the customer, over the complete range of products made. Hence, the high-mix and low-volume scenario.
As this is a long-term significant business driver, assembly cannot continue to cling to the paradigm of optimized long-term planning as core parameters change every day. What is really needed is a way to manage the allocation of products to assembly line configurations immediately in a way that optimizes the utilization of resources. Accepting that we have to visit individual stores on the high street does not preclude us from planning to visit them in an efficient fashion, creating a sequenced journey that minimizes the walking distance from one to another.
Having seen the evolution of the core business requirement, Aegis Software has been driving industry change through the use of new technology based on standards for some time. Assembly engineering and manufacturing are now going through a fundamental change to address the production fragmentation problem. Adaptive planning is a critical new solution within a modern digital engineering solution. The best practice flow is to receive the complete product design data inclusive of all required documentation related to the intent of how a product should be built.
To read this entire column, which appeared in the April 2019 issue of Design007 Magazine, click here.
More Columns from Smart Factory Insights
Smart Factory Insights: Making Rework a Smart Business OpportunitySmart Factory Insights: The Sustainability Gold Rush
Smart Factory Insights: Today’s Manufacturing Jobs Require a New Skill Set
Smart Factory Insights: Compose Yourself, Mr. Ford
Smart Factory Insights: The Smart Business Case for Local PCB Manufacturing
Smart Factory Insights: Manufacturing Digital Twin—Spanners in the Works
Smart Factory Insights: Machines, People, and AI
Smart Factory Insights: Is Sustainability in Manufacturing a Benefit or Burden?