-
- News
- Books
Featured Books
- design007 Magazine
Latest Issues
Current IssueShowing Some Constraint
A strong design constraint strategy carefully balances a wide range of electrical and manufacturing trade-offs. This month, we explore the key requirements, common challenges, and best practices behind building an effective constraint strategy.
All About That Route
Most designers favor manual routing, but today's interactive autorouters may be changing designers' minds by allowing users more direct control. In this issue, our expert contributors discuss a variety of manual and autorouting strategies.
Creating the Ideal Data Package
Why is it so difficult to create the ideal data package? Many of these simple errors can be alleviated by paying attention to detail—and knowing what issues to look out for. So, this month, our experts weigh in on the best practices for creating the ideal design data package for your design.
- Articles
- Columns
- Links
- Media kit
||| MENU - design007 Magazine
Estimated reading time: 1 minute
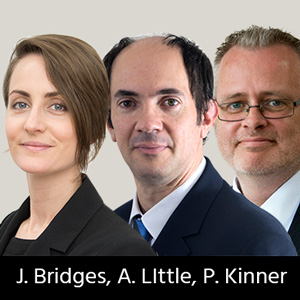
Sensible Design: Five Tips to Further Improve Resin Encapsulant Performance
In the second of my recent columns on resin potting and encapsulation, I will expand on my previous Q&A guide on the subject with further advice on selection and application.
Keeping to our tried and trusted five-point Q&A format, I am returning to the subject of potting and encapsulation with a few more pointers to help steer you in the direction of making appropriate resin choices—and, hopefully, away from problems that you are more than likely to encounter on the way. Initially, here’s a little primer to whet your appetite.
There are a number of different factors that influence the protection afforded by potting compounds. The act of encapsulating a component or PCB means that it is surrounded by a layer of resin, which completely seals a component or an entire PCB from the environment in which it operates. When mixed, a two-part resin starts a chemical reaction, which results in the resin becoming fully polymerised to provide a homogenous layer. The polymerisation reaction creates a three-dimensional structure, which provides a barrier against chemical attack and high humidity, physical shocks, and the potentially destructive effects of thermal cycling.
Now, let’s refer to our questions.
1. What typical applications use epoxy resins?
Epoxies are typically used where extremes of temperature and chemically aggressive environments are encountered. Under-hood applications are common, and epoxies are often used to protect the huge variety of sensors, digital electronics, and connectors that abound beneath the hood of a modern automobile not just from high temperatures but also from volatile fuels and lubricants.
Even as we switch from the internal combustion engine to the electric motor, the chemical environment might change, but the requirements for chemically resistant potting resins capable of tolerating a wide temperature range and resisting chemical attack will remain. Their excellent adhesion to a wide range of substrates means that epoxies are used to ensure that the electronics are also very effectively sealed against the external environment and are perfectly adapted for use in equipment destined for deployment in ATEX and other hazardous areas.
To read this entire column, which appeared in the April 2019 issue of Design007 Magazine, click here.
More Columns from Sensible Design
Sensible Design: Automotive Conformal Coating ApplicationsSensible Design: Green Coats Are In
Sensible Design: Encapsulation Resins—PU vs. Epoxy
Sensible Design: Avoiding Conformal Coating Pitfalls
Sensible Design: Comparing Traditional and Bio-based Resins
Sensible Design: All Resins Are Not Created Equal
Sensible Design: Can Solvent-free UV-cure Coatings Increase Stability and Throughput?
Sensible Design: Optimize Your Thermal Management