Collaboratively Creating Wearable Medical Products
May 28, 2019 | I-Connect007 Editorial TeamEstimated reading time: 5 minutes
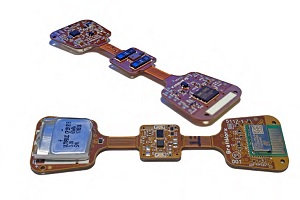
Patty Goldman, Barry Matties, and Happy Holden recently spoke with David Moody and Rich Clemente of Lenthor Engineering along with Anthony Flattery and Amit Rushi—their customers at GraftWorx. They discussed a recent project and how they worked together to solve a difficult problem by designing a rigidized flex circuit for their product.
Patty Goldman: Tony and Amit, thanks so much for joining us today to talk about your project with Lenthor.
Anthony Flannery: We had a number of different challenges that were unique to our product. It was fantastic working with Lenthor. We’re very happy with how the final product came out.
Barry Matties: Let’s start with some information on your company for our readers. What does your company make?
Amit Rushi: I lead business development product and marketing at GraftWorx, and I’ve been here for about two years. At GraftWorx, we build an end-to-end remote monitoring solution to target fluid management issues in chronic condition patient populations. We realized that a big gap in solving for that was the lack of a continuous-sensing technology that generates clinically actionable cardiovascular metrics, specifically hemodynamic metrics.
We took on this endeavor of creating an end-to-end platform, including making a new, continuous-sensing solution. In our vernacular, we refer to it as a SmartPatch. That journey has gone through its own gyrations to determine the adequate number of sensors, the desired flexibility of the circuit board, and how can we make it truly forgettable in the mind of the patient from a wearable perspective.
We started with the architecture of an end-to-end remote mounting platform but needed to solve for the gap of this continuous-sensing SmartPatch. The first market we’re targeting is dialysis—a patient population that, unfortunately, has a lot of rigor to living their life on dialysis; they go to dialysis treatment three times a week. Then, we’re looking at congestive heart failure or heart failure at large, since 40% of dialysis patients are diagnosed with heart failure. These are two very big markets in need of innovation, especially in supporting the patients’ lives outside of the clinic.
Goldman: Today, we’re here to talk about the topic for this issue, which is “From Design Through Final Product.” Our thought was to follow a product through from the design—the very beginning—through all of your concerns and what happens to make that product a reality. Let’s jump in at the design stage and talk about how everything worked out with Dave and Rich from Lenthor’s perspective. I know the end was good, but what happened in between?
David Moody: Tony, if you could give us a brief description of what determined the ultimate solution, that would be great. For example, it had to be a rigid-flex design from the standpoint of what you were trying to accomplish when you were all sitting around the table with a napkin trying to figure out what to do.
Flannery: It’s funny. We’re all going to sit down and write our memoirs about this company someday. GraftWorx has been around for about six and a half years, and we first cut our teeth on trying to bring a product to market on a monitoring system for peripheral arterial disease.
And there’s a long, convoluted history that goes beyond the scope of this conversation. What we ended up realizing was there was a tremendous opportunity to do this, and we’d get to market faster in the wearable space.
It’s no secret or surprise that there’s a tremendous opportunity in medicine to generate data that can make a huge difference in a clinical outcome. As Amit was describing, we’re trying to generate quality data that goes back to the clinic and has a positive impact on managing patients with a very difficult disease, end-stage renal disease. We wanted to design something that fits into a patient’s lifestyle with very little impact on their lives.
Figure 1: The GraftWorx end-to-end data path. Results from patient monitoring are transmitted via a semi-custom Bluetooth link to our B2H data bridge. Data is transmitted over a cellular IoT network to the Cloud where, after authentication, data is processed and alerts generated. Data and alerts are available to clinicians as part of their standard clinical workflow.
In terms of conveying what we’re trying to do, this is something that sits on your skin, such as a small, smart bandage. We wanted it to move with you and be flexible, comfortable, light, and forgettable. But at the same time, it’s a very sophisticated device. We have 11 different sensor data streams acquired during a reading. There is encryption that goes on so that we’re HIPAA-compliant in terms of how we store and transmit patient data. There is a tremendous optimization that went into power management so that our device lasts as long as it does on the skin, and this data is pulled into our cloud via a medical data relay (Figure 1).
What went into defining this device? Well, one of the things about the medical field that’s interesting is we have four different customers: patients, doctors, clinics, and payers. To answer your question about the journey in terms of starting the design, we have to take all of those players into account when we start laying out our product requirements, which then feed into our design inputs.
Clemente: I think you’re on a nice track. Would it be safe to say that the onset of wearable electronics helped you find a solution?
Flannery: I’m going to take a little hubris at this point and say we are the onset of wearable electronics (laughs). We’re one of the drivers in this field. There are other people on the market, for instance, such as iRhythm, who are out there looking for wearable devices to record EKGs and a number of other players in different spaces.
We’re driven by a need to solve a clinical problem. We’re not a hammer looking for a nail or a technology-driven solution; technology is our tool to solve a genuine clinical need. In a lot of ways, we’re taking the best that technology has to offer and designing it for our own product requirements and needs. We’re driving the revolution, not following on the wave. We like to think of ourselves as at the forefront.
To read the full article, which was originally published in the April 2019 issue of Flex007 Magazine, click here.
Suggested Items
Microchip Enters into Partnership Agreement with Delta Electronics on Silicon Carbide Solutions
07/18/2025 | Globe NewswireThe growth of artificial intelligence (AI) and the electrification of everything are driving an ever-increasing demand for higher levels of power efficiency and reliability.
ESD Alliance Reports Electronic System Design Industry Posts $5.1 Billion in Revenue in Q1 2025
07/16/2025 | SEMIElectronic System Design (ESD) industry revenue increased 12.8% to $5,098.3 million in the first quarter of 2025 from the $4,521.6 million registered in the first quarter of 2024, the ESD Alliance, a SEMI Technology Community, announced in its latest Electronic Design Market Data (EDMD) report.
Beyond Design: Refining Design Constraints
07/17/2025 | Barry Olney -- Column: Beyond DesignBefore starting any project, it is crucial to develop a thorough plan that encompasses all essential requirements. This ensures that the final product not only aligns with the design concept but is also manufacturable, reliable, and meets performance expectations. High-speed PCB design requires us to not only push technological boundaries but also consider various factors related to higher frequencies, faster transition times, and increased bandwidths during the design process.
Prague PEDC: Call for Abstracts Deadline July 31
07/16/2025 | Pan-European Electronics Design Conference (PEDC)The second Pan-European Electronics Design Conference (PEDC) will take place Jan. 21-22, 2026, in Prague, Czech Republic. The call for abstracts deadline is July 31. Organized jointly by the German Electronics Design and Manufacturing Association (FED) and the Global Electronics Association PEDC serves as a European platform for knowledge exchange, networking, and innovation in electronics design and development.
The Pulse: Design Constraints for the Next Generation
07/17/2025 | Martyn Gaudion -- Column: The PulseIn Europe, where engineering careers were once seen as unpopular and lacking street credibility, we have been witnessing a turnaround in the past few years. The industry is now welcoming a new cohort of designers and engineers as people are showing a newfound interest in the profession.