-
-
News
News Highlights
- Books
Featured Books
- design007 Magazine
Latest Issues
Current IssueAll About That Route
Most designers favor manual routing, but today's interactive autorouters may be changing designers' minds by allowing users more direct control. In this issue, our expert contributors discuss a variety of manual and autorouting strategies.
Creating the Ideal Data Package
Why is it so difficult to create the ideal data package? Many of these simple errors can be alleviated by paying attention to detail—and knowing what issues to look out for. So, this month, our experts weigh in on the best practices for creating the ideal design data package for your design.
Designing Through the Noise
Our experts discuss the constantly evolving world of RF design, including the many tradeoffs, material considerations, and design tips and techniques that designers and design engineers need to know to succeed in this high-frequency realm.
- Articles
- Columns
- Links
- Media kit
||| MENU - design007 Magazine
Stitching Capacitor: Crosstalk Mitigation for Return Path Discontinuity
June 13, 2019 | Chang Fei Yee, Keysight TechnologiesEstimated reading time: 2 minutes
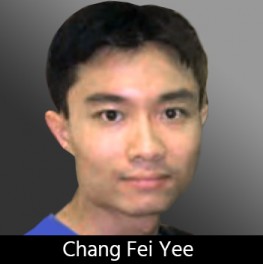
This article discusses the impact of stitching capacitors in mitigating signal crosstalk due to return path discontinuity during layer transition on PCB. The investigation was performed with 3DEM simulation using Keysight EMPro.
Introduction
In electronic systems, signal transmission exists in a close loop form. The forward current propagates from transmitter to receiver through the signal trace. On the contrary, the return current travels backward from receiver to transmitter through the power or ground plane right underneath the signal trace that serves as the reference or return path. The path of the forward current and return current forms a loop inductance. It is important to route the high-speed signal on a continuous reference plane so that the return current can propagate on the desired path, directly beneath the signal trace.
When the return path is broken due to the switching of reference planes with different potential, e.g., from ground to power or vice versa after layer transition on PCB, the return current might detour and propagate on a longer path, which causes a rise in loop inductance. This might lead to the sharing of a common return path by different signals that pose a high risk of interference among the signals due to higher mutual inductance. This interference results in signal crosstalk. To mitigate the crosstalk due to return path discontinuity (RPD), stitching capacitors are mounted on the PCB to serve as a bridge between the two reference planes of interest on different PCB layers.
Analysis of Signal Crosstalk
To investigate the impact of stitching capacitor in mitigating signal crosstalk due to RPD during layer transition on PCB, three simulation models of 3DEM are constructed. In model 1A (Figure 1), two signal traces with 50 ohm characteristic impedance in single-ended mode on the top PCB layer transition to the bottom layer using vias. Each segment of the signal traces on top and bottom layers is 100 mil long and 5 mil wide. Meanwhile, the diameters of the via barrel and pad are 5 mil and 7 mil respectively. The PCB stackup shown in Figure 2 is applied to this 3D model, where solid planes exist on layer 2 and 3. All the four copper layers are 1.2 mil thick and FR-4 material is used as the PCB substrate.
The two signal traces are 15 mil apart, which is triple the signal trace width for minimum crosstalk due to forward current propagation. A stitching via is placed 20 mil off each signal via, connected to the reference plane on layer 2 and extending to layer 4. However, voids are placed on the layer 3 reference plane to break the electrical connectivity between the planes on layer 2 and 3. This simulates the effect of RPD on signal crosstalk by switching the reference from ground to power or vice versa after the signal layer transition through the via.
To read this entire article, which appeared in the June 2019 issue of Design007 Magazine, click here.
Suggested Items
The Evolution of Picosecond Laser Drilling
06/19/2025 | Marcy LaRont, PCB007 MagazineIs it hard to imagine a single laser pulse reduced not only from nanoseconds to picoseconds in its pulse duration, but even to femtoseconds? Well, buckle up because it seems we are there. In this interview, Dr. Stefan Rung, technical director of laser machines at Schmoll Maschinen GmbH, traces the technology trajectory of the laser drill from the CO2 laser to cutting-edge picosecond and hybrid laser drilling systems, highlighting the benefits and limitations of each method, and demonstrating how laser innovations are shaping the future of PCB fabrication.
Day 2: More Cutting-edge Insights at the EIPC Summer Conference
06/18/2025 | Pete Starkey, I-Connect007The European Institute for the PCB Community (EIPC) summer conference took place this year in Edinburgh, Scotland, June 3-4. This is the third of three articles on the conference. The other two cover Day 1’s sessions and the opening keynote speech. Below is a recap of the second day’s sessions.
Day 1: Cutting Edge Insights at the EIPC Summer Conference
06/17/2025 | Pete Starkey, I-Connect007The European Institute for the PCB Community (EIPC) Summer Conference took place this year in Edinburgh, Scotland, June 3-4. This is the second of three articles on the conference. The other two cover the keynote speeches and Day 2 of the technical conference. Below is a recap of the first day’s sessions.
Preventing Surface Prep Defects and Ensuring Reliability
06/10/2025 | Marcy LaRont, PCB007 MagazineIn printed circuit board (PCB) fabrication, surface preparation is a critical process that ensures strong adhesion, reliable plating, and long-term product performance. Without proper surface treatment, manufacturers may encounter defects such as delamination, poor solder mask adhesion, and plating failures. This article examines key surface preparation techniques, common defects resulting from improper processes, and real-world case studies that illustrate best practices.
RF PCB Design Tips and Tricks
05/08/2025 | Cherie Litson, EPTAC MIT CID/CID+There are many great books, videos, and information online about designing PCBs for RF circuits. A few of my favorite RF sources are Hans Rosenberg, Stephen Chavez, and Rick Hartley, but there are many more. These PCB design engineers have a very good perspective on what it takes to take an RF design from schematic concept to PCB layout.