-
- News
- Books
Featured Books
- design007 Magazine
Latest Issues
Current IssueShowing Some Constraint
A strong design constraint strategy carefully balances a wide range of electrical and manufacturing trade-offs. This month, we explore the key requirements, common challenges, and best practices behind building an effective constraint strategy.
All About That Route
Most designers favor manual routing, but today's interactive autorouters may be changing designers' minds by allowing users more direct control. In this issue, our expert contributors discuss a variety of manual and autorouting strategies.
Creating the Ideal Data Package
Why is it so difficult to create the ideal data package? Many of these simple errors can be alleviated by paying attention to detail—and knowing what issues to look out for. So, this month, our experts weigh in on the best practices for creating the ideal design data package for your design.
- Articles
- Columns
- Links
- Media kit
||| MENU - design007 Magazine
Estimated reading time: 2 minutes
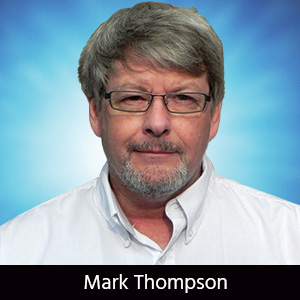
The Bare (Board) Truth: Fabrication Starts With Solid Design Practices
“All right! Don’t rush me. I’m a-thinking…and my head hurts.” —Yosemite Sam
It’s a fact: Great board design is the key to a great PCB. I’m even more certain of this after spending two days in a wonderful class presented by Rick Hartley titled “Control of Noise, EMI, and Signal Integrity in High-speed Circuits and PCBs.”
First, I would like to thank Rick for teaching his course. I thought I had a pretty decent grasp of controlled impedance and signal integrity, but the gaps in my knowledge base can fill the Grand Canyon. This class helped me see how important the design truly is not only for functionality but also for minimizing revisions and passing EMI testing the first time. I deal with incoming designs for a living, but I had no idea how many things you should consider when doing a board layout, from part placement and organization to via location.
I guess I am just accustomed to simply using my field solver and answering fabrication-related questions to make a PCB producible. I thought I knew it all, from effective Dk and Er to layer “nesting” based on the layer interfaces and prepreg selection for various controlled impedance structures. I assumed I knew what I needed to know from how the color and dielectric of a mask can affect controlled impedances to the use of ultra-thin dielectrics to increase inductance to pass EMI. Well, I was wrong!
How far we have come from the days of slower-speed designs; their edge rates didn’t matter very much because they were are basically lumped elements. Those old designs are nothing like today’s high-speed designs and all the bugaboos associated with distributed length line designs. Understanding the impact of nearby traces on controlled impedance lines and how magnetic fields work can make the difference between a successful design and a quagmire of self-created issues, such as common-mode emissions that can make or break passing EMI testing.
I even learned a few things about via filling with silver-epoxy or copper-epoxy for thermal applications. Remember, if you are using a via fill for conductivity, you are missing the point; the electromagnetic fields are generated around the barrel of the holes, not the material filling the hole. In some cases during Rick’s presentation, I wanted to slap myself in the forehead and say, “I should have had a V-8!”
Rick showed one slide with four examples to be rated from least to most of radiated EMI. Fortunately, they are the same as a firing order in most four-cylinder combustion engines (1, 3, 4, 2) and pretty much everyone understood not to rout a trace over a split or a slot.
On many occasions during Rick’s presentation, I began to make sense of some of the crazy things we have been asked as a fabricator over the years. Eight years ago, one customer asked us to mill a channel in a thick PCB using an end mill to make the corners as square as possible (not routed with a radii) and plate the trough and cap the whole structure with what appeared to be a wide plated “trace” running the entire length and width of the channel. At either end was a small hole where I was told they would inject a liquid. Then, I saw Rick’s slide saying, “Apply a wave whose half wavelength is equal to distance X. We have a perfect balance and a true waveguide.”
To read this entire column, which appeared in the June 2019 issue of Design007 Magazine, click here.
More Columns from The Bare (Board) Truth
The Bare (Board) Truth: My Top Six Design ChallengesThe Bare (Board) Truth: Via Basics
The Bare (Board) Truth: 5 Questions About Improving Thermal Management
The Bare (Board) Truth: Teaching the Next Generation—An Overview of Today’s University Courses
Board Negotiations: Design Rules and Tolerances
The Bare (Board) Truth: Eliminate Confusion
The Bare (Board) Truth: Getting on the Same Page—A Data Story
The Bare (Board) Truth: Refining Output Data Packages for Fabricators