-
-
News
News Highlights
- Books
Featured Books
- design007 Magazine
Latest Issues
Current IssueAll About That Route
Most designers favor manual routing, but today's interactive autorouters may be changing designers' minds by allowing users more direct control. In this issue, our expert contributors discuss a variety of manual and autorouting strategies.
Creating the Ideal Data Package
Why is it so difficult to create the ideal data package? Many of these simple errors can be alleviated by paying attention to detail—and knowing what issues to look out for. So, this month, our experts weigh in on the best practices for creating the ideal design data package for your design.
Designing Through the Noise
Our experts discuss the constantly evolving world of RF design, including the many tradeoffs, material considerations, and design tips and techniques that designers and design engineers need to know to succeed in this high-frequency realm.
- Articles
- Columns
- Links
- Media kit
||| MENU - design007 Magazine
Estimated reading time: 2 minutes
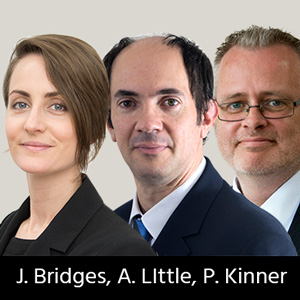
Sensible Design: Resins Fit for a Purpose—Failure Mitigation and Environmental Concerns
So far, in my columns on resin chemistries and encapsulation/potting techniques, I have tended to concentrate on the properties of these materials. My insights have included how they are best applied in the factory, and the steps that must be taken to get the best performance from them once they are in the field to protect an electronic assembly or lighting fixture against the elements. In this column, I am going to address the question of resin failures—in particular, how to avoid them—and to get a better idea of where and how appropriately selected and applied modern resins are making a big difference in the world of extreme electronics installation and implementation.
Regarding resin failures and how to avoid them, there are some excellent, well-formulated resins out there that will deliver unfailing service as long as they are carefully selected for the anticipated conditions, stored appropriately, and applied and cured according to the manufacturer’s recommendations. One lapse in this sequence and you are likely to have a problem on your hands that may manifest itself on the test bench if you are lucky. But if you are very unlucky, it will manifest sometime later when a unit is already in service and likely to be operating in some hazardous or otherwise difficult-to-access location.
There are a number of simple steps that you can follow to reduce incidences of resin failure, and, at best, help you avoid them altogether. First, always read the product manufacturer’s technical data sheet; this will at least guide you on basic requirements, such as ensuring that the correct storage conditions for the product are being maintained. Operate good stock rotation so that the resin is not left in storage for a prolonged length of time, and always make sure that containers are kept well sealed.
Second, it is vital to ensure that the correct mix ratio for two-component resins is achieved. For medium- to large-production volumes, the use of a mixing machine is recommended to minimise the risk of variability in the mix ratio across a production run. It is important that all pipework used with these machines is bled properly so there isn’t any air present in the system, which could result in mix ratio variations or air entrapment in the resin.
It is always wise to carry out regular checks on the amount of each component being dispensed if a machine is used. And if manual mixing is preferred, such as for short runs and/or prototyping, it is advisable to use calibrated balances to measure each component. Only pour the amount of resin required for the job in hand and be sure to reseal containers without delay.
To read this entire column, which appeared in the June 2019 issue of Design007 Magazine, click here.
More Columns from Sensible Design
Sensible Design: Automotive Conformal Coating ApplicationsSensible Design: Green Coats Are In
Sensible Design: Encapsulation Resins—PU vs. Epoxy
Sensible Design: Avoiding Conformal Coating Pitfalls
Sensible Design: Comparing Traditional and Bio-based Resins
Sensible Design: All Resins Are Not Created Equal
Sensible Design: Can Solvent-free UV-cure Coatings Increase Stability and Throughput?
Sensible Design: Optimize Your Thermal Management