-
- News
- Books
Featured Books
- design007 Magazine
Latest Issues
Current IssueShowing Some Constraint
A strong design constraint strategy carefully balances a wide range of electrical and manufacturing trade-offs. This month, we explore the key requirements, common challenges, and best practices behind building an effective constraint strategy.
All About That Route
Most designers favor manual routing, but today's interactive autorouters may be changing designers' minds by allowing users more direct control. In this issue, our expert contributors discuss a variety of manual and autorouting strategies.
Creating the Ideal Data Package
Why is it so difficult to create the ideal data package? Many of these simple errors can be alleviated by paying attention to detail—and knowing what issues to look out for. So, this month, our experts weigh in on the best practices for creating the ideal design data package for your design.
- Articles
- Columns
- Links
- Media kit
||| MENU - design007 Magazine
This Month in Design007 Magazine: What Did You Expect From Me, Anyway?
May 14, 2020 | Todd Westerhoff, Mentor, a Siemens businessEstimated reading time: 2 minutes
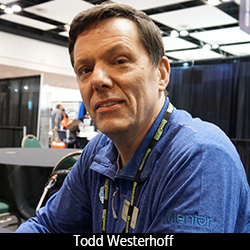
As engineers, we work in the middle of a (usually long) process chain. Product requirements come from the front of the chain (marketing), the products we create are physically realized at the back of the chain (“production”), and hopefully get sold to customers who enjoy them and buy more.
It’s sort of like working on an intellectual assembly line—we get requirements and data as input, perform our particular task, and then provide our output as requirements and data to the next person on down the line. It seems easy enough. So, why is it that so many of the requirements we’re supposed to meet and so much of the data we receive is downright bad?
To be fair, “hard data” is usually okay. Component dimensions, material properties, pinout definitions, etc., all tend to be correct because, without that, reliable manufacturing would be impossible. It’s the soft stuff that tends to be the problem. In the case of signal integrity, it’s the simulation models we receive from vendors or clear guidelines on just what is and isn’t achievable from a board layout standpoint or manufacturing cost standpoint that make the analysis job difficult. Sorting through problems with data requires time that no one seems to have—at least, in the world as it existed three months ago—and any delay associated with vetting and reacquiring data presents a huge problem.
Example Issues
Why does this happen? While not an exhaustive list by any means, these are some of the issues I’ve seen.
Poor Definition of Requirements
Simulation models are a great example— even though the syntax for simulation models is well defined, there’s really no good way to assess simulation model quality or fitness for a particular analysis. In my hardware design days, I noted that just about every analysis project had some simulation models show up past the period we had reserved to test them, so we just gave them a quick test and got to work instead. Without fail, we’d use the models for a week or so before problems popped up and realized our analysis had been compromised. It was a 2–3 week hit, every time.
Sometimes the list of items to be delivered just isn’t complete or clear enough, and only part of the information needed is provided. The time it takes to go back to the source and acquire the additional data (and justify why they should take the time to provide it) causes project downtime.
To read this entire feature, which appeared in the May 2020 issue of Design007 Magazine, click here.
Suggested Items
NEPCON ASIA 2025: Innovating Smart Manufacturing Ecosystems and Bridging Global Opportunities
07/11/2025 | PRNewswireTaking place from October 28 to 30, 2025 at the Shenzhen World Exhibition & Convention Center (Bao'an), NEPCON ASIA is the premier platform to discover the latest technologies and market trends, connect with new suppliers and products, and explore potential partnerships and distribution opportunities.
Mycronic Delivers Strong Q2 Performance and Raises 2025 Outlook to SEK 7.5 Billion
07/11/2025 | MycronicMycronic reported a 35% increase in Q2 net sales and a 27% EBIT margin, prompting an upward revision of its full-year 2025 revenue forecast to SEK 7.5 billion.
Cetec ERP Expands into Larger Office to Support Continued Growth
07/11/2025 | Cetec ERPCetec ERP, a leading provider of cloud-based ERP software for manufacturers, has officially relocated to a larger, modern office facility in central Austin as of July 2, 2025.
Digital Twin Concept in Copper Electroplating Process Performance
07/11/2025 | Aga Franczak, Robrecht Belis, Elsyca N.V.PCB manufacturing involves transforming a design into a physical board while meeting specific requirements. Understanding these design specifications is crucial, as they directly impact the PCB's fabrication process, performance, and yield rate. One key design specification is copper thieving—the addition of “dummy” pads across the surface that are plated along with the features designed on the outer layers. The purpose of the process is to provide a uniform distribution of copper across the outer layers to make the plating current density and plating in the holes more uniform.
Kitron Reports Strengthening Momentum in Q2 2025
07/10/2025 | KitronKitron reported solid quarterly sales and profits, particularly driven by the Defence & Aerospace market sector.