Documenting Your Flex Circuit Design
September 16, 2020 | Tony Plemel, Flexible Circuit TechnologiesEstimated reading time: 1 minute
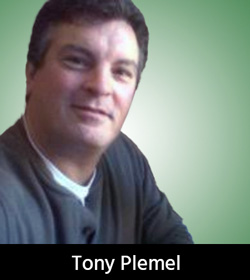
As a flex circuit applications engineer, when I receive an RFQ, the first thing I do is look at the customer’s data and review their manufacturing notes. Quite often, I find notes that supersede IPC specifications in manufacturing documents, as customers often believe these added notes and associated specifications will make the circuit more robust. However, these non-standard IPC manufacturing specifications/notes can wreak havoc on the manufacturing process and can actually lead to a less robust circuit.
For example, a customer will sometimes specify additional copper plating, believing it will result in a more reliable circuit. In reality, that type of requirement can make the circuit less reliable, more difficult to manufacture, and more expensive. When manufacturing yields go down, the price goes up!
In taking a deeper dive into manufacturing notes and the potential issues that they can create, let’s use a three-layer multilayer flexible circuit as an example. The first note on a manufacturing print is usually “Manufacture to IPC6013, Class 2, Type 3.” This note should always be included; I cannot stress that enough!
Unfortunately, in the continued review of the documentation, I often find one or more additional conflicting notes further down in the manufacturing notes that overrule IPC6013 specifications.
Copper Plating
One example would be “Minimum copper plating shall be 0.0015”.” This note supersedes the IPC-6013 specification in Table 1.
Table 1: IPC-6013 copper plating requirements.
PCB designers who are not well-versed in flex circuit manufacturing may not know that exceeding IPC-6013 of 984 µin (0.000984”) can cause the circuit to be less reliable and possibly cause problems later in the manufacturing process. Having a specified requirement this large (0.000516” thicker) will require the plating line at the factory to plate more than 0.0015” to ensure the minimum plating is 0.0015” thick.
To read this entire article, which appeared in the September 2020 issue of Design007 Magazine, click here.
Suggested Items
I-Connect007 Editor’s Choice: Five Must-Reads for the Week
07/11/2025 | Andy Shaughnessy, Design007 MagazineThis week, we have quite a variety of news items and articles for you. News continues to stream out of Washington, D.C., with tariffs rearing their controversial head again. Because these tariffs are targeted at overseas copper manufacturers, this news has a direct effect on our industry.I-Connect007 Editor’s Choice: Five Must-Reads for the Week
Digital Twin Concept in Copper Electroplating Process Performance
07/11/2025 | Aga Franczak, Robrecht Belis, Elsyca N.V.PCB manufacturing involves transforming a design into a physical board while meeting specific requirements. Understanding these design specifications is crucial, as they directly impact the PCB's fabrication process, performance, and yield rate. One key design specification is copper thieving—the addition of “dummy” pads across the surface that are plated along with the features designed on the outer layers. The purpose of the process is to provide a uniform distribution of copper across the outer layers to make the plating current density and plating in the holes more uniform.
Trump Copper Tariffs Spark Concern
07/10/2025 | I-Connect007 Editorial TeamPresident Donald Trump stated on July 8 that he plans to impose a 50% tariff on copper imports, sparking concern in a global industry whose output is critical to electric vehicles, military hardware, semiconductors, and a wide range of consumer goods. According to Yahoo Finance, copper futures climbed over 2% following tariff confirmation.
Happy’s Tech Talk #40: Factors in PTH Reliability—Hole Voids
07/09/2025 | Happy Holden -- Column: Happy’s Tech TalkWhen we consider via reliability, the major contributing factors are typically processing deviations. These can be subtle and not always visible. One particularly insightful column was by Mike Carano, “Causes of Plating Voids, Pre-electroless Copper,” where he outlined some of the possible causes of hole defects for both plated through-hole (PTH) and blind vias.
Trouble in Your Tank: Can You Drill the Perfect Hole?
07/07/2025 | Michael Carano -- Column: Trouble in Your TankIn the movie “Friday Night Lights,” the head football coach (played by Billy Bob Thornton) addresses his high school football team on a hot day in August in West Texas. He asks his players one question: “Can you be perfect?” That is an interesting question, in football and the printed circuit board fabrication world, where being perfect is somewhat elusive. When it comes to mechanical drilling and via formation, can you drill the perfect hole time after time?