-
- News
- Books
Featured Books
- design007 Magazine
Latest Issues
Current IssueShowing Some Constraint
A strong design constraint strategy carefully balances a wide range of electrical and manufacturing trade-offs. This month, we explore the key requirements, common challenges, and best practices behind building an effective constraint strategy.
All About That Route
Most designers favor manual routing, but today's interactive autorouters may be changing designers' minds by allowing users more direct control. In this issue, our expert contributors discuss a variety of manual and autorouting strategies.
Creating the Ideal Data Package
Why is it so difficult to create the ideal data package? Many of these simple errors can be alleviated by paying attention to detail—and knowing what issues to look out for. So, this month, our experts weigh in on the best practices for creating the ideal design data package for your design.
- Articles
- Columns
- Links
- Media kit
||| MENU - design007 Magazine
DFM 101: Final Finishes—Electrolytic Nickel/Gold
January 30, 2023 | Anaya Vardya, American Standard CircuitsEstimated reading time: 1 minute
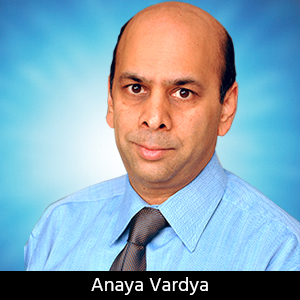
Introduction
One of the biggest challenges facing PCB designers is not understanding the cost drivers in the PCB manufacturing process. This article is the latest in a series that will discuss these cost drivers (from the PCB manufacturer’s perspective) and the design decisions that will impact product reliability.
Final Finishes
Final finishes provide a surface for the component assembler to solder, wire bond, or conductively attach a component pad or lead to a pad, hole, or area of a PCB. The other use for a final finish is to provide a known contact resistance and life cycle for connectors, keys, or switches. The primary purpose of a final finish is to create electrical and thermal continuity with a surface of the PCB.
There are several final finishes in use in the industry today. These include:
- ENIG (electroless nickel, immersion gold)
- ENIPIG (electroless nickel, immersion palladium, immersion gold)
- ENEPIG (electroless nickel, electroless palladium, immersion gold)
- ImmAg (immersion silver)
- ImmSn (immersion tin)
- Sulfamate nickel/hard or soft gold (electrolytic nickel/gold)
- HASL (hot air solder leveling)
- SnPb (63/37 tin/lead)
- LF (lead-free)
- OSP (organic solderability preservative)
Final finishes are primarily application driven, so there are several considerations that should be part of any decision to choose a final finish:
- Lead-tolerant or lead-free (LF) process
- Shelf life
- Flatness
- Lead or ball pitch
- Wire bondability
- Lead insertion
- Solder joint integrity
- Corrosion resistance
- Potential problems
- Cost
To read this entire article, which appeared in the December 2022 issue of Design007 Magazine, click here.
Suggested Items
Silicon Mountain Contract Services Enhances SMT Capabilities with New HELLER Reflow Oven
07/17/2025 | Silicon Mountain Contract ServicesSilicon Mountain Contract Services, a leading provider of custom electronics manufacturing solutions, is proud to announce a significant upgrade to its SMT production capability with the addition of a HELLER 2043 MK5 10‑zone reflow oven to its Nampa facility.
Knocking Down the Bone Pile: Addressing End-of-life Component Solderability Issues, Part 4
07/16/2025 | Nash Bell -- Column: Knocking Down the Bone PileIn 1983, the Department of Defense identified that over 40% of military electronic system failures in the field were electrical, with approximately 50% attributed to poor solder connections. Investigations revealed that plated finishes, typically nickel or tin, were porous and non-intermetallic.
SHENMAO Strengthens Semiconductor Capabilities with Acquisition of PMTC
07/10/2025 | SHENMAOSHENMAO America, Inc. has announced the acquisition of Profound Material Technology Co., Ltd. (PMTC), a premier Taiwan-based manufacturer of high-performance solder balls for semiconductor packaging.
KYZEN to Highlight Understencil and PCB Cleaners at SMTA Querétaro Expo and Tech Forum
07/09/2025 | KYZEN'KYZEN, the global leader in innovative environmentally responsible cleaning chemistries, will exhibit at the SMTA Querétaro Expo & Tech Forum, scheduled to take place Thursday, July 24, at Centro de Congresos y Teatro Metropolitano de Querétaro.
Driving Innovation: Direct Imaging vs. Conventional Exposure
07/01/2025 | Simon Khesin -- Column: Driving InnovationMy first camera used Kodak film. I even experimented with developing photos in the bathroom, though I usually dropped the film off at a Kodak center and received the prints two weeks later, only to discover that some images were out of focus or poorly framed. Today, every smartphone contains a high-quality camera capable of producing stunning images instantly.