-
- News
- Books
Featured Books
- design007 Magazine
Latest Issues
Current IssueShowing Some Constraint
A strong design constraint strategy carefully balances a wide range of electrical and manufacturing trade-offs. This month, we explore the key requirements, common challenges, and best practices behind building an effective constraint strategy.
All About That Route
Most designers favor manual routing, but today's interactive autorouters may be changing designers' minds by allowing users more direct control. In this issue, our expert contributors discuss a variety of manual and autorouting strategies.
Creating the Ideal Data Package
Why is it so difficult to create the ideal data package? Many of these simple errors can be alleviated by paying attention to detail—and knowing what issues to look out for. So, this month, our experts weigh in on the best practices for creating the ideal design data package for your design.
- Articles
- Columns
- Links
- Media kit
||| MENU - design007 Magazine
Estimated reading time: 1 minute
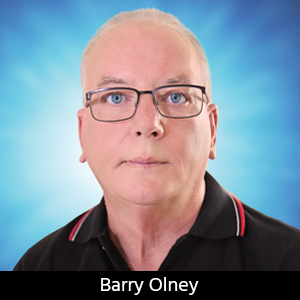
Material Selection for Digital Design
In a previous column, Material Selection for SERDES Design, I pointed out that materials used for the fabrication of the multilayer PCB absorb high frequencies and reduce edge rates and that loss, in the transmission lines, is a major cause of signal integrity issues. But we are not all designing cutting-edge boards, and sometimes we tend to over-specify requirements that can lead to inflated production costs.
In this column, I will look at what types of materials are commonly used for digital design, and how to select an adequate material to minimize costs. Of course, selecting the best possible material will not hurt, but it may blow out the costs.
Figure 1: Simulated signal propagating through a curved waveguide.
Signals propagate in a vacuum or air at approximately the speed of light. But, as the electromagnetic energy is enveloped in a dielectric material, sandwiched between planes in the PCB medium, it slows down. Figure 1 illustrates a signal propagating through a curved waveguide. This is representative of a typical stripline configuration of a PCB. What needs to be understood is that the signal traces on a PCB simply guide the signal wave, as the electromagnetic energy propagates in the surrounding dielectric material. It is the dielectric material that determines the velocity (v) of propagation of the electromagnetic energy:
Keep in mind that c is the speed of light (in free space) and Er is the dielectric constant of the material (FR-4 is ~4.0). By contrast, the Er of air is 1. Therefore, the velocity of propagation in FR-4 is about half the speed of light or 6 inches per ns. The important concept is that it is the electromagnetic energy that propagates down the transmission line--not electron flow. Electrons flow at about 0.4 inches per second, a snail’s pace by comparison.
Read the full column here.
Editor's Note: This column originally appeared in the August 2014 issue of The PCB Design Magazine.
More Columns from Beyond Design
Beyond Design: Refining Design ConstraintsBeyond Design: The Metamorphosis of the PCB Router
Beyond Design: Radiation and Interference Coupling
Beyond Design: Key SI Considerations for High-speed PCB Design
Beyond Design: Electro-optical Circuit Boards
Beyond Design: AI-driven Inverse Stackup Optimization
Beyond Design: High-speed Rules of Thumb
Beyond Design: Integrated Circuit to PCB Integration