-
- News
- Books
Featured Books
- design007 Magazine
Latest Issues
Current IssueShowing Some Constraint
A strong design constraint strategy carefully balances a wide range of electrical and manufacturing trade-offs. This month, we explore the key requirements, common challenges, and best practices behind building an effective constraint strategy.
All About That Route
Most designers favor manual routing, but today's interactive autorouters may be changing designers' minds by allowing users more direct control. In this issue, our expert contributors discuss a variety of manual and autorouting strategies.
Creating the Ideal Data Package
Why is it so difficult to create the ideal data package? Many of these simple errors can be alleviated by paying attention to detail—and knowing what issues to look out for. So, this month, our experts weigh in on the best practices for creating the ideal design data package for your design.
- Articles
- Columns
- Links
- Media kit
||| MENU - design007 Magazine
IPC Plating Sub-committee 4-14: Surface Finish Specifications
May 27, 2015 | George Milad, UyemuraEstimated reading time: 1 minute
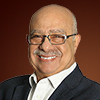
IPC specifications are reference documents to be called out by designers and OEMs. Designers may take exception with one or more items in the specification to ensure that the product meets the requirements of its intended use. The acronym AAUBUS (as agreed upon between user and supplier) is part of any specification.
Specifications are consensus documents. They are agreed upon by a panel of interested industry participants composed of suppliers, manufacturers, assembly houses (CMs) and end-users. The IPC Plating Sub-committee 4-14 is no exception.
When there is consensus, the committee documents it in a specification. In cases where no consensus is readily arrived at, the committee undergoes its own testing in what is commonly referred to as a round-robin (RR) study. In an RR investigation, an agreed-upon test vehicle (TV) is designed and manufactured. TVs are then sent around to the different suppliers who deposit the agreed upon thicknesses to be investigated. The TVs are collected and the deposit thicknesses are verified and documented. The TVs are then coded. The TVs are sent around again to the different testing sites that test for the desired attribute like soldering, contacting and wire bonding capabilities of different finish thicknesses. The data is then collected, sorted out and documented. At this point, a new attempt at consensus is made and upon arrival, the thickness specification is set.
A draft is prepared after consensus is complete. The draft is then posted for peer review. Any IPC member can review the document and suggest technical or editorial changes. All comments are then reviewed and all issues resolved before the final draft is issued. At this time the IPC takes on the task of publishing the document in its final format.
The IPC Plating Sub-committee 4-14 has been active since 2001. It is co-chaired by me and Gerard O’Brien of ST and S Group. The IPC liaison is Tom Newton. The sub-committee has an extensive member list composed of OEMs, contract assemblers, board manufacturers, and chemical suppliers, as well as labs and consultants.
To read this entire article, which appeared in the April issue of The PCB Design Magazine, click here.
Suggested Items
TRI to Exhibit at SMTA Queretaro Expo 2025
07/16/2025 | TRITest Research, Inc. (TRI), the leading provider of test and inspection systems for the electronics manufacturing industry, is pleased to announce plans to exhibit at the SMTA Querétaro Expo 2025, scheduled to take place on July 24, 2025, at the Querétaro Centro de Congresos y Teatro Metropolitano.
Global PCB Connections: Let the Spec Fit the Board, Not Just the Brand
07/17/2025 | Jerome Larez -- Column: Global PCB ConnectionsIf you’ve ever seen an excellent PCB quote delayed, or worse, go cold because of a single line on the fab print, you’re not alone. Often, that line reads something like, “Use 370HR only,” or “IT-180A required.” These and other brand-name materials are proven performers, but unless your design needs that specific resin system (say, for RF performance, thermal reliability, or stringent CAF resistance), you may inadvertently be holding your job hostage.
IPC Hall of Fame Spotlight Series: Highlighting Lionel Fullwood
07/15/2025 | Dan Feinberg, I-Connect007Many IPC members who have contributed significantly to IPC and our industry have been awarded the IPC Raymond E. Pritchard Hall of Fame (HOF) Award. Though many early HOF members have passed away and are unknown to today’s IPC membership, their contributions still resonate. This special series on IPC Hall of Fame members provides a reminder of who was honored and why. As a bonus, for those who are still around, we get to find out what these talented individuals are up to today.
TRI Unveils New Platform for Diverse Board Sizes
07/14/2025 | TRITest Research, Inc. (TRI), the leading test and inspection systems provider for the electronics manufacturing industry, proudly introduces a new size configuration for SPI and AOI Models.
Seeing a Future in Mexico
07/09/2025 | Michelle Te, I-Connect007The Global Electronics Association (formerly known as IPC) has been instrumental in fostering a partnership with Guanajuato, a state north of Mexico City with 12 industrial clusters and close to 150 companies involved in electronics. This past spring, Alejandro Hernández, the undersecretary for investment promotion in Guanajuato, attended IPC APEX EXPO 2025 at the invitation of IPC Mexico Director Lorena Villanueva, where he met with several companies to discuss the opportunities available in Mexico. He is inviting electronics-related companies seeking long-term investment in a centrally located area with access to highways, railways, and ports.