-
- News
- Books
Featured Books
- design007 Magazine
Latest Issues
Current IssueShowing Some Constraint
A strong design constraint strategy carefully balances a wide range of electrical and manufacturing trade-offs. This month, we explore the key requirements, common challenges, and best practices behind building an effective constraint strategy.
All About That Route
Most designers favor manual routing, but today's interactive autorouters may be changing designers' minds by allowing users more direct control. In this issue, our expert contributors discuss a variety of manual and autorouting strategies.
Creating the Ideal Data Package
Why is it so difficult to create the ideal data package? Many of these simple errors can be alleviated by paying attention to detail—and knowing what issues to look out for. So, this month, our experts weigh in on the best practices for creating the ideal design data package for your design.
- Articles
- Columns
- Links
- Media kit
||| MENU - design007 Magazine
Estimated reading time: 1 minute
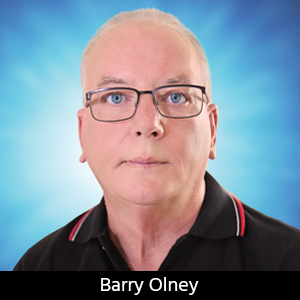
Beyond Design: Stackup Planning, Part 1
The PCB substrate that physically supports the components, links them together via high-speed interconnects and also distributes high-current power to the ICs is the most critical component of the electronics assembly. The PCB is so fundamental that we often forget that it is a component and, like all components, it must be selected based on specifications in order to achieve the best possible performance of the product. Stackup planning involves careful selection of materials and transmission line parameters to avoid impedance discontinuities, unintentional signal coupling and excessive electromagnetic emissions.
The complexity of electronics design is undoubtedly going to increase in the future, presenting a new set of challenges for PCB designers. Materials used for the fabrication of multilayer PCBs absorb high frequencies and reduce edge rates, thus putting the materials selection process under tighter scrutiny. Ensuring that your board stackup and impedances are correctly configured is a good basis for stable performance.
So where do we start? Over the years, I have found that many engineers and PCB designers do not understand the basic structure that makes up a substrate. We all know that multilayer PCBs consist of signal and plane layers, dielectric material and soldermask coating, but there is a lot more to it.
The most popular dielectric material is FR-4 and may be in the form of core or prepreg (pre-impregnated) material. The core material is thin dielectric (cured fiberglass epoxy resin) with copper foil bonded to one or both sides. For instance: Isola's FR406 materials include 5, 8, 9.5, 14, 18, 21, 28, 35, 39, 47, 59 and 93 mil cores. The copper thickness is typically 1/3 to 2 oz. (17 to 70 µm).
The prepreg (B-stage) material is comprised of thin sheets of fiberglass impregnated with uncured epoxy resin which hardens, when heated and pressed, during the PCB fabrication process. Isola’s FR406 materials include 1.7, 2.3, 3.9 and 7.1 mil prepregs that may be combined to achieve thicker prepreg.
To read this article, which appeared in the June 2015 issue of The PCB Design Magazine, click here.
More Columns from Beyond Design
Beyond Design: The Metamorphosis of the PCB RouterBeyond Design: Radiation and Interference Coupling
Beyond Design: Key SI Considerations for High-speed PCB Design
Beyond Design: Electro-optical Circuit Boards
Beyond Design: AI-driven Inverse Stackup Optimization
Beyond Design: High-speed Rules of Thumb
Beyond Design: Integrated Circuit to PCB Integration
Beyond Design: Does Current Deliver the Energy in a Circuit?