-
- News
- Books
Featured Books
- design007 Magazine
Latest Issues
Current IssueShowing Some Constraint
A strong design constraint strategy carefully balances a wide range of electrical and manufacturing trade-offs. This month, we explore the key requirements, common challenges, and best practices behind building an effective constraint strategy.
All About That Route
Most designers favor manual routing, but today's interactive autorouters may be changing designers' minds by allowing users more direct control. In this issue, our expert contributors discuss a variety of manual and autorouting strategies.
Creating the Ideal Data Package
Why is it so difficult to create the ideal data package? Many of these simple errors can be alleviated by paying attention to detail—and knowing what issues to look out for. So, this month, our experts weigh in on the best practices for creating the ideal design data package for your design.
- Articles
- Columns
- Links
- Media kit
||| MENU - design007 Magazine
Rigid-Flex PCB Right the First Time--Without Paper Dolls
July 8, 2015 | AltiumEstimated reading time: 2 minutes
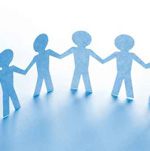
The biggest problem with designing rigid-flex hybrid PCBs is making sure everything will fold in the right way, while maintaining good flex-circuit stability and lifespan. The next big problem to solve is the conveyance of the design to a fabricator who will clearly understand the design intent and therefore produce exactly what the designer/engineer intended.
Rigid-flex circuit boards require additional cutting and lamination stages, and more exotic materials in manufacturing; therefore, the cost of re-spins and failures are substantially higher than traditional rigid boards. To reduce the risk and costs associated with rigid-flex design and prototyping, it is desirable to model the flexible parts of the circuit in 3D CAD to ensure correct form and fit. In addition, it is necessary to provide absolutely clear documentation for manufacturing to the fabrication and assembly houses.
The traditional attempt most design teams use to mitigate these risks is to create a “paper doll” of the PCB, by printing out a 1:1 representation of the board and then folding it up to fit a sample enclosure. This presents a number of issues:
- The paper doll does not also model the 3D thickness of the rigid and flex sections
- The paper doll does not include 3D models of the electronic components mounted on the PCB
- A physical sample of the final enclosure is needed, which may not yet be available
- If the mechanical enclosure is custom designed, a costly 3D print will be required for testing. This adds much time and expense to the project. As cool as 3D printers are, it's not a sensible use for them if the modeling can be done entirely in software.
This paper discusses practical steps in two approaches to solve these problems, contrasting against the traditional paper doll approach above.
In the first scenario, a 3D MCAD model of the PCB assembly can be created in the MCAD package where a sheet metal model can be generated for the PCB substrate model. This sheet metal model can be bent into shape in the MCAD software to fit the final enclosure and check for clearance violations. This is not the best approach, but it is better than paper dolls.
In the second scenario, a significant part of the enclosure or mechanical assembly model is brought from the MCAD package into the PCB design software, where the rigid-flex board outline can be designed specifically to fit with it. Rigid-flex layer stack sections can be defined and then flexible circuit areas have bending lines added. In the PCB design tool's 3D mode, the folds are then implemented to reveal where potential clearance violations and interference occurs. The PCB design can then be interactively modified to resolve the problems and check right away—without having to build any further mock-ups or translate design databases from one tool to another.
To read this entire article, which appeared in the June 2015 issue of The PCB Design Magazine, click here.
Suggested Items
Digital Twin Concept in Copper Electroplating Process Performance
07/11/2025 | Aga Franczak, Robrecht Belis, Elsyca N.V.PCB manufacturing involves transforming a design into a physical board while meeting specific requirements. Understanding these design specifications is crucial, as they directly impact the PCB's fabrication process, performance, and yield rate. One key design specification is copper thieving—the addition of “dummy” pads across the surface that are plated along with the features designed on the outer layers. The purpose of the process is to provide a uniform distribution of copper across the outer layers to make the plating current density and plating in the holes more uniform.
Meet the Author Podcast: Martyn Gaudion Unpacks the Secrets of High-Speed PCB Design
07/10/2025 | I-Connect007In this special Meet the Author episode of the On the Line with… podcast, Nolan Johnson sits down with Martyn Gaudion, signal integrity expert, managing director of Polar Instruments, and three-time author in I-Connect007’s popular The Printed Circuit Designer’s Guide to... series.
Showing Some Constraint: Design007 Magazine July 2025
07/10/2025 | I-Connect007 Editorial TeamA robust design constraint strategy balances dozens of electrical and manufacturing trade-offs. This month, we focus on design constraints—the requirements, challenges, and best practices for setting up the right constraint strategy.
The Shaughnessy Report: Showing Some Constraint
07/14/2025 | Andy Shaughnessy -- Column: The Shaughnessy ReportWhen we first decided to cover strategies for setting PCB design constraints, one designer we spoke with said, “They’re not really constraints; they’re more like guardrails that prevent your design from going off a cliff.”
Elementary, Mr. Watson: Rein in Your Design Constraints
07/10/2025 | John Watson -- Column: Elementary, Mr. WatsonI remember the long hours spent at the light table, carefully laying down black tape to shape each trace, cutting and aligning pads with surgical precision on sheets of Mylar. I often went home with nicks on my fingers from the X-Acto knives and bits of tape all over me. It was as much an art form as it was an engineering task—tactile and methodical, requiring the patience of a sculptor. A lot has changed in PCB design over the years.