-
- News
- Books
Featured Books
- design007 Magazine
Latest Issues
Current IssueShowing Some Constraint
A strong design constraint strategy carefully balances a wide range of electrical and manufacturing trade-offs. This month, we explore the key requirements, common challenges, and best practices behind building an effective constraint strategy.
All About That Route
Most designers favor manual routing, but today's interactive autorouters may be changing designers' minds by allowing users more direct control. In this issue, our expert contributors discuss a variety of manual and autorouting strategies.
Creating the Ideal Data Package
Why is it so difficult to create the ideal data package? Many of these simple errors can be alleviated by paying attention to detail—and knowing what issues to look out for. So, this month, our experts weigh in on the best practices for creating the ideal design data package for your design.
- Articles
- Columns
- Links
- Media kit
||| MENU - design007 Magazine
Estimated reading time: 2 minutes
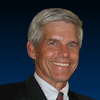
Designing a Manufacturable Flexible PCB Involves Tradeoffs
Designers are always inquiring about the limits of flexible PCBs. Maximum amperage, copper thickness, flex life, and minimum recommended pitch are just a few examples of the limits that designers are exploring when designing electronic packages. Design guides and websites provide information and tools related to many of these questions, and materials and properties pages provide information on the various materials and material thicknesses that are typically used. A trace width calculator can give you power, resistance and amperage calculations based on trace configuration. Design guides can also provide information and recommendations on a wide variety of flexible circuit options and characteristics.
In most cases, these information sources address the single criteria, but in reality, a flex designer is faced with multiple requirements that can make calculations and specifications much more complicated. For example, 5 oz. copper may adequately address an amperage requirement, but flexibility can be diminished. Five-ounce copper may not work for high flex applications, although it may work with limited flexing such as flex-to-install applications. Another limitation of thicker copper is the ability to resolve narrow conductors. Circuits with 0.005” width and spacings are commonly fabricated, but with much thinner copper. Five-ounce copper is 0.007” thick. This would require etching ratios (the rate of X-Y etch to Z etch) that present manufacturability issues. So the limits of line width and spacing are highly dependent on copper thicknesses.
Copper thickness and pitch are just two examples of the interdependencies that different characteristics or parameters impose on each other. As flexible circuit features and characteristics such as layer count, number of components, surface finishing and circuit size increase, the interdependencies of multiple criteria become far more complex. As with most things in life, in order to get something you probably have to give something. What is at stake is the manufacturability, and cost effectiveness, of the design. Failure to adequately account for these interdependencies can result in unacceptable manufacturing yields and/or designs that are not robust.
An electronic designer is usually faced with a set of trade-offs when deciding what type of interconnect medium to adopt. Rigid printed circuit boards, connectors, flex circuits, wire harnesses and hand assembly all compete for the attention of a system designer. Often the designer is forced to compromise among several design constraints driven by restrictions that alternative component specifications place on the package. Within flex circuitry design alternatives, the solution may involve going from single-sided to double-sided circuits, adding a shielding layer, folding an “origami” flex circuit, or blending two circuits into one.
Understanding these interdependencies requires a high level of experience and expertise—and sometimes a sequence of trial and error. Many times an iterative process is required even for some of the most experienced flexible circuit engineers. Getting a flexible circuit supplier involved early and often in the design process will eliminate some of the more obvious design issues. Choosing a supplier with a short product start-up cycle time can also be advantageous.
When choosing a flex circuit supplier, look for one with website tools and resources that provide design support with these complex issues. Utilize the engineering talent at the supplier by taking advantage of a design consultation. A robust design review process helps bring a new part number from concept to high volume manufacturing. Designing a flexible circuit doesn’t have to be complicated and challenging if support resources from the supplier are engaged early in the decision process.
Dave Becker is vice president of sales and marketing at All Flex Flexible Circuits LLC.
More Columns from All About Flex
All About Flex: Terms and ConditionsAll About Flex: ISO 9001 Basics
All About Flex: FAQs on UL Listings for Flexible Circuits
All About Flex: Avoiding Trace Fracturing in a Flexible Circuit
Polyimide vs. Silicone for Flexible Heaters
All About Flex: Copper Thickness Requirements for Flex Circuits
All About Flex: Copper Grain Direction
All About Flex: Options for Purchasing Flexible Heaters