-
-
News
News Highlights
- Books
Featured Books
- design007 Magazine
Latest Issues
Current IssueAll About That Route
Most designers favor manual routing, but today's interactive autorouters may be changing designers' minds by allowing users more direct control. In this issue, our expert contributors discuss a variety of manual and autorouting strategies.
Creating the Ideal Data Package
Why is it so difficult to create the ideal data package? Many of these simple errors can be alleviated by paying attention to detail—and knowing what issues to look out for. So, this month, our experts weigh in on the best practices for creating the ideal design data package for your design.
Designing Through the Noise
Our experts discuss the constantly evolving world of RF design, including the many tradeoffs, material considerations, and design tips and techniques that designers and design engineers need to know to succeed in this high-frequency realm.
- Articles
- Columns
- Links
- Media kit
||| MENU - design007 Magazine
Gary Ferrari Shares His Thoughts on PCB Design and More
August 5, 2015 | Barry Matties, I-Connect007Estimated reading time: 2 minutes
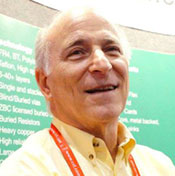
Recently, I had a chance to talk with Gary Ferrari, the director of technical support at Firan Technology Group Corporation (FTG), on numerous topics related to PCB design. Our conversation ranged from CID training to the need for reaching high school students as a way of introducing more young people to career opportunities in our industry. We also covered strategies for helping customers design and build better product, and keeping designers provided with the most critical part of their supply chain—information.
Barry Matties: Gary, please begin by telling us a little bit about FTG.
Gary Ferrari: FTG is a circuit board manufacturer—that's the circuits division. Then we have an aerospace division and their products are keyboards, bezels, and panels for the avionics industry. When you look at all the gauges on the dashboard of a cockpit, you are looking at the items we manufacture.
Matties: Is it more for military applications?
Ferrari: It’s for both commercial and military avionics. Our products are on helicopters and military aircraft. We're also on many of the commercial aircraft. We're on the new C919 from China. Actually, we have a plant to build those units over there. We have an aerospace and a circuits division in Toronto, as well as an aerospace and circuits division in Chatsworth, California.
Matties: What is your position at FTG?
Ferrari: I am the director of technical support—that means that I get into the customer prior to the design or during the design phase and I help them with their design issues. I look at manufacturability from a fabrication standpoint, as well as assembly, DFM, test, etc. I try to help them design a good product in the long run. That's where I serve best.
Matties: When you talk about working with customers, is that at the pre-circuit level when they are just imagining this stuff or is it beyond that?
Ferrari: They have already done the imagining, and now they need to bring it to the physical world. Sometimes they just don't understand the tolerances or the processes, the sequences in building a stack-up, material characteristics and combinations, buried vias and all those little details. I work with them so that they understand how to build something that's manufacturable and cost-effective. Anybody can design something, but when it comes down to getting fabricated, it could end up being a million-dollar design when it could have been maybe a thousand-dollar design, but they messed it all up. We try to help them out with that, and that's what my job is.
To read this entire article, which appeared in the July 2015 issue of The PCB Design Magazine, click here.
Suggested Items
I-Connect007 Editor’s Choice: Five Must-Reads for the Week
06/27/2025 | Nolan Johnson, I-Connect007While news outside our industry keeps our attention occupied, the big news inside the industry is the rechristening of IPC as the Global Electronics Association. My must-reads begins with Marcy LaRont’s exclusive and informative interview with Dr. John Mitchell, president and CEO of the Global Electronics Association. For designers, have we finally reached the point in time where autorouters will fulfill their potential?
Knocking Down the Bone Pile: Tin Whisker Mitigation in Aerospace Applications, Part 3
06/25/2025 | Nash Bell -- Column: Knocking Down the Bone PileTin whiskers are slender, hair-like metallic growths that can develop on the surface of tin-plated electronic components. Typically measuring a few micrometers in diameter and growing several millimeters in length, they form through an electrochemical process influenced by environmental factors such as temperature variations, mechanical or compressive stress, and the aging of solder alloys.
RTX, the Singapore Economic Development Board Sign MOU Outlining 10-year Growth Roadmap
06/20/2025 | RTXRTX and the Singapore Economic Development Board (EDB) have signed a Memorandum of Understanding (MoU) which outlines a 10-year roadmap to further long-term strategic collaboration in Singapore.
Indra Signs Agreement with AXISCADES to Boost Production of Cutting-Edge Systems in India
06/18/2025 | PRNewswireParis Air Show -- Indra and the Indian technology company AXISCADES have signed an agreement to collaborate on the production of solutions for the aerospace and defense markets.
GKN Aerospace Delivers First High Voltage EWIS System for Clean Aviation’s SWITCH Project
06/16/2025 | GKN AerospaceGKN Aerospace has completed and delivered the first high voltage Electrical Wiring Interconnection System (EWIS) for the Clean Aviation SWITCH project.