-
- News
- Books
Featured Books
- design007 Magazine
Latest Issues
Current IssueAll About That Route
Most designers favor manual routing, but today's interactive autorouters may be changing designers' minds by allowing users more direct control. In this issue, our expert contributors discuss a variety of manual and autorouting strategies.
Creating the Ideal Data Package
Why is it so difficult to create the ideal data package? Many of these simple errors can be alleviated by paying attention to detail—and knowing what issues to look out for. So, this month, our experts weigh in on the best practices for creating the ideal design data package for your design.
Designing Through the Noise
Our experts discuss the constantly evolving world of RF design, including the many tradeoffs, material considerations, and design tips and techniques that designers and design engineers need to know to succeed in this high-frequency realm.
- Articles
- Columns
- Links
- Media kit
||| MENU - design007 Magazine
The Challenges of Being Competitive in Automotive Electronics Manufacturing
October 14, 2015 | Michael Ford, Mentor Graphics Valor DivisionEstimated reading time: 2 minutes
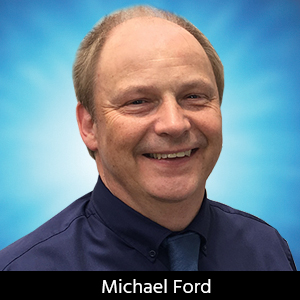
Tight money and severe liability requirements make competition tough for OEMs, as well as EMS providers and ODM counterparts in the market for automotive electronics. Manufacturers with the technological infrastructure to create low-cost, integrated traceability solutions and Lean process controls will most likely succeed in the forthcoming industrial climate, while those with heavy overhead burdens and sluggish enterprise resources are likely to retreat or fail.
In the highly competitive automotive industry, prices for electronic products across a vast range of applications have generally reduced to the point where meeting all the aspects of quality, reliability, and safety has become a serious challenge, far more so than in other sectors of critical electronics manufacturing such as aerospace, medical, and military, where price pressure has been far less significant. Automotive is unique in this respect, having to provide the most critical of products in the most cost-competitive way. Regardless of the price point of the vehicle, the purchaser always expects perfect quality supporting a “perfect” safety expectation. This is not a new situation per se, but dealing with this challenge in today’s evolving automotive environment in terms of increased adoption of technology, is now a critical factor for the success of automotive manufacturers and their suppliers.
The Evolving Significance of Automotive Electronics
Simple electronics were gradually introduced into automobiles from the earliest times. At first, these were just simple electro-mechanical devices to make cars work without manual effort, such as to start the engine and keep windshields clear. A little later, electronics evolved for convenience and entertainment, for example, radios and heaters. It is relatively recently that we see the introduction of more sophisticated systems for safety and performance, appearing relatively recently in the life of automotive as an industry. As an initially insignificant component in terms of manufacturing cost and therefore, electronics sub-assemblies have had to follow the same management requirements, directives and rules governing other parts of the automotive manufacturing process. But in this past decade, we have seen the effects of the gradual growth of issues with electronics systems, with recalls caused by safety issues that cost automotive manufacturers millions of dollars. Electronics within an automotive environment today requires a new approach to ensure a higher level of quality perfection.
Traditionally, traceability in the automobile industry was invented to identify, in the case of a market problem occurring, the precise scope of cars that were potentially affected by the issue, to reduce the exposure and cost if a recall had to be made, limiting the damage and erosion of brand confidence in the market. As more safety-critical applications with the potential of new problems are becoming ubiquitous in today’s vehicles, such as air-bags, breaking and stability systems, and more recently radar control, millions of cars and their drivers can be affected by issues related to electronics.
To read this entire article, which appeared in the September 2015 issue of The PCB Design Magazine, click here.
Suggested Items
I-Connect007’s Editor’s Choice: Five Must-Reads for the Week
07/04/2025 | Marcy LaRont, I-Connect007For our industry, we have seen several bullish market announcements over the past few weeks, including one this week by IDC on the massive growth in the global server market. We’re also closely watching global trade and nearshoring. One good example of successful nearshoring is Rehm Thermal Systems, which celebrates its 10th anniversary in Mexico and the official opening of its new building in Guadalajara.
Hon Hai Education Foundation Continues to Promote Quantum Education
07/04/2025 | FoxconnHon Hai Education Foundation has long been committed to promoting forward-looking technology education in Taiwan's high schools, and held the "High School Quantum Teacher Training Camp" in Tainan City on July 1.
Incap UK Achieves JOSCAR Zero Accreditation
07/04/2025 | IncapIncap Electronics UK has been accredited under JOSCAR Zero, a new sustainability-focused extension of the defence and aerospace sector’s supplier assurance system.
Kitron Secures Contract for Components Supporting Unmanned Aerial Systems
07/04/2025 | KitronKitron has received a contract with an estimated value between EUR 4 and 8 million for the production and supply of advanced electronic components used in unmanned aerial systems (UAS).
NOTE Receives Order Worth 132 MSEK and Expands Collaboration with Customer within Security & Defense
07/04/2025 | NOTENOTE has received an order worth SEK 132 million from one of its existing customers operating within Security & Defense. NOTE thereby strengthens its long-term collaboration with the industry-leading customer.