-
-
News
News Highlights
- Books
Featured Books
- design007 Magazine
Latest Issues
Current IssueAll About That Route
Most designers favor manual routing, but today's interactive autorouters may be changing designers' minds by allowing users more direct control. In this issue, our expert contributors discuss a variety of manual and autorouting strategies.
Creating the Ideal Data Package
Why is it so difficult to create the ideal data package? Many of these simple errors can be alleviated by paying attention to detail—and knowing what issues to look out for. So, this month, our experts weigh in on the best practices for creating the ideal design data package for your design.
Designing Through the Noise
Our experts discuss the constantly evolving world of RF design, including the many tradeoffs, material considerations, and design tips and techniques that designers and design engineers need to know to succeed in this high-frequency realm.
- Articles
- Columns
- Links
- Media kit
||| MENU - design007 Magazine
Accelerating the Design Cycle : Moving from Discipline-Centric to Product-Centric Design
October 28, 2015 | Bob Potock, ZukenEstimated reading time: 2 minutes
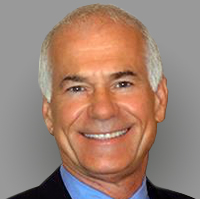
Defining the characteristics of a new product, such as features, size, weight, and battery life, is the job of marketing. Realizing those design requirements is the responsibility of a multidisciplinary team consisting of product architects, hardware engineers, software engineers, mechanical engineers, packaging engineering, manufacturing engineers, purchasers, etc.
Today, the design process in most cases fans out from the requirements as defined by marketing into multiple independent design threads that converge at the prototype. There is usually no systematic method for these different disciplines to communicate their work to the other disciplines. This lack of communication often leads to conflicting design decisions, such as when an electrical engineer or purchaser selects a component without having any way of knowing that it interferes with the enclosure. Extra design turns are often needed to resolve these conflicts at the prototype stage.
This obstacle, and many others, can be overcome by a product-centric design process that enables all disciplines to work collaboratively during a new virtual prototyping and detailed design. During the architectural validation or virtual prototyping phase, each contributor can optimize the design from their own perspective with visibility and change notices from the others. The product optimization completed during the virtual prototyping process seamlessly transitions to detailed design, preserving all the critical decisions without data loss or re-entry. Product-centric design ensures that the evolving design meets the requirements of every discipline, reducing late stage design changes and enabling the product to be optimized to a higher degree than is possible with current methods.
Limitations of the Discipline-Centric Process
Looking back just a few years, developers of electronic products primarily competed based on the functionality of their design as determined by unique hardware and software features. Today, with much of the key functionality of electronic products having been commoditized in system-on-chips (SoCs) or application processors, electronics companies are now competing across a wide range of fronts: size, weight, style, battery life and features. The result is a greater need than ever for collaboration across the multiple disciplines that are responsible for providing this much broader range of attributes. More than ever before, a multidiscipline collaborative effort is required to deliver the best design that conforms to marketing requirements in the shortest possible time and at the lowest possible cost.
Yet the tools used to support product development and the process itself have not yet evolved to this new reality. In most cases, the marketing department draws up the requirements documents that then explode into multiple independent paths. The creative team styles the product. The procurement team looks at part cost. PCB designers design the boards one at a time. The manufacturing team decides where to make the product and what processes to use. Mechanical engineers design the enclosure. There may be some limited informal collaboration between disciplines using a spreadsheet or flowcharting tool prior to detailed design, but for the most part, each of these disciplines works independently with relatively little interaction with the others. This is a critical time where architectural decisions are being made with very little validation. In addition, this is generally a sidebar process whose results are not easy to integrate back into the separate design disciplines or into the detailed design; any communications errors can be disastrous.
To read this entire article, which appeared in the October 2015 issue of The PCB Design Magazine, click here.
Suggested Items
DownStream Acquisition Fits Siemens’ ‘Left-Shift’ Model
06/26/2025 | Andy Shaughnessy, I-Connect007I recently spoke to DownStream Technologies founder Joe Clark about the company’s acquisition by Siemens. We were later joined by A.J. Incorvaia, Siemens’ senior VP of electronic board systems. Joe discussed how he, Rick Almeida, and Ken Tepper launched the company in the months after 9/11 and how the acquisition came about. A.J. provides some background on the acquisition and explains why the companies’ tools are complementary.
Elementary Mr. Watson: Retro Routers vs. Modern Boards—The Silent Struggle on Your Screen
06/26/2025 | John Watson -- Column: Elementary, Mr. WatsonThere's a story about a young woman preparing a holiday ham. Before putting it in the pan, she cuts off the ends. When asked why, she shrugs and says, "That's how my mom always did it." She asks her mother, who gives the same answer. Eventually, the question reaches Grandma, who laughs and says, "Oh, I only cut the ends off because my pan was too small." This story is a powerful analogy for how many PCB designers approach routing today.
Connect the Dots: The Future of PCB Design and Manufacturing
07/02/2025 | Matt Stevenson -- Column: Connect the DotsFor some time, I have been discussing the increasing complexity of PCBs and how designers can address the constantly evolving design requirements associated with them. My book, "The Printed Circuit Designer’s Guide to… Designing for Reality," details best practices for creating manufacturable boards in a modern production environment.
Siemens Turbocharges Semiconductor and PCB Design Portfolio with Generative and Agentic AI
06/24/2025 | SiemensAt the 2025 Design Automation Conference, Siemens Digital Industries Software today unveiled its AI-enhanced toolset for the EDA design flow.
Cadence AI Autorouter May Transform the Landscape
06/19/2025 | Andy Shaughnessy, Design007 MagazinePatrick Davis, product management director with Cadence Design Systems, discusses advancements in autorouting technology, including AI. He emphasizes a holistic approach that enhances placement and power distribution before routing. He points out that younger engineers seem more likely to embrace autorouting, while the veteran designers are still wary of giving up too much control. Will AI help autorouters finally gain industry-wide acceptance?