-
- News
- Books
Featured Books
- design007 Magazine
Latest Issues
Current IssueShowing Some Constraint
A strong design constraint strategy carefully balances a wide range of electrical and manufacturing trade-offs. This month, we explore the key requirements, common challenges, and best practices behind building an effective constraint strategy.
All About That Route
Most designers favor manual routing, but today's interactive autorouters may be changing designers' minds by allowing users more direct control. In this issue, our expert contributors discuss a variety of manual and autorouting strategies.
Creating the Ideal Data Package
Why is it so difficult to create the ideal data package? Many of these simple errors can be alleviated by paying attention to detail—and knowing what issues to look out for. So, this month, our experts weigh in on the best practices for creating the ideal design data package for your design.
- Articles
- Columns
- Links
- Media kit
||| MENU - design007 Magazine
Designers Notebook: Flex and Rigid-Flex Circuit Design Principles, Part 1
January 27, 2016 | Vern Solberg, ConsultantEstimated reading time: 5 minutes
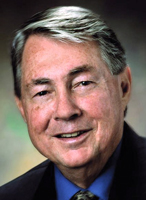
Flexible circuits represent an advanced approach to total electronics packaging, typically occupying a niche that replaces ordinary printed circuit board assemblies and the hard-wire interface needed to join assemblies. Flex circuits have an advantage over hard-wire interface because they fit only one way, eliminating wire routing errors as well as the time needed for testing and inspection.
Furthermore, flex circuit conductor patterns will maintain uniform electrical characteristics, controlling noise, crosstalk, and impedance. In addition to saving up to 75% on space and weight, flexible circuits improve overall product reliability. In essence, flex circuits furnish unlimited freedom of packaging geometry while retaining the precision, density, and repeatability of printed circuits.
Primary Flexible Circuit Structures
The four basic variations of flexible and rigid-flex circuits are defined as:
- Single-sided flex: The most common type of flexible circuit consists of a conductive layer bonded between two insulating layer materials with SMT lands (when needed) accessible on only one side. The single Cu layer flex is the ideal circuit for dynamic flexing applications.
- Double-sided flex circuit: Where copper foil is bonded on both sides of the base material. Vias connecting sides are punched, drilled or laser ablated and plated prior to chemically etching the circuit pattern. Finally, both sides of the circuit are covered with a dielectric cover-layer or cover-coat.
- Multilayer flex circuits: This type of circuit consists of a number of conductive layers bonded together with dielectric between them. Plated through-holes are used to create the interconnection of the conductive layers. Although referred to as a flex circuit, pliability is considerably lessened with the addition of each layer.
- Rigid-flex circuits: A rigid-flex structure consists of flexible circuit(s), which are then bonded onto or laminated within a rigid dielectric material. Flexible dielectrics provide unlimited conformability between rigid sections of the circuit commonly utilized for component mounting and system interface.
The design guidelines for flexible circuits, although similar to rigid circuits, have distinctive differences that are influenced by specific applications and the intended operating use environments.
Design for Operating Environment
Although the actual use environment may not subject the flex or rigid-flex circuits to excessive conditions, qualifying the end-product often requires thermal cycle testing (typically based on worst-case environments). Consumer and commercial products, for example, are not expected to be exposed to thermal conditions greater than 60°C; however, qualifying products for industrial, automotive and aeronautic applications will require reliable operation at both high and low temperature conditions (+95°C to -55°C).
Base Material Selection
Base material for flexible circuit applications includes both polyester and polyimide films. While polyester-based material may be considered for a number of cost-sensitive consumer applications, polyimide-based materials will continue to be specified for the more demanding environments noted above.
- Polyester films may not be the first choice for a number of applications but it does furnish excellent electrical properties, has relatively low moisture absorption potential and is thermally stable (capable of continuous operation at 105ºC). The material exhibits good to fair dimensional stability, is resistant to most chemicals and is the least expensive of the commonly used dielectric materials.
- Polyimide films have excellent electrical properties, the highest operating temperature capability (>200ºC) and good to excellent dimensional stability. Although the material furnishes excellent chemical resistance (acetone, methyl alcohol, toluene, and trichloroethylene) it has a relatively high moisture absorption rate and is significantly more expensive than polyester films.
Non-reinforced Dielectric
Polyimide remains the favorite alternative for flex and rigid-flex applications because the material is mechanically tough and easily withstands exposure to most harsh operating environments. The designer of the flexible circuit has a fairly wide range of material choices. The films, for example, are furnished in thicknesses that range between a very thin 12 microns (0.0005”) and 125 microns (.005”). For a majority of applications the 50-micron (0.002”) thick material will be specified; however, 25.0-micron (0.001”) thick films are often selected for complex forming conditions or, in dynamic applications, to maximize the circuits’ flexibility. Additionally, copper foil can be furnished on one side or both sides of the dielectric base. The copper foil is commonly laminated onto the surface of the polyimide film using a thin layer of modified acrylic, epoxy, epoxy prepreg, or phenolic butyral. Although copper foil can be furnished on both sides of the flexible base, furnishing copper on only one surface will be significantly less costly than the circuit requiring two-sided copper.
Copper foils are rolled and annealed and furnished in thicknesses of 17.0 microns (~0.0007") and 34.0 microns (~0.0014"). Foils as thin as 5.0 microns (~0.00018”) can also be furnished for semi-additive build-up plating when very high-density circuit routing is required. There are also polyimide films furnished with copper that is cast or deposited directly onto the films surface. These products are generally designated as adhesiveless. The adhesiveless circuits are more pliable and excellent for higher reliability applications, but the supply base is more limited and can be cost prohibitive for many consumer or commercial applications.
Reinforced Dielectric
Material selected for the rigid areas of the circuit is typically reinforced with a woven glass fiber. A key concern is how the material responds to multiple exposures to thermal extremes during the fabrication and assembly process. Material selected should exhibit minimal Z-axis expansion and furnish a higher thermal threshold before decomposition occurs. These factors will contribute to avoiding delamination during the product’s intended life cycle. All materials selected for the rigid-flex circuit will be certified to meet a flammability rating established by Underwriters Laboratory (UL).
Another factor that will influence material selection is the glass transition temperature (Tg), the temperature at which the material begins to relax. For example, the better grades of epoxy-glass laminates have a minimum Tg of 170ºC, while the polyimide-glass composites Tg minimum is extended to 200ºC. In regard to decomposition temperature (Td), epoxy-glass material specified in UL/ANSI FR4/126 and FR-4/129 specifies a minimum of 340ºC.
Note: Polyimide films and glass reinforced and non-reinforced organic base material specifications are detailed further in IPC-4101 and IPC-4102.
Before proceeding with the circuit layout, the designer must consider a number of requirements exclusive to the fabrication of flexible circuits. It’s important to discuss base material sets and alternative fabrication processes with your supplier prior to finalizing the design.
Vern Solberg is an independent technical consultant based in Saratoga, California specializing in SMT and microelectronics design and manufacturing technology. To reach Solberg, click here.
Suggested Items
I-Connect007 Editor’s Choice: Five Must-Reads for the Week
07/11/2025 | Andy Shaughnessy, Design007 MagazineThis week, we have quite a variety of news items and articles for you. News continues to stream out of Washington, D.C., with tariffs rearing their controversial head again. Because these tariffs are targeted at overseas copper manufacturers, this news has a direct effect on our industry.I-Connect007 Editor’s Choice: Five Must-Reads for the Week
Digital Twin Concept in Copper Electroplating Process Performance
07/11/2025 | Aga Franczak, Robrecht Belis, Elsyca N.V.PCB manufacturing involves transforming a design into a physical board while meeting specific requirements. Understanding these design specifications is crucial, as they directly impact the PCB's fabrication process, performance, and yield rate. One key design specification is copper thieving—the addition of “dummy” pads across the surface that are plated along with the features designed on the outer layers. The purpose of the process is to provide a uniform distribution of copper across the outer layers to make the plating current density and plating in the holes more uniform.
Trump Copper Tariffs Spark Concern
07/10/2025 | I-Connect007 Editorial TeamPresident Donald Trump stated on July 8 that he plans to impose a 50% tariff on copper imports, sparking concern in a global industry whose output is critical to electric vehicles, military hardware, semiconductors, and a wide range of consumer goods. According to Yahoo Finance, copper futures climbed over 2% following tariff confirmation.
Happy’s Tech Talk #40: Factors in PTH Reliability—Hole Voids
07/09/2025 | Happy Holden -- Column: Happy’s Tech TalkWhen we consider via reliability, the major contributing factors are typically processing deviations. These can be subtle and not always visible. One particularly insightful column was by Mike Carano, “Causes of Plating Voids, Pre-electroless Copper,” where he outlined some of the possible causes of hole defects for both plated through-hole (PTH) and blind vias.
Trouble in Your Tank: Can You Drill the Perfect Hole?
07/07/2025 | Michael Carano -- Column: Trouble in Your TankIn the movie “Friday Night Lights,” the head football coach (played by Billy Bob Thornton) addresses his high school football team on a hot day in August in West Texas. He asks his players one question: “Can you be perfect?” That is an interesting question, in football and the printed circuit board fabrication world, where being perfect is somewhat elusive. When it comes to mechanical drilling and via formation, can you drill the perfect hole time after time?