-
- News
- Books
Featured Books
- pcb007 Magazine
Latest Issues
Current IssueSales: From Pitch to PO
From the first cold call to finally receiving that first purchase order, the July PCB007 Magazine breaks down some critical parts of the sales stack. To up your sales game, read on!
The Hole Truth: Via Integrity in an HDI World
From the drilled hole to registration across multiple sequential lamination cycles, to the quality of your copper plating, via reliability in an HDI world is becoming an ever-greater challenge. This month we look at “The Hole Truth,” from creating the “perfect” via to how you can assure via quality and reliability, the first time, every time.
In Pursuit of Perfection: Defect Reduction
For bare PCB board fabrication, defect reduction is a critical aspect of a company's bottom line profitability. In this issue, we examine how imaging, etching, and plating processes can provide information and insight into reducing defects and increasing yields.
- Articles
- Columns
- Links
- Media kit
||| MENU - pcb007 Magazine
All About Flex: Lead-Free Soldering Flexible Circuits
September 22, 2016 | Dave Becker, All FlexEstimated reading time: 3 minutes
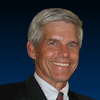
Ever since the European community adopted the RoHS directive in 2006, the U.S. electronics industry has been steadily increasing its use of lead-free solder. Medical was the first U.S. industry to go totally lead-free. Today, a significant percentage of electronics soldering is done with lead-free solder. After several years of refinement and withstanding some mischaracterizations, lead-free soldering is proving to be cost effective and reliable.
While lead-free solder is reliable, there are differences in materials and processing that need to be understood to ensure a robust electronics design.
Material Composition: The most widely used lead-free solder paste is a tin/silver/copper alloy (Sn/Ag/Cu). These are available in slightly different combinations; the following are the more common ones:
- Sn96.5/Ag3.0/Cu0.5
- Sn95.5/Ag3.8/Cu0.7
- Sn95.5/Ag4.0/Cu0.5
There are alloys other than tin/silver/copper that can be used for lead-free soldering; most of these are for non-electronic applications. The optimal choice of alloy depends on the type of surface to solder and the application for the flexible circuit.
Cosmetic Appearance: The classic tin-lead solder joints were shiny and smooth. In fact, a defective solder joint often had a dull, rough appearance. This is not the case for lead-free solder joints, which have a less shiny appearance. Those who are not familiar with lead-free solder will immediately flag the dull appearance as defective joints. The dull appearance in solder joints is not indicative of the quality of the solder joint, but simply due to the inherent properties of the alloy. See Figure 1 for a side-by-side comparison.
Figure 1: Lead-free vs. tin-lead. (Source: CEDOS Electronics)
Process Temperature: Lead-free solder starts to reflow around 218°C, whereas tin-lead solder will reflow around 188°C. The higher temperature can have an adverse impact on the fixtures, equipment and materials used on a flexible circuit. When introducing a new part number requiring lead-free solder, an engineering review should occur to insure all materials have proper temperature compatibility.
Mechanical Strength: Lead-free solder does not have the mechanical strength of the traditional tin-lead solder. This is one of the reasons that the lead-free is not used in military or aerospace applications. The RoHS directive exempts military and some aerospace products. While tin-lead solder has better mechanical properties, there are ways to address mechanical strength issues with lead-free solder. Adding epoxy or conformal coating to reinforce the bond areas are ways to add robustness to designs requiring a high level of mechanical strength.
Flux: As with tin-lead soldering, there are two basic types of fluxes used with lead-free soldering: water washable flux and no-clean flux. The water washable flux must be completely removed after soldering. Water wash generally works well if there is adequate room under the components to rinse away residue. If the component density and profile do not allow thorough rinsing, then no-clean flux should be used. No-clean flux leaves a visible residue, which some may find objectionable. There may be a temptation to require residue removal with a cleaning process. But experts advise against removing the residue of a no-clean flux. No-clean flux residue is designed to encapsulate any contaminants that could potentially cause electrical problems in the field. By cleaning the no-clean flux, there is risk some of the contaminants will remain and create potential reliability problems.
Testing: Reliability and electrical testing are the same for both lead-free and tin-lead soldering processes. There are a couple of tests to determine if a given component has lead. One is to apply a chemical that simply changes color if there is lead in the solder. One could also use an atomic absorption spectrophotometer that will provide the exact content of the metal. These tests are mainly applicable to ensure an incoming product is lead-free, or to prove that a product meets RoHS requirements. During circuit fabrication, in-process material control should insure solder paste is lead-free.
An electronic packaging designer who is unfamiliar with lead-free processes will need to be educated on the various design, material, process, component and inspection nuances that lead-free soldering presents. Many circuit suppliers are able to provide a significant amount of design support for applications requiring lead-free solder.
Dave Becker is vice president of sales and marketing at All Flex Flexible Circuits LLC.
Suggested Items
Silicon Mountain Contract Services Enhances SMT Capabilities with New HELLER Reflow Oven
07/17/2025 | Silicon Mountain Contract ServicesSilicon Mountain Contract Services, a leading provider of custom electronics manufacturing solutions, is proud to announce a significant upgrade to its SMT production capability with the addition of a HELLER 2043 MK5 10‑zone reflow oven to its Nampa facility.
Knocking Down the Bone Pile: Addressing End-of-life Component Solderability Issues, Part 4
07/16/2025 | Nash Bell -- Column: Knocking Down the Bone PileIn 1983, the Department of Defense identified that over 40% of military electronic system failures in the field were electrical, with approximately 50% attributed to poor solder connections. Investigations revealed that plated finishes, typically nickel or tin, were porous and non-intermetallic.
SHENMAO Strengthens Semiconductor Capabilities with Acquisition of PMTC
07/10/2025 | SHENMAOSHENMAO America, Inc. has announced the acquisition of Profound Material Technology Co., Ltd. (PMTC), a premier Taiwan-based manufacturer of high-performance solder balls for semiconductor packaging.
KYZEN to Highlight Understencil and PCB Cleaners at SMTA Querétaro Expo and Tech Forum
07/09/2025 | KYZEN'KYZEN, the global leader in innovative environmentally responsible cleaning chemistries, will exhibit at the SMTA Querétaro Expo & Tech Forum, scheduled to take place Thursday, July 24, at Centro de Congresos y Teatro Metropolitano de Querétaro.
Driving Innovation: Direct Imaging vs. Conventional Exposure
07/01/2025 | Simon Khesin -- Column: Driving InnovationMy first camera used Kodak film. I even experimented with developing photos in the bathroom, though I usually dropped the film off at a Kodak center and received the prints two weeks later, only to discover that some images were out of focus or poorly framed. Today, every smartphone contains a high-quality camera capable of producing stunning images instantly.