-
- News
- Books
Featured Books
- pcb007 Magazine
Latest Issues
Current IssueVoices of the Industry
We take the pulse of the PCB industry by sharing insights from leading fabricators and suppliers in this month's issue. We've gathered their thoughts on the new U.S. administration, spending, the war in Ukraine, and their most pressing needs. It’s an eye-opening and enlightening look behind the curtain.
The Essential Guide to Surface Finishes
We go back to basics this month with a recount of a little history, and look forward to addressing the many challenges that high density, high frequency, adhesion, SI, and corrosion concerns for harsh environments bring to the fore. We compare and contrast surface finishes by type and application, take a hard look at the many iterations of gold plating, and address palladium as a surface finish.
It's Show Time!
In this month’s issue of PCB007 Magazine we reimagine the possibilities featuring stories all about IPC APEX EXPO 2025—covering what to look forward to, and what you don’t want to miss.
- Articles
- Columns
Search Console
- Links
- Media kit
||| MENU - pcb007 Magazine
EIPC 50th Anniversary Conference Day 1: The Past, the Present and the Future, Pt. 2
July 4, 2018 | Pete Starkey, I-Connect007Estimated reading time: 7 minutes
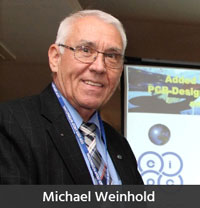
To read the first part of this article, click here.
Having already moderated Session 2, the moderator turned presenter as Emma Hudson, UL’s industry leader for PCBs in Europe, the Middle East, Africa and Latin America, continued her campaign to help the industry to understand the significance of solder limits and the need to keep them updated to meaningfully reflect the conditions of the assembly process.
She explained that Solder Limits were critical parameters employed in most of the test procedures used to characterise a PCB, a metal-clad base material or a solder resist, as part of the Recognition process, and represented the soldering processes the PCB would be exposed to during component-assembly operations. Any component-assembly time spent over 100°C or the maximum operating temperature, whichever was greater, was considered to be part of the Solder Limits, which could be single time and temperature or multiple times and temperatures. The only exceptions were PCBs which would only be subject to hand soldering.
The PCB industry was well aware that the more severe the soldering operation, the greater the degradation of the PCB and this included the properties evaluated for UL Recognition. Hudson emphasised that the traditional solder float test was not representative of SMT soldering operations. She made it clear that the standards were not changing, and that Solder Limits had always represented the soldering processes the circuit board was exposed to during the assembly operations. And manufacturers of PCBs, laminates and solder resists were free to choose their solder limits provided they were meaningful. Importantly, exceeding the Solder Limits would breach the Conditions of Acceptability and the PCB would be no longer Recognised for that application.
The fact was that the majority of UL Recognized PCBs, laminates and coatings had not had their solder limits updated for surface mount and/or multiple soldering operations and testing under more severe conditions would be required, the amount of testing depending on the materials being used and the existing parameters and process conditions. If laminate and coating manufacturers established appropriate solder limits, this would reduce the amount of testing to be carried out by the PCB fabricator.
Hudson urged the industry to work together to determine what would be the most meaningful solder limits to have Recognized. UL planned to formally communicate to companies that currently had UL Recognition or UL Listing. UL field engineers would then be responsible for verifying the soldering conditions to which the PCBs were exposed during all assembly operations and comparing these to the solder limits Recognized for the PCB. If the Recognized solder limits were exceeded, a Variation Notice would be raised. There would be a two-year transition period for the industry to complete the updating of their solder limits, after which a Variation Notice would result in charges being incurred.
Session 4 focused on new PCB material and processes for advanced applications, and was moderated by Martyn Gaudion, managing director of Polar Instruments and EIPC board member.
“Why going to halogen-free laminates?” Was the question posed by Shannon Juan, product promotion and marketing manager for Elite Material Co. in Taiwan. She explained that the development of halogen-free laminates had been driven initially by increasing environmental awareness and international environmental protection regulations. The adoption of halogen-free by leading manufacturers of mobile phones and computers may have been motivated primarily by commercial rather than technical considerations but had served to give halogen-free a firm foot-hold in the laminate market.
So how did halogen-free laminate differ from its halogenated counterparts? How was flame retardancy achieved without brominated resin? Juan examined the chemistry of combustion and explained that the essential components were combustible matter, a heat source and a combustion-supporting gas. Combustion in oxygen was a chain reaction involving many distinct radical intermediates. The combustion reaction could be disrupted by inhibiting the chain reaction, or by producing an incombustible gas or water to reduce the temperature, or by producing a char to separate the combustion-supporting gas from the combustible matter. Halogenated material acted by blocking the chain reaction, whereas halogen-free tended to rely on the production of a thick char and/or a filler that produced water vapour.
She showed some test results demonstrating superior physical properties of halogen-free resulting from stronger molecular bonds, and claimed that in general, halogen-free materials had better thermal reliability than their halogenated counterparts. And in conclusion she suggested that, in addition to its better reliability, as environmental awareness attracted more attention, halogen free material would become a trend for the future.
Alexander Ippich, technical director signal integrity and advanced technology in the OEM marketing group at Isola, discussed how laminate and process technology could be optimised to minimize the RF impact of frequencies in the 55 GHz to 95 GHz region.
In RF and microwave applications, most critical signals were routed as surface microstrip transmission lines without solder mask coverage to minimize insertion losses. However, the absence of solder mask resulted in these critical traces being coated with the solderable final finish, typically ENIG.
In the interests of keeping insertion losses to a minimum, very-low-loss and ultra-low-loss laminates, with dissipation factors as low as 0.0017 and very smooth copper foils were used in these high-frequency applications. But the impact of final metallisation was often not taken into consideration, and in the case of ENIG, the lower conductivity of the nickel could cause excessive losses as a consequence of the skin effect concentrating the current in the conductor surface.
Page 1 of 2
Suggested Items
ViTrox Marks 25 Years of Innovation with Cutting-Edge Solutions at NEPCON China 2025 in Shanghai
04/18/2025 | ViTrox TechnologiesViTrox, which aims to be the World’s Most Trusted Technology Company, is proud to announce its participation in NEPCON China 2025, taking place from April 22–24, 2025, at Booth #1E45, Shanghai World Expo Exhibition & Convention Centre (SWEECC).
Indium Experts to Present on Power Electronics at PCIM Europe 2025
04/17/2025 | Indium CorporationAs one of the leading materials providers to the power electronics assembly and e-Mobility industries, Indium Corporation experts will share their technical insight and knowledge on a variety of industry-related topics throughout PCIM Europe, May 6-8, in Nuremberg, Germany.
KOKI Announces Upcoming Webinar on Solder Voiding – Causes and Remedies
04/16/2025 | KOKIKOKI, a global leader in advanced soldering materials and process optimization services, is pleased to announce its upcoming webinar, “Solder Voiding—Causes and Remedies,” which will take place on Tuesday, April 22, 2025, at 12:00 PM CDT. Jerome McIntyre, Regional Sales & Applications Engineer at KOKI Americas, will present this live session.
Real Time with... IPC APEX EXPO 2025: Transition Automation Focusing on Security Coatings and Squeegee Technology
04/16/2025 | Real Time with...IPC APEX EXPOMark Curtin, President of Transition Automation, gives an update on recent innovations at his company. He highlights a record sales month and their new focus on security coatings to fight counterfeiting. Mark explains the engineering behind their durable squeegees, the importance of maintenance, and the value of considering overall costs over just price.
Indium to Feature Materials Solutions Powering Sustainability at PCIM Europe
04/15/2025 | Indium CorporationIndium Corporation specializes in power device packaging, offering a portfolio of advanced material solutions encompassing the entire assembly, including die-attach, top-side die interconnect, substrate-attach, package-attach, and PCB assembly.