Successful Flex Circuit Design and Processing Guidelines
December 18, 2018 | Tuan Tran, GREEN CIRCUITSEstimated reading time: 1 minute
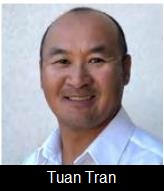
With the use of sensors and technology in everything from mobile phones to refrigerators, automobiles, and wearable medical devices, circuit boards are a component in many different types of products. In today’s world of electronics, any product with an on-off switch contains a circuit board.
Due to their versatility, the use of flex circuits is one of the fastest growing product market segments. With the introduction of flex and rigid-flex circuits, engineers have been given the opportunity to be more creative in designing new and innovative products. Flex and rigid-flex boards are built to fit into tight, threedimensional spaces while ensuring resistance to mechanical wear and vibration. Engineers can design products that require boards to fit into tight spaces, twist and turn for packaging, and make the product live in a more dynamic environment. These flexible circuits have the same performance levels as traditional rigid FR-4 boards; however, they have their own nuances and considerations when it comes to design, fabrication, and assembly.
Design and Layout
When designing a flex circuit, it is important to know the specific application for the circuit. Will it be used in a static or dynamic environment? If the board will reside in a static environment with little to no movement, the circuit design needs to have the appropriate amount of flexibility so that it can be easily installed within the product. Alternatively, if the board will exist in a dynamic environment where the board will continuously flex back and forth, a level of flexibility that can withstand continuous movement needs to be considered in the design.
Will the application require a flex or a rigidflex circuit? If the product requires one-sided surface-mount technology, then a fully flexible board may be the best option. If the product requires two-sided SMT, then a rigid-flex board is needed.
To read the full version of this article which originally appeared in the October 2018 issue of Flex007 Magazine, click here.
Suggested Items
Microchip Enters into Partnership Agreement with Delta Electronics on Silicon Carbide Solutions
07/18/2025 | Globe NewswireThe growth of artificial intelligence (AI) and the electrification of everything are driving an ever-increasing demand for higher levels of power efficiency and reliability.
ESD Alliance Reports Electronic System Design Industry Posts $5.1 Billion in Revenue in Q1 2025
07/16/2025 | SEMIElectronic System Design (ESD) industry revenue increased 12.8% to $5,098.3 million in the first quarter of 2025 from the $4,521.6 million registered in the first quarter of 2024, the ESD Alliance, a SEMI Technology Community, announced in its latest Electronic Design Market Data (EDMD) report.
Beyond Design: Refining Design Constraints
07/17/2025 | Barry Olney -- Column: Beyond DesignBefore starting any project, it is crucial to develop a thorough plan that encompasses all essential requirements. This ensures that the final product not only aligns with the design concept but is also manufacturable, reliable, and meets performance expectations. High-speed PCB design requires us to not only push technological boundaries but also consider various factors related to higher frequencies, faster transition times, and increased bandwidths during the design process.
Prague PEDC: Call for Abstracts Deadline July 31
07/16/2025 | Pan-European Electronics Design Conference (PEDC)The second Pan-European Electronics Design Conference (PEDC) will take place Jan. 21-22, 2026, in Prague, Czech Republic. The call for abstracts deadline is July 31. Organized jointly by the German Electronics Design and Manufacturing Association (FED) and the Global Electronics Association PEDC serves as a European platform for knowledge exchange, networking, and innovation in electronics design and development.
The Pulse: Design Constraints for the Next Generation
07/17/2025 | Martyn Gaudion -- Column: The PulseIn Europe, where engineering careers were once seen as unpopular and lacking street credibility, we have been witnessing a turnaround in the past few years. The industry is now welcoming a new cohort of designers and engineers as people are showing a newfound interest in the profession.