-
-
News
News Highlights
- Books
Featured Books
- pcb007 Magazine
Latest Issues
Current IssueThe Hole Truth: Via Integrity in an HDI World
From the drilled hole to registration across multiple sequential lamination cycles, to the quality of your copper plating, via reliability in an HDI world is becoming an ever-greater challenge. This month we look at “The Hole Truth,” from creating the “perfect” via to how you can assure via quality and reliability, the first time, every time.
In Pursuit of Perfection: Defect Reduction
For bare PCB board fabrication, defect reduction is a critical aspect of a company's bottom line profitability. In this issue, we examine how imaging, etching, and plating processes can provide information and insight into reducing defects and increasing yields.
Voices of the Industry
We take the pulse of the PCB industry by sharing insights from leading fabricators and suppliers in this month's issue. We've gathered their thoughts on the new U.S. administration, spending, the war in Ukraine, and their most pressing needs. It’s an eye-opening and enlightening look behind the curtain.
- Articles
- Columns
- Links
- Media kit
||| MENU - pcb007 Magazine
Insulectro’s OEM Program: Time to ACT!
June 21, 2019 | Nolan Johnson, I-Connect007Estimated reading time: 4 minutes
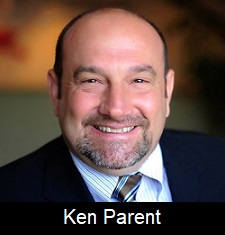
Ken Parent, Insulectro VP of sales and product management, discusses the current dynamics in the materials marketplace and how Insulectro is developing educational resources to help design teams and fabricators better understand the capabilities and features for the emerging laminate materials.
Nolan Johnson: Ken, let's start with a quick introduction of you and Insulectro.
Ken Parent: Insulectro is an electronic materials distribution company. We have been doing business in the PCB world for 50+ years. We provide materials that our fabricator customers use to build PCBs. In the last decade, Insulectro has also expanded into the printed electronics world, which brings some interesting perspectives to electronic material requirements. And we are focusing on how materials get specified in design as we continue to work through our OEM ACT! program—Accomplish Change Together!—which educates OEMs and designers by partnering with our fabricator customers.
Johnson: What are the dynamics in the market right now, and how do you see it changing?
Parent: Material selection right now is very dynamic especially with the two major laminate suppliers we represent. On the rigid laminate side, Isola has brought out at least seven new materials in the last 10 years, including products like Tachyon® 100G, I-Tera® MT40, ISpeed®, Astra MT77, and materials that they’ve just started to release as well. Many new materials are coming to the market, and they all have a very special performance attribute that is needed in the market.
On the flex side, we're also seeing new materials addressing high temperatures, for example. And there’s a renewed interest in materials that have been around for decades but now seem to be hitting their stride, such as DuPont’s Interra™ HK 04 buried capacitance material. There are great opportunities for new materials, but it also creates a lot of work and demand for educating the designers and fabricator customers on how to best use them. A lot of work is being done on laminates as well with copper foil enabling higher performance materials for electronic products and using smoother copper for better signal integrity performance.
Johnson: And the trade-offs in soldering and adhesion that go along with that.
Parent: Everything has its trade-offs, but in our case, Oak-Mitsui is working with the laminators, and they have some very good proprietary processes to make sure that those tradeoffs are meeting the expectations of IPC and OEMs. But even with help from IPC and UL, it's a lot to keep up with, but we have resources to help; that’s one of the key things that distinguishes Insulectro from the pack. For those looking for materials choices, we can match up Isola laminates together with DuPont Pyralux® laminates along with copper foils to create the best solution to a particular demand in the marketplace. We're very fortunate to get the ear of designers and people that are challenged for the next level of performance in their material choices.
Johnson: It seems to be time for designers to start thinking about the substrate as an active, performing part of the design. And you really need to think about the board as if it is an active component in your overall assembly.
Parent: Yes, that's true in a lot of ways. There’s electrical and thermal performance to consider as well as other requirements like flexibility, fitting into a particular box, or building a 32-layer board with minimal thickness. There are all sorts of mechanical, electrical, and thermal criteria required by these boards today. Evolving technology in electronics is stretching the limits of some of process capabilities. I am amazed at what PCB shops are able to do today, including the small holes they’re drilling, the number of layers they're doing, how well they're registering them, and the fact that now 3-mil lines and spaces are a daily occurrence in many shops. OEMs are requiring sub-50-micron lines and spaces on certain high-density jobs. All of those examples are challenging our fabricator customers, and therefore, our materials.
Johnson: With all of this new work going on in materials, there's a spectrum of materials appropriate for a particular design. Historically, it was standard FR-4m and you would go to some sort of high-end material; those were your two choices. But now, there is a range of products in the middle, and the ultimate specifier for materials is the design. How do we educate designers to make better decisions so that they're not under-specifying nor overspecifying their substrate?
Parent: That's a great question. It's an ongoing challenge, and we’re looking for ways to become a better solution provider on that front as well. We’re a little premature to talk about it today, but we are about to announce that Insulectro is going to be getting a lot closer to the PCBs design houses by providing design services to our fabricator customers that don’t currently have that as an offering. We've recently promoted one of our top Field Application Engineers, Megan Teta, to be product manager for these new design services.
There are a few circuit board shops that have a relationship with design houses today, and they do get involved with early design choices, including material selection, layer count, lines and spaces, hole sizes, etc. We have hired another resource who will be starting in May to drive our design services program to a significantly higher level within our business. We are anticipating having a relationship with as many as 100+ designers in the next 3–5 years do a better design of circuit boards. It’s a very young program that we've been talking about and investing time in over the last few months, and we’re about to take one giant step forward on that front soon.
To read the full article, which appeared in the May 2019 issue of PCB007 Magazine, click here.
Suggested Items
The Evolution of Picosecond Laser Drilling
06/19/2025 | Marcy LaRont, PCB007 MagazineIs it hard to imagine a single laser pulse reduced not only from nanoseconds to picoseconds in its pulse duration, but even to femtoseconds? Well, buckle up because it seems we are there. In this interview, Dr. Stefan Rung, technical director of laser machines at Schmoll Maschinen GmbH, traces the technology trajectory of the laser drill from the CO2 laser to cutting-edge picosecond and hybrid laser drilling systems, highlighting the benefits and limitations of each method, and demonstrating how laser innovations are shaping the future of PCB fabrication.
Day 2: More Cutting-edge Insights at the EIPC Summer Conference
06/18/2025 | Pete Starkey, I-Connect007The European Institute for the PCB Community (EIPC) summer conference took place this year in Edinburgh, Scotland, June 3-4. This is the third of three articles on the conference. The other two cover Day 1’s sessions and the opening keynote speech. Below is a recap of the second day’s sessions.
Day 1: Cutting Edge Insights at the EIPC Summer Conference
06/17/2025 | Pete Starkey, I-Connect007The European Institute for the PCB Community (EIPC) Summer Conference took place this year in Edinburgh, Scotland, June 3-4. This is the second of three articles on the conference. The other two cover the keynote speeches and Day 2 of the technical conference. Below is a recap of the first day’s sessions.
Preventing Surface Prep Defects and Ensuring Reliability
06/10/2025 | Marcy LaRont, PCB007 MagazineIn printed circuit board (PCB) fabrication, surface preparation is a critical process that ensures strong adhesion, reliable plating, and long-term product performance. Without proper surface treatment, manufacturers may encounter defects such as delamination, poor solder mask adhesion, and plating failures. This article examines key surface preparation techniques, common defects resulting from improper processes, and real-world case studies that illustrate best practices.
RF PCB Design Tips and Tricks
05/08/2025 | Cherie Litson, EPTAC MIT CID/CID+There are many great books, videos, and information online about designing PCBs for RF circuits. A few of my favorite RF sources are Hans Rosenberg, Stephen Chavez, and Rick Hartley, but there are many more. These PCB design engineers have a very good perspective on what it takes to take an RF design from schematic concept to PCB layout.