-
-
News
News Highlights
- Books
Featured Books
- pcb007 Magazine
Latest Issues
Current IssueThe Hole Truth: Via Integrity in an HDI World
From the drilled hole to registration across multiple sequential lamination cycles, to the quality of your copper plating, via reliability in an HDI world is becoming an ever-greater challenge. This month we look at “The Hole Truth,” from creating the “perfect” via to how you can assure via quality and reliability, the first time, every time.
In Pursuit of Perfection: Defect Reduction
For bare PCB board fabrication, defect reduction is a critical aspect of a company's bottom line profitability. In this issue, we examine how imaging, etching, and plating processes can provide information and insight into reducing defects and increasing yields.
Voices of the Industry
We take the pulse of the PCB industry by sharing insights from leading fabricators and suppliers in this month's issue. We've gathered their thoughts on the new U.S. administration, spending, the war in Ukraine, and their most pressing needs. It’s an eye-opening and enlightening look behind the curtain.
- Articles
- Columns
- Links
- Media kit
||| MENU - pcb007 Magazine
Estimated reading time: 2 minutes
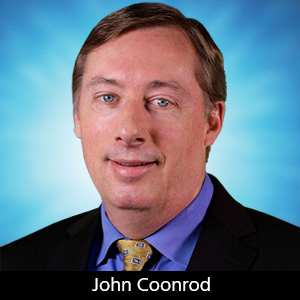
Lightning Speed Laminates: Practical Evaluations of Glass Weave Effect
The impact of glass weave effect on PCB electrical performance is a topic that has been investigated for many years. From my perspective, the initial investigators for the glass weave effect were mostly from the high-speed digital industry. However, as more RF applications are using millimeter-wave (mmWave) frequencies, the RF industry is now pursuing more studies for the potential of glass weave to impact these applications.
The basic issue for the glass weave effect is that many laminates have a layer, or layers, of woven fiberglass used to improve mechanical properties. The raw glass used to make the woven glass reinforcement layers is typically an E-glass, which has an approximate dielectric constant (Dk) of 6. As an example, for many laminates that have an overall Dk of 3.5, the resin system must have a much lower Dk than the glass, so the overall Dk of the laminate will be roughly 3.5.
For glass-reinforced laminates, and when looking down through the laminate, in isolated areas, the Dk of the laminate will be different in an area where there are glass bundles from the woven glass layer compared to areas where there are openings in the woven glass layer. In the open areas of the glass weave pattern, the Dk will be that of the resin system, and will probably have a Dk value around 2.1 to 3.0, depending on the laminate construction. In an area of the laminate where there is a combination of resin and one layer of glass bundles, the Dk will be somewhere between 2.1 and 6. In another area where the glass bundles intersect to form the grid of glass reinforcement, there will be two layers of glass as a knuckle and also the resin system. In these knuckle areas, the Dk will be the highest for the laminate. This means that within a small area of the laminate, there can be three areas of distinctly different Dk values.
When a circuit pattern is adjacently aligned to the glass weave pattern within a laminate, there will be areas of very different Dk values. However, at low frequency or low-speed digital, these Dk differences blend together and give an average Dk value. This is typically not a problem for PCB electrical performance. However, at much higher frequencies, like mmWave and high-speed digital, the wave and the digital pulse can detect these Dk differences, which can alter the expected electrical performance of the circuit.
There are a few things to consider about glass weave effect. One point of interest is when a laminate is using more than one layer of glass, the glass weave effect is somewhat dampened due to an averaging effect of the glass weave layers with their random alignment to each other. Another point of interest would be when a conductor is much larger than the geometry of the glass bundles, knuckles, and open area. Then, the conductor will experience an averaging of these different Dk values from the glass weave effect. This is typically not a problem for electrical performance.
To read this entire column, which appeared in the June 2019 issue of Design007 Magazine, click here.
More Columns from Lightning Speed Laminates
Lightning Speed Laminates: Millimeter-wave Properties and PCB Design ChallengesLightning Speed Laminates: Optimizing Thermal Management for Wireless Communication Systems
Lightning Speed Laminates: Test Vehicles for PCB Electrical Material Characterization
Lightning Speed Laminates: Optimum Thermal Stability Considerations
Lightning Speed Laminates: Thermal Management Isn’t Getting Easier
Lightning Speed Laminates: Benefits of High-Performance Hybrid Multilayer PCBs
Lightning Speed Laminates: An Overview of Copper Foils
Lightning Speed Laminates: The Importance of Circuit Features for Millimeter-Wave Applications