New High-Definition Satellite Radar Can Detect Bridges at Risk of Collapse From Space
July 10, 2019 | Bath UniversityEstimated reading time: 3 minutes
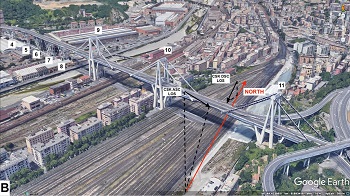
Combining data from a new generation of satellites with a sophisticated algorithm, a new monitoring system developed by researchers at the University of Bath with NASA could be used by governments or developers to act as a warning system ensuring large-scale infrastructure projects are safe.
The team of experts led by NASA’s JPL and engineers from Bath verified the technique by reviewing 15 years of satellite imagery of the Morandi Bridge in Genoa, Italy, a section of which collapsed in August 2018, killing 43 people. The review, published in the journal Remote Sensing, showed that the bridge did show signs of warping in the months before the tragedy.
Dr Giorgia Giardina, Lecturer in the University’s Department of Architecture and Civil Engineering, said: “The state of the bridge has been reported on before, but using the satellite information we can see for the first time the deformation that preceded the collapse.
“We have proved that it is possible to use this tool, specifically the combination of different data from satellites, with a mathematical model, to detect the early signs of collapse or deformation.”
While current structural monitoring techniques can detect signs of movement in a bridge or building, they focus only on specific points where sensors are placed. The new technique can be used for near-real time monitoring of an entire structure.
Jet Propulsion Laboratory Lead author Dr Pietro Milillo said: "The technique marks an improvement over traditional methods because it allows scientists to gauge changes in ground deformation across a single infrastructure with unprecedented frequency and accuracy.
"This is about developing a new technique that can assist in the characterisation of the health of bridges and other infrastructure. We couldn't have forecasted this particular collapse because standard assessment techniques available at the time couldn't detect what we can see now. But going forward, this technique, combined with techniques already in use, has the potential to do a lot of good."
This is made possible by advances in satellite technology, specifically on the combined use of the Italian Space Agency’s (ASI) COSMO-SkyMed constellation and the European Space Agency's (ESA's) Sentinel-1a and 1b satellites, which allows for more accurate data to be gathered. Precise Synthetic Aperture Radar (SAR) data, when gathered from multiple satellites pointed at different angles, can be used to build a 3D picture of a building, bridge or city street.
Dr Giardina added: “Previously the satellites we tried to use for this research could create radar imagery accurate to within about a centimetre. Now we can use data that is accurate to within a millimetre – and possibly even better, if the conditions are right. The difference is like switching to an Ultra-HD TV – we now have the level of detail needed to monitor structures effectively.
“There is clearly the potential for this to be applied continuously on large structures. The tools for this are cheap compared to traditional monitoring and can be more extensive. Normally you need to install sensors at specific points within a building, but this method can monitor many points at one time.”
The technique can also be used to monitor movement of structures when underground excavations, such as tunnel boring, are taking place.
“We monitored the displacement of buildings in London above the Crossrail route,” said Dr Giardina. “During underground projects there is often a lot of data captured at the ground level, while fewer measurements of structures are available. Our technique could provide an extra layer of information and confirm whether everything is going to plan.”
Dr Giardina has already been approached by infrastructure organisations in the UK with a view to setting up monitoring of roads and rail networks.
Suggested Items
Specially Developed for Laser Plastic Welding from LPKF
06/25/2025 | LPKFLPKF introduces TherMoPro, a thermographic analysis system specifically developed for laser plastic welding that transforms thermal data into concrete actionable insights. Through automated capture, evaluation, and interpretation of surface temperature patterns immediately after welding, the system provides unprecedented process transparency that correlates with product joining quality and long-term product stability.
Smart Automation: The Power of Data Integration in Electronics Manufacturing
06/24/2025 | Josh Casper -- Column: Smart AutomationAs EMS companies adopt automation, machine data collection and integration are among the biggest challenges. It’s now commonplace for equipment to collect and output vast amounts of data, sometimes more than a manufacturer knows what to do with. While many OEM equipment vendors offer full-line solutions, most EMS companies still take a vendor-agnostic approach, selecting the equipment companies that best serve their needs rather than a single-vendor solution.
Keysight, NTT, and NTT Innovative Devices Achieve 280 Gbps World Record Data Rate with Sub-Terahertz for 6G
06/17/2025 | Keysight TechnologiesKeysight Technologies, Inc. in collaboration with NTT Corporation and NTT Innovative Devices Corporation (NTT Innovative Devices), today announced a groundbreaking world record in data rate achieved using sub-THz frequencies.
Priority Software Announces the New, Game-Changing aiERP
06/12/2025 | Priority SoftwarePriority Software Ltd., a leading global provider of ERP and business management software announces its revolutionary aiERP, leveraging the power of AI to transform business operations.
Breaking Silos with Intelligence: Connectivity of Component-level Data Across the SMT Line
06/09/2025 | Dr. Eyal Weiss, CybordAs the complexity and demands of electronics manufacturing continue to rise, the smart factory is no longer a distant vision; it has become a necessity. While machine connectivity and line-level data integration have gained traction in recent years, one of the most overlooked opportunities lies in the component itself. Specifically, in the data captured just milliseconds before a component is placed onto the PCB, which often goes unexamined and is permanently lost once reflow begins.