-
-
News
News Highlights
- Books
Featured Books
- pcb007 Magazine
Latest Issues
Current IssueThe Hole Truth: Via Integrity in an HDI World
From the drilled hole to registration across multiple sequential lamination cycles, to the quality of your copper plating, via reliability in an HDI world is becoming an ever-greater challenge. This month we look at “The Hole Truth,” from creating the “perfect” via to how you can assure via quality and reliability, the first time, every time.
In Pursuit of Perfection: Defect Reduction
For bare PCB board fabrication, defect reduction is a critical aspect of a company's bottom line profitability. In this issue, we examine how imaging, etching, and plating processes can provide information and insight into reducing defects and increasing yields.
Voices of the Industry
We take the pulse of the PCB industry by sharing insights from leading fabricators and suppliers in this month's issue. We've gathered their thoughts on the new U.S. administration, spending, the war in Ukraine, and their most pressing needs. It’s an eye-opening and enlightening look behind the curtain.
- Articles
- Columns
- Links
- Media kit
||| MENU - pcb007 Magazine
Communication, Part 1: How to Qualify a Board Shop
October 4, 2019 | Steve Williams, The Right Approach Consulting LLCEstimated reading time: 2 minutes
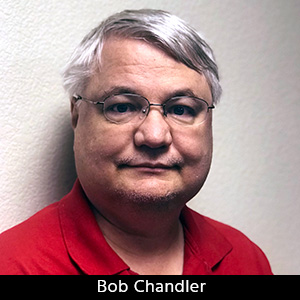
In Part 1 of this six-part series for "Fab Fridays," Mark Thompson, CID+, engineering support at Prototron, and CA Design CTO Bob Chandler discuss ways that PCB fabricators and designers can better communicate, starting with how to qualify a board shop.
Steve Williams: Welcome, Mark and Bob. To start this series, we’ll address how to qualify a board shop, aside from just getting a quote from somebody and giving them the green light. Let’s start with you, Bob. When you look at board shops, how do you suggest qualifying one?
Bob Chandler: Yes, that tends to be an issue that depends a great deal on what your industry is and what your requirements are. If you’re doing a small prototype series of boards, the qualifications of the fabrication house become much less important. If you’re dealing with aerospace or medical, the qualifications become a great deal and bigger if you’re dealing in production or prototype volumes; the qualification processes are considerably different. You really need to know what you need your fabrication house for before you start qualifying.
Williams: Good points. Mark, you do a lot of tours for customers and are involved with audits, etc. You’ve seen every different type of qualification. What are your thoughts on this topic?
Mark Thompson: I would send someone to the facility to qualify the shop. Secondly, ensure that the fabricator understands the engineer’s needs and reads and comprehends the drawing notes. Make sure that they won’t play any games with your boards, such as adding a second coat of mask to reduce impedances that may have overetched inadvertently and, therefore, run too high for impedance or even under. Understand the nature of RF features so that they won’t clip back a CPWG lead that’s intended to go right to the board edge for cosmetics and those kinds of things. It’s very important that the fabricator understands the needs of the engineer.
Williams: Right, and not just from a quality systems standpoint but also a technological standpoint.
Thompson: Exactly.
Williams: Excellent. What do you think of that, Bob? Is that something you’re on board with?
Chandler: Yes, those are definitely issues that we have had with the fabrication house in the past. If you design a board to make it exactly the way you want it, and the board house modifies the data—such as pulling circuits back from the edge, adding extra solder mask or to copper in the high-voltage area, or doing other things that change the characteristics of it—most of the time, they’ll come back and let us know that they’re doing that sort of thing. If they don’t, we discover it on the board later after the board has failed testing.
Stay tuned for Parts 2–6 of this series.
Steve Williams is the president of The Right Approach Consulting and an I-Connect007 columnist.
Bob Chandler is CTO of CA Design (cadesign.net) and a senior Allegro/OrCAD trainer and consultant.
Mark Thompson, CID+, is in engineering support at Prototron Circuits and an I-Connect007 columnist. Thompson is also the author of The Printed Circuit Designer's Guide to… Producing the Perfect Data Package. Visit I-007eBooks.com to download this book and other free, educational titles.
Suggested Items
Driving Innovation: Direct Imaging vs. Conventional Exposure
07/01/2025 | Simon Khesin -- Column: Driving InnovationMy first camera used Kodak film. I even experimented with developing photos in the bathroom, though I usually dropped the film off at a Kodak center and received the prints two weeks later, only to discover that some images were out of focus or poorly framed. Today, every smartphone contains a high-quality camera capable of producing stunning images instantly.
Hands-On Demos Now Available for Apollo Seiko’s EF and AF Selective Soldering Lines
06/30/2025 | Apollo SeikoApollo Seiko, a leading innovator in soldering technology, is excited to spotlight its expanded lineup of EF and AF Series Selective Soldering Systems, now available for live demonstrations in its newly dedicated demo room.
Indium Corporation Expert to Present on Automotive and Industrial Solder Bonding Solutions at Global Electronics Association Workshop
06/26/2025 | IndiumIndium Corporation Principal Engineer, Advanced Materials, Andy Mackie, Ph.D., MSc, will deliver a technical presentation on innovative solder bonding solutions for automotive and industrial applications at the Global Electronics A
Fresh PCB Concepts: Assembly Challenges with Micro Components and Standard Solder Mask Practices
06/26/2025 | Team NCAB -- Column: Fresh PCB ConceptsMicro components have redefined what is possible in PCB design. With package sizes like 01005 and 0201 becoming more common in high-density layouts, designers are now expected to pack more performance into smaller spaces than ever before. While these advancements support miniaturization and functionality, they introduce new assembly challenges, particularly with traditional solder mask and legend application processes.
Knocking Down the Bone Pile: Tin Whisker Mitigation in Aerospace Applications, Part 3
06/25/2025 | Nash Bell -- Column: Knocking Down the Bone PileTin whiskers are slender, hair-like metallic growths that can develop on the surface of tin-plated electronic components. Typically measuring a few micrometers in diameter and growing several millimeters in length, they form through an electrochemical process influenced by environmental factors such as temperature variations, mechanical or compressive stress, and the aging of solder alloys.