Flex Standards Update With Nick Koop
November 21, 2019 | Andy Shaughnessy, Design007 MagazineEstimated reading time: 1 minute
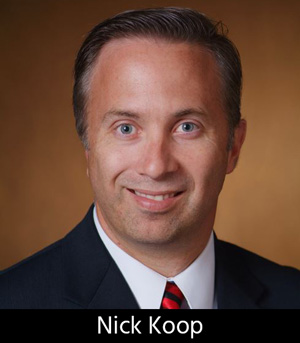
This month, I interviewed Nick Koop—director of flex technology at TTM Technologies, a veteran “flex guy” and instructor, and a leader of several IPC flex standards committees. Nick provides an update for the committees he’s involved with and discusses some of the challenges that he sees as more designers enter the world of flex.
Andy Shaughnessy: Nick, tell us a little about your background and your work with flex and rigid-flex circuits at TTM.
Nick Koop: I’ve worked in the flex and rigid-flex world since 1985 where my roles have ranged from process engineer to design engineer to general manager of a factory. And I’ve been with TTM since 2013. It has been a great experience working with such a wide range of customers and programs, solving problems that lead to success for our customers.
Shaughnessy: You’re the vice-chair of the Flexible Circuits Committee and co-chair of the 6013 Subcommittee. Give us some updates on the flex committees.
Koop: All of the flex specifications are being reviewed on an ongoing basis. We are close to releasing new versions of IPC-2223 and IPC-6013. They will include more information on microvias, finished copper thickness, and other member-requested updates. I would expect that to happen by early 2020. The supporting material specifications and test methods are also under review. In addition, there is work happening on the T-50 Terms and Definitions Guideline, which is in the middle of a substantial update. So, there is a lot happening on all fronts.
Shaughnessy: We talk to a lot of rigid board designers who are being forced into flex design. Usually, they start with flex standards, and then hopefully, they will call a flex board shop. What advice would you give any rigid folks moving into the flex world?
Koop: We are also seeing dramatic growth in flex use driven by several factors; space, weight, reliability, and cost being some of the most common. Flex provides a lot of advantages over a rigid board and discrete wiring. My initial advice would be to gain an understanding of the similarities and differences. The key differences are unique materials and a variation in material movement, which can impact alignment.
To read this entire interview, which appeared in Flex007 in the September 2019 issue of Design007 Magazine, click here.
Suggested Items
I-Connect007 Editor’s Choice: Five Must-Reads for the Week
07/11/2025 | Andy Shaughnessy, Design007 MagazineThis week, we have quite a variety of news items and articles for you. News continues to stream out of Washington, D.C., with tariffs rearing their controversial head again. Because these tariffs are targeted at overseas copper manufacturers, this news has a direct effect on our industry.I-Connect007 Editor’s Choice: Five Must-Reads for the Week
Digital Twin Concept in Copper Electroplating Process Performance
07/11/2025 | Aga Franczak, Robrecht Belis, Elsyca N.V.PCB manufacturing involves transforming a design into a physical board while meeting specific requirements. Understanding these design specifications is crucial, as they directly impact the PCB's fabrication process, performance, and yield rate. One key design specification is copper thieving—the addition of “dummy” pads across the surface that are plated along with the features designed on the outer layers. The purpose of the process is to provide a uniform distribution of copper across the outer layers to make the plating current density and plating in the holes more uniform.
Trump Copper Tariffs Spark Concern
07/10/2025 | I-Connect007 Editorial TeamPresident Donald Trump stated on July 8 that he plans to impose a 50% tariff on copper imports, sparking concern in a global industry whose output is critical to electric vehicles, military hardware, semiconductors, and a wide range of consumer goods. According to Yahoo Finance, copper futures climbed over 2% following tariff confirmation.
Happy’s Tech Talk #40: Factors in PTH Reliability—Hole Voids
07/09/2025 | Happy Holden -- Column: Happy’s Tech TalkWhen we consider via reliability, the major contributing factors are typically processing deviations. These can be subtle and not always visible. One particularly insightful column was by Mike Carano, “Causes of Plating Voids, Pre-electroless Copper,” where he outlined some of the possible causes of hole defects for both plated through-hole (PTH) and blind vias.
Trouble in Your Tank: Can You Drill the Perfect Hole?
07/07/2025 | Michael Carano -- Column: Trouble in Your TankIn the movie “Friday Night Lights,” the head football coach (played by Billy Bob Thornton) addresses his high school football team on a hot day in August in West Texas. He asks his players one question: “Can you be perfect?” That is an interesting question, in football and the printed circuit board fabrication world, where being perfect is somewhat elusive. When it comes to mechanical drilling and via formation, can you drill the perfect hole time after time?