Space Saving, 3.3V I/O FBGA Two-Speed Synchro/Resolver Combiner from DDC
November 22, 2019 | Data Device Corporation (DDC)Estimated reading time: 1 minute
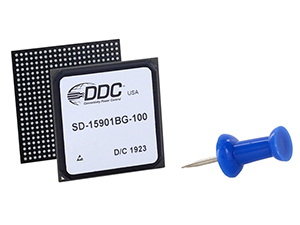
Data Device Corporation (DDC) introduces a redesigned version of its popular Synchro/Resolver two-speed combiner, now featuring 3.3V I/O within a compact and highly efficient FBGA (Fine Pitch Ball Grid Array) package. The SD-15901 FBGA design provides space and power savings with a 34% smaller footprint and 35% less power dissipation than the previous generation, enabling SWaP optimization of PCB layout and ease of assembly with ball grid array surface mounting.
Using coarse and fine digital angle inputs, the combiner provides up to 22-bit angle resolution, making it ideal for high-performance position control systems requiring real-time precision resolution. Additionally, the SD-15901 is RoHS compliant, and rated for the full military temperature range (-55°C to +125°C).
Benefits include:
- Optimized Performance and Design
- High resolution (up to 22 bits)
- Small footprint (23 mm x 23 mm) saves board space, 34% smaller compared with (28.4 mm x 28.4 mm) of previous generation
- Low power dissipation, 35% less power dissipated than previous generation (at nominal operation)
- FBGA design enables ease of assembly
- Flexibility & Ease of Use
- Can be used with all 3.3V Synchro/Resolver converters and processors, no logic shifters required
- No software or calibration required
- Environmental
- Military temperature range (-55°C to +125°C)
- RoHS compliant
"DDC’s second generation Synchro/Resolver two-speed combiner offers significant SWaP savings along with high resolution, to enable optimized PDB design," Roger Tomassi, DDC Product Line Manager, Motion Feedback.
Suggested Items
Microchip Enters into Partnership Agreement with Delta Electronics on Silicon Carbide Solutions
07/18/2025 | Globe NewswireThe growth of artificial intelligence (AI) and the electrification of everything are driving an ever-increasing demand for higher levels of power efficiency and reliability.
ESD Alliance Reports Electronic System Design Industry Posts $5.1 Billion in Revenue in Q1 2025
07/16/2025 | SEMIElectronic System Design (ESD) industry revenue increased 12.8% to $5,098.3 million in the first quarter of 2025 from the $4,521.6 million registered in the first quarter of 2024, the ESD Alliance, a SEMI Technology Community, announced in its latest Electronic Design Market Data (EDMD) report.
Beyond Design: Refining Design Constraints
07/17/2025 | Barry Olney -- Column: Beyond DesignBefore starting any project, it is crucial to develop a thorough plan that encompasses all essential requirements. This ensures that the final product not only aligns with the design concept but is also manufacturable, reliable, and meets performance expectations. High-speed PCB design requires us to not only push technological boundaries but also consider various factors related to higher frequencies, faster transition times, and increased bandwidths during the design process.
Prague PEDC: Call for Abstracts Deadline July 31
07/16/2025 | Pan-European Electronics Design Conference (PEDC)The second Pan-European Electronics Design Conference (PEDC) will take place Jan. 21-22, 2026, in Prague, Czech Republic. The call for abstracts deadline is July 31. Organized jointly by the German Electronics Design and Manufacturing Association (FED) and the Global Electronics Association PEDC serves as a European platform for knowledge exchange, networking, and innovation in electronics design and development.
The Pulse: Design Constraints for the Next Generation
07/17/2025 | Martyn Gaudion -- Column: The PulseIn Europe, where engineering careers were once seen as unpopular and lacking street credibility, we have been witnessing a turnaround in the past few years. The industry is now welcoming a new cohort of designers and engineers as people are showing a newfound interest in the profession.