Airbus Demonstrates First Fully Automatic Vision-Based Take-Off
January 17, 2020 | AirbusEstimated reading time: 1 minute
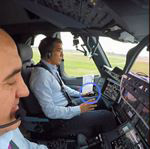
Airbus has successfully performed the first fully automatic vision-based take-off using an Airbus Family test aircraft at Toulouse-Blagnac airport. The test crew comprising of two pilots, two flight test engineers and a test flight engineer took off initially at around 10h15 on 18 December and conducted a total of 8 take-offs over a period of four and a half hours.
“The aircraft performed as expected during these milestone tests. While completing alignment on the runway, waiting for clearance from air traffic control, we engaged the auto-pilot,” said Airbus Test Pilot Captain Yann Beaufils. “We moved the throttle levers to the take-off setting and we monitored the aircraft. It started to move and accelerate automatically maintaining the runway centre line, at the exact rotation speed as entered in the system. The nose of the aircraft began to lift up automatically to take the expected take-off pitch value and a few seconds later we were airborne.”
Rather than relying on an Instrument Landing System (ILS), the existing ground equipment technology currently used by in-service passenger aircraft in airports around the world where the technology is present, this automatic take-off was enabled by image recognition technology installed directly on the aircraft.
Automatic take-off is an important milestone in Airbus’ Autonomous Taxi, Take-Off & Landing (ATTOL) project. Launched in June 2018, ATTOL is one of the technological flight demonstrators being tested by Airbus in order to understand the impact of autonomy on aircraft. The next steps in the project will see automatic vision-based taxi and landing sequences taking place by mid-2020.
Airbus’ mission is not to move ahead with autonomy as a target in itself, but instead to explore autonomous technologies alongside other innovations in areas such as materials, electrification and connectivity. By doing so, Airbus is able to analyse the potential of these technologies in addressing the key industrial challenges of tomorrow, including improving air traffic management, addressing pilot shortages and enhancing future operations. At the same time Airbus is leveraging these opportunities to further improve aircraft safety while ensuring today’s unprecedented levels are maintained.
For autonomous technologies to improve flight operations and overall aircraft performance, pilots will remain at the heart of operations. Autonomous technologies are paramount to supporting pilots, enabling them to focus less on aircraft operation and more on strategic decision-making and mission management.
Suggested Items
TRI to Exhibit at SMTA Queretaro Expo 2025
07/16/2025 | TRITest Research, Inc. (TRI), the leading provider of test and inspection systems for the electronics manufacturing industry, is pleased to announce plans to exhibit at the SMTA Querétaro Expo 2025, scheduled to take place on July 24, 2025, at the Querétaro Centro de Congresos y Teatro Metropolitano.
Knocking Down the Bone Pile: Addressing End-of-life Component Solderability Issues, Part 4
07/16/2025 | Nash Bell -- Column: Knocking Down the Bone PileIn 1983, the Department of Defense identified that over 40% of military electronic system failures in the field were electrical, with approximately 50% attributed to poor solder connections. Investigations revealed that plated finishes, typically nickel or tin, were porous and non-intermetallic.
Meet the Author Podcast: Martyn Gaudion Unpacks the Secrets of High-Speed PCB Design
07/16/2025 | I-Connect007In this special Meet the Author episode of the On the Line with… podcast, Nolan Johnson sits down with Martyn Gaudion, signal integrity expert, managing director of Polar Instruments, and three-time author in I-Connect007’s popular The Printed Circuit Designer’s Guide to... series.
TTCI Joins Printed Circuit Engineering Association to Strengthen Design-to-Test Collaboration and Workforce Development
07/09/2025 | The Test Connection Inc.The Test Connection Inc. (TTCI), a leading provider of electronic test and manufacturing solutions, is proud to announce its membership in the Printed Circuit Engineering Association (PCEA), further expanding the company’s efforts to support cross-functional collaboration, industry standards, and technical education in the printed circuit design and manufacturing community.
Study on Resonance Mitigation in Metallic Shielding for Integrated Circuits
07/08/2025 | Maria Cuesta-Martin, Victor Martinez, Vidal Gonzalez Aguado, Würth ElektronikInherent cavity resonant modes often lead to significant degradation of shielding effectiveness, responsible for unwanted electromagnetic coupling. Cavity resonant modes of the metal shielding enclosure can produce two adverse problems: the mutual coupling among different RF modules and shielding effectiveness reduction of the metal enclosure. The cabinets serve to shield certain components from electromagnetic interference (EMI). However, these cavities present some resonance peaks at 5 GHz, making it impossible to use them at higher frequencies.