-
- News
- Books
Featured Books
- pcb007 Magazine
Latest Issues
Current IssueThe Hole Truth: Via Integrity in an HDI World
From the drilled hole to registration across multiple sequential lamination cycles, to the quality of your copper plating, via reliability in an HDI world is becoming an ever-greater challenge. This month we look at “The Hole Truth,” from creating the “perfect” via to how you can assure via quality and reliability, the first time, every time.
In Pursuit of Perfection: Defect Reduction
For bare PCB board fabrication, defect reduction is a critical aspect of a company's bottom line profitability. In this issue, we examine how imaging, etching, and plating processes can provide information and insight into reducing defects and increasing yields.
Voices of the Industry
We take the pulse of the PCB industry by sharing insights from leading fabricators and suppliers in this month's issue. We've gathered their thoughts on the new U.S. administration, spending, the war in Ukraine, and their most pressing needs. It’s an eye-opening and enlightening look behind the curtain.
- Articles
- Columns
- Links
- Media kit
||| MENU - pcb007 Magazine
Aurora Circuits on Ultra-Heavy Copper PCBs
August 3, 2020 | Dan Beaulieu, D.B. Management GroupEstimated reading time: 3 minutes
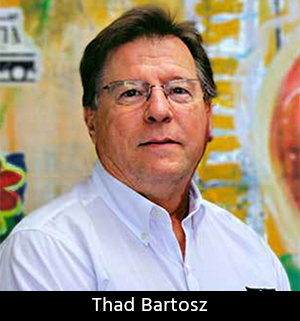
It’s always fun to talk with a company that can do something different—in this case, ultra-heavy copper PCBs, meaning over 20-ounce copper. Wanting to know more about this, I talked to Aurora Circuits Director of Business Development Thad Bartosz, who is one of our industry experts when it comes to ultra-heavy copper technology.
Dan Beaulieu: Thad, it’s good talking to you today. Let’s start with the basics. What is heavy copper?
Thad Bartosz: Heavy copper used to be defined as 4–5 ounce, but we do that for a snack. Aurora is capable of fabricating SS, NPTH, PTH, and multilayer types with up to 20-oz copper layers.
Beaulieu: What defines ultra-heavy copper?
Bartosz: Ounces of copper have been defined in ounces per square foot of area on the process panel. The thickness of the copper foil is based on 0.0014” per oz. Copper weights of 4–5 ounces are made with electrodeposited copper (ED), and ultra-heavy copper sheets are made with rolled annealed (RA) copper that must be treated to laminate to dielectrics used in fabrication.
Beaulieu: How many ounces of copper can you do at Aurora?
Bartosz: We have delivered PCBs with etched copper up to 20 ounces and would work with customers that may require any copper thickness.
Beaulieu: Why doesn’t every shop build this technology?
Bartosz: You need to have the proper equipment and process capabilities—some of these are customer or Aurora proprietary—so that you can fabricate a usable product that meets customer requirements.
Beaulieu: How did you get involved with this technology?
Bartosz: We have been building ultra-heavy copper products since 2003 when a customer asked if we could do this as they were having issues with their current source.
Beaulieu: What special equipment and processes do you have that allow you to build ultra-heavy copper boards?
Bartosz: As I mentioned earlier, these are processes that have been developed over years of sampling and production processing. We start with a sample run to establish a feasible process and then scale up for production. Etching is normally a big factor as well as machining, so you acquire equipment to properly process the PCB to make an acceptable finished product.
Beaulieu: What technology requires ultra-heavy copper?
Bartosz: Circuit boards that need high current or thermal dissipation like solar and wind power collection, aerospace/military, telecommunications, and automotive applications.
Beaulieu: What kind of end-products need it?
Bartosz: Some products include automotive junction boxes, battery management systems, and high-power circuits that have MOSFETs, IGBTs, and other high-current components, running hundreds of amps through the circuitry. For those who may not know, MOSFETs and IGBTs are a couple of power devices/components that can handle high-voltage and high-current needs. You will find them on inverters, converters, and power supplies.
Beaulieu: How do you think it will be used in the future?
Bartosz: Currently, designs have been made for power distribution, power collection, battery-powered transportation, and LED lighting. Future use will depend on new applications needed in the marketplace. You also need a supplier that changes with the market to meet these specialized needs. It will definitely be used more in the future.
Beaulieu: Is this kind of technology being designed right now?
Bartosz: Yes, it is still used in the automotive and power markets, such as new EV and autonomous vehicles where battery technology has higher current requirements and power-generation systems, solar, wind, or conventional types as their technology changes.
Beaulieu: How many ultra-heavy copper boards have you built?
Bartosz: Aurora has shipped over five million boards of single-sided, PTH, and multilayer designs over the last 10 years. Many of these were for junction boxes or battery systems in automobiles. For a few years, we shipped over 400,000 6/6 copper PCBs to China. We have processed over 800 tons (based on oz/sq ft) and over 1.7 million square feet without any EPA violations.
Beaulieu: Before we end, tell us a little bit about Aurora Circuits.
Bartosz: We have over 60 years of experience in printed circuit fabrication, providing advanced thermal management and interconnect technology solutions for PCB designs and specialty products. Product specialty areas include polymer thick-film (PTF) resistors, metal-clad materials for LED lighting and other markets, durable plating for contact areas, and, of course, ultra-heavy copper. We partner with companies to help them to maximize profitability and production sustainability.
Beaulieu: Thank you, Thad.
Bartosz: No problem, Dan.
Read more about Aurora Circuits and ultra-heavy copper PCBs here.
Suggested Items
Copper Price Surge Raises Alarms for Electronics
07/15/2025 | Global Electronics Association Advocacy and Government Relations TeamThe copper market is experiencing major turbulence in the wake of U.S. President Donald Trump’s announcement of a 50% tariff on imported copper effective Aug. 1. Recent news reports, including from the New York Times, sent U.S. copper futures soaring to record highs, climbing nearly 13% in a single day as manufacturers braced for supply shocks and surging costs.
I-Connect007 Editor’s Choice: Five Must-Reads for the Week
07/11/2025 | Andy Shaughnessy, Design007 MagazineThis week, we have quite a variety of news items and articles for you. News continues to stream out of Washington, D.C., with tariffs rearing their controversial head again. Because these tariffs are targeted at overseas copper manufacturers, this news has a direct effect on our industry.I-Connect007 Editor’s Choice: Five Must-Reads for the Week
Digital Twin Concept in Copper Electroplating Process Performance
07/11/2025 | Aga Franczak, Robrecht Belis, Elsyca N.V.PCB manufacturing involves transforming a design into a physical board while meeting specific requirements. Understanding these design specifications is crucial, as they directly impact the PCB's fabrication process, performance, and yield rate. One key design specification is copper thieving—the addition of “dummy” pads across the surface that are plated along with the features designed on the outer layers. The purpose of the process is to provide a uniform distribution of copper across the outer layers to make the plating current density and plating in the holes more uniform.
Trump Copper Tariffs Spark Concern
07/10/2025 | I-Connect007 Editorial TeamPresident Donald Trump stated on July 8 that he plans to impose a 50% tariff on copper imports, sparking concern in a global industry whose output is critical to electric vehicles, military hardware, semiconductors, and a wide range of consumer goods. According to Yahoo Finance, copper futures climbed over 2% following tariff confirmation.
Happy’s Tech Talk #40: Factors in PTH Reliability—Hole Voids
07/09/2025 | Happy Holden -- Column: Happy’s Tech TalkWhen we consider via reliability, the major contributing factors are typically processing deviations. These can be subtle and not always visible. One particularly insightful column was by Mike Carano, “Causes of Plating Voids, Pre-electroless Copper,” where he outlined some of the possible causes of hole defects for both plated through-hole (PTH) and blind vias.