-
- News
- Books
Featured Books
- pcb007 Magazine
Latest Issues
Current IssueThe Hole Truth: Via Integrity in an HDI World
From the drilled hole to registration across multiple sequential lamination cycles, to the quality of your copper plating, via reliability in an HDI world is becoming an ever-greater challenge. This month we look at “The Hole Truth,” from creating the “perfect” via to how you can assure via quality and reliability, the first time, every time.
In Pursuit of Perfection: Defect Reduction
For bare PCB board fabrication, defect reduction is a critical aspect of a company's bottom line profitability. In this issue, we examine how imaging, etching, and plating processes can provide information and insight into reducing defects and increasing yields.
Voices of the Industry
We take the pulse of the PCB industry by sharing insights from leading fabricators and suppliers in this month's issue. We've gathered their thoughts on the new U.S. administration, spending, the war in Ukraine, and their most pressing needs. It’s an eye-opening and enlightening look behind the curtain.
- Articles
- Columns
- Links
- Media kit
||| MENU - pcb007 Magazine
Estimated reading time: 3 minutes
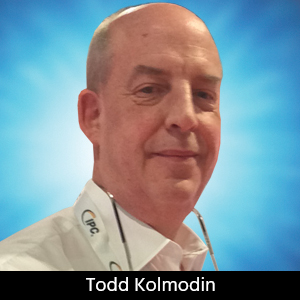
Testing Todd: Too Much Automation?
The last six months have brought monumental changes to commerce, manufacturing, recreation, and almost every aspect of our daily lives. As we slowly begin to emerge from this pandemic, we are finding that what was routine six months ago has drastically changed and may never be the same.
This has caused us all to rethink our daily lives and how we go about existing in this new normal. Workplaces have changed for those that still exist, while others have become extinct. Virtual workplaces are gaining traction, as well as telecommuting and more reliance on the internet for virtual meetings, webinars, and many other daily activities that required face-to-face collaboration. For many of us, life has changed forever.
We have to rethink our personal lives and adjust to the changing conditions so that we can continue to thrive. As humans, we have the ability to experience, review, react, and change quickly to adapt to changing conditions. Whether it’s staying home, wearing a mask, telecommuting, or doing nothing, those decisions come from our ability to think and analyze. We rethink, adapt, and thrive.
With that in mind, it causes us to rethink other aspects regarding manufacturing. The hot topic over the last decade or more has been automation—automate, automate, automate. Of course, after the initial investment, automation can save on costs. Fewer humans are required, throughput is predictable, and repeatability can be expected. Flip the switch, turn off the lights, and the required products will be ready to ship in 12 hours. Right? Not so fast.
Although automation can save costs and provide repeatable results, when something goes wrong, very bad things can happen, as Apple and Foxconn have learned[1]. Automation lacks one critical component: the ability to question, reason, and evolve on its own. At the end of the day, the robot does exactly what it is told to do, over and over again. Yes, robots are predictable, can work in the dark and don’t need breaks except for periodic maintenance. However, all the optics, conveyors, arms, and brute strength that automation can provide is no match for the grey matter of the human brain. Highly skilled human labor is still needed.
In many aspects of automation, providing the human replacement for mundane, repetitive tasks works out fine. More complex tasks, although campaigned for automation, should be rethought. Here, the human element still makes a valuable difference—the ability to question, analyze, think critically, and create are traits that automation will always lack regardless of how strong the AI may be or the complexity of the program driving the process. It is not thinking. It is doing exactly what it is told. To quote David Bourne, principal systems scientist at The Robotics Institute at Carnegie Mellon University, on his work with Apple and Foxconn [1], “Robotics and automation are fantastic and amazing when it works, But when something breaks, God knows what happens.” Enough said.
As we are all in our rethinking mode, retooling our lives and considering how we do business, we must ask, “How much automation is enough?” We can easily get caught up in the cost savings and immediate gratification. But remember, the automation you implemented is a snapshot of today’s technology. It will do what you want today, but it will not evolve. It cannot learn without costs. (maintenance contract, service agreement, etc.).
However, your employees at these critical processes think dynamically, analyze, criticize, ask questions, provide options, and evolve. They will always be necessary. There is a place for automation, but balancing the cost savings vs. the liability the automation may create are bullet items that should be on any engineer and management whiteboard.
Be safe.?
Reference
1. W. Gallagher, “How Apple learned automation can’t match human skill,” AppleInsider, June 5, 2020.
This column originally appeared in the July 2020 issue of PCB007 Magazine.
More Columns from Testing Todd
Testing Todd: Why 4-wire Kelvin?Testing Todd: Why TDR?
Testing Todd: Positivity Boosts Employee Morale
Testing Todd: Preparing Employees for the Long Haul
Testing Todd: Where Can We Improve?
Testing Todd: Turning Into the Wind
Testing Todd: Coming Back to Life—Design Recovery
Testing Todd: Decision Time—Invest or Delegate?