-
- News
- Books
Featured Books
- pcb007 Magazine
Latest Issues
Current IssueThe Hole Truth: Via Integrity in an HDI World
From the drilled hole to registration across multiple sequential lamination cycles, to the quality of your copper plating, via reliability in an HDI world is becoming an ever-greater challenge. This month we look at “The Hole Truth,” from creating the “perfect” via to how you can assure via quality and reliability, the first time, every time.
In Pursuit of Perfection: Defect Reduction
For bare PCB board fabrication, defect reduction is a critical aspect of a company's bottom line profitability. In this issue, we examine how imaging, etching, and plating processes can provide information and insight into reducing defects and increasing yields.
Voices of the Industry
We take the pulse of the PCB industry by sharing insights from leading fabricators and suppliers in this month's issue. We've gathered their thoughts on the new U.S. administration, spending, the war in Ukraine, and their most pressing needs. It’s an eye-opening and enlightening look behind the curtain.
- Articles
- Columns
- Links
- Media kit
||| MENU - pcb007 Magazine
Estimated reading time: 4 minutes
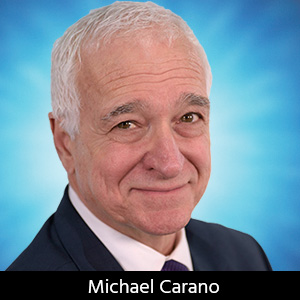
Contact Columnist Form
Trouble in Your Tank: A Process Engineer’s Guide to Electroless Copper
The electroless copper metalization process (also known as plated through-hole or PTH) is a system of multiple process steps with the expressed goal of producing a continuous, void-free, and tightly adherent deposit through the vias and surface of the circuit board. While these various steps in the process all play a role in the successful operation of the process, the subject of this column is on the electroless copper plating solution itself. The discussion will focus on a copper formulation based on copper chloride, EDTA, formaldehyde, and sodium hydroxide.
The Autocatalytic Copper Process
Electroless copper plating solutions by their very nature are thermodynamically unstable. There are several side reactions that take place in the course of the everyday operation of the electroless copper plating solution. The stability of the plating solution requires diligence on the part of the process engineer. For copper ions to be reduced to copper metal, the inherent instability of the electroless copper solution is expected. However, the stability of the solution must be controlled to prevent deleterious defects, including interconnect defect (ICD), excessive plating thickness, and excessive stress of the copper deposit. Deposit stress alone can lead to copper blistering from the hole wall and separating from the internal layer copper interface.
A few key aspects of stability include the following:
- Stability will decrease as specific gravity increases.
- Stability will decrease as the temperature increases.
- Although stability is improved by running at a lower temperature, the rate is sacrificed to the point where a medium deposit bath is unattainable.
- Low loading with intermittent use (<3 sq. ft./gal/shift) will lower the amount of active stabilizer in the bath and decrease stability. When this occurs, excessive copper loss is expected.
- The specific gravity of the electroless copper plating solution should be monitored each shift. As specific gravity increases, copper loss or plate-out increases (Figure 1).
- Note: Consult the supplier of the particular electroless copper process in use. There ?may be differences in specific gravity recommendations.
- The process tank containing the electroless copper solution should be etched out every few weeks, depending on operation and maintenance. Copper deposits that form on the tank walls and heaters due to normal plate-out must be removed as part of process maintenance. It is good practice to have two electroless copper plating tanks in the PTH line. As one goes offline for maintenance, the second one is ready to go.
- Sporadic short-term fluctuations in temperature have no adverse effect on stability.
Electroless Copper Solution Life
As much as we would like them to, plating solutions do not last forever. There are numerous factors that negatively impact the useful life of a plating solution. The electroless copper solution is no exception.
Factors affecting electroless copper solution life may include:
- Tank condition (is there copper plate-out on the tank walls?)
- Bail-out schedule
- Filtration (are the copper particles being effectively removed)
- The amount of time spent operating bath out of chemistry and temperature specifications
- Extended idle periods at temperature and concentration
- Improper bath turnover from low loading
- Poor rinsing/drag-in of catalyst and accelerator
- The buildup of formate and other by-products
The bath ages with the buildup of formate, carbonate, and chloride as by-products. These by-products are measured with specific gravity but are not individually differentiated. Chloride increases linearly with the consumption of cupric chloride (if a copper sulfate electroless process is in use, by-product build up rates will be different). Carbonate is another by-product and is formed as carbon dioxide in the air reacts with sodium hydroxide in the bath. Assuming air flow is constant, carbonate will also build linearly. Formate also tends to grow linearly at low levels through several reactions:
Excessive formate is known to promote the creation of additional formate through the breakdown of formaldehyde resulting in the generation of copper(I) oxide (reaction 2), which will, in turn, create copper dust through the following reaction:
Therefore, as conventional electroless copper solutions age with increased metal turnovers, and normal plating solution age, there is a higher formate buildup. Therefore, there will be increased instability in the copper plating solution due to the accelerated formaldehyde breakdown rate. When this occurs, the go-to tactic is to bail out a portion of the working plating solution and replace that with fresh electroless copper components. This reduces the specific gravity to a lower level. Also, keep in mind that the formation of carbonate and formate is not linear. And the buildup is not easily predicted.
Again, unlike electrolytic plating solutions, electroless copper is thermally unstable. While suppliers have worked diligently to ensure reasonable stability of the copper process, by-product buildup, catalyst drag-in, and other factors will create conditions ripe for plate-out and copper loss. Drain the boards before entry into the electroless copper solution. Water from rinses may contain both organic and inorganic contaminants. Follow recommended times of immersion in all proprietary pre-plate solutions and rinse thoroughly after each step. Palladium drag-in to electroless copper may cause instantaneous solution decomposition.
Always strive to use best practices when it comes to rinsing, filtration, and monitoring of any contaminants.
This column originally appeared in the August 2020 issue of PCB007 Magazine.
More Columns from Trouble in Your Tank
Trouble in Your Tank: Can You Drill the Perfect Hole?Trouble in Your Tank: Yield Improvement and Reliability
Trouble in Your Tank: Causes of Plating Voids, Pre-electroless Copper
Trouble in Your Tank: Organic Addition Agents in Electrolytic Copper Plating
Trouble in Your Tank: Interconnect Defect—The Three Degrees of Separation
Trouble in Your Tank: Things You Can Do for Better Wet Process Control
Trouble in Your Tank: Processes to Support IC Substrates and Advanced Packaging, Part 5
Trouble in Your Tank: Materials for PWB Fabrication—Drillability and Metallization