Understanding MIL-PRF-31032, Part 4
October 20, 2020 | Anaya Vardya, American Standard CircuitsEstimated reading time: 3 minutes
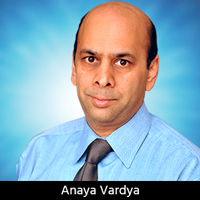
Overview
Continuing with Part 4 of the discussion on understanding the military PCB performance standard MIL-PRF-31032, the next step in the process is to create four new procedures to address the unique requirements of the military.
Qualification and Add-On Procedure
This process provides the guidelines for the initial qualification of the company, as well as a path for future add-on qualifications. The first thing that needs to be included is the process for developing the qualification test vehicle. This is the specific PCB design that will be used to build the qualification boards. The documentation required must also be identified, such as production traveler, test vehicle design, drawings, multilayer layup, etc.
Test Vehicle
A company will qualify for specific technology and will need to develop a qualification test plan, which is a document that specifies the following minimum attributes of the qualification board:
- Max. Number of Layers and Dielectric Type
- Max. Panel Size
- Max. Board Thickness
- Min. Drilled Hole Before Plating
- Aspect Ratio
- Min. Conductor Width
- Via Structure
- Min. Conductor Space
- Hole Preparation
- Hole Wall Conductive Coating
- Copper Plating
- Solder Resist
- Silkscreen
- Final Finish
- Additional Fabrication Capabilities
- Controlled Impedance
It is important to note here that the qualification “flows down” but not “up.” In other words, if an 18-layer is qualified, layer counts less than 18 layers can be built as long as the other above parameters are the same, but a 20-layer would not be allowed.
Sample Size and Data Requirements
The next section would be to establish the lot size of the qualification lot and the sample sizes that will be used for testing. The data recording and retention of all qualification records must be defined, including coupons and any extra boards left over from the qualification lot.
Failure Analysis and Resubmission
A DLA-approved third-party testing lab must be selected to use for the initial qualification as well as the ongoing monthly testing. Should a submitted sample fail any tests, this procedure needs to have a provision for failure analysis and corrective action. This typically leverages the existing processes already in place. The rules for resubmitting new qualification boards must also be defined here, particularly that additional extra samples from the failed lot cannot be used.
Qualification Test Summary and Reporting
This section outlines the components for the summary that is needed to be submitted to the DLA after all tests and inspections have been successfully performed, including the third-party lab). This includes things like the travelers, internal and external test and inspection results, lot conformance forms and results, failure mode for any rejections, dimensional and electrical test parameters and measurements, and a copy of the qualification test plan.
Add-On Qualification
MIL-PRF-31032 allows for the expansion of the qualified technology through the add-on qualification process. A technology that falls within 25% of the current qualified technology can be built with a new qualification test plan and TRB approval. For example, with a qualified 18-layer, a 22-layer could be qualified through the add-on process.
The same would apply to line width, hole size, etc. There is no need to wait for DLA approval in these cases; they will verify the add-on qualification data during their next regular visit/audit. Anything greater than a 25% technology change will require a new full qualification like the initial qualification.
Conclusion
This wraps up qualification and add-on procedures. Part 5 will focus on the next unique procedure needed to produce MIL-PRF-31032 PCBs.
Editor’s note: Read Part 1, Part 2, and Part 3.
Anaya Vardya is president and CEO of American Standard Circuits; co-author of The Printed Circuit Designer’s Guide to… Fundamentals of RF/Microwave PCBs and Flex and Rigid-Flex Fundamentals; and author of Thermal Management: A Fabricator's Perspective. Visit I-007eBooks.com to download these and other free, educational titles. He also co-authored “Fundamentals of PCB Technology.”
Suggested Items
SHENMAO Strengthens Semiconductor Capabilities with Acquisition of PMTC
07/10/2025 | SHENMAOSHENMAO America, Inc. has announced the acquisition of Profound Material Technology Co., Ltd. (PMTC), a premier Taiwan-based manufacturer of high-performance solder balls for semiconductor packaging.
KYZEN to Highlight Understencil and PCB Cleaners at SMTA Querétaro Expo and Tech Forum
07/09/2025 | KYZEN'KYZEN, the global leader in innovative environmentally responsible cleaning chemistries, will exhibit at the SMTA Querétaro Expo & Tech Forum, scheduled to take place Thursday, July 24, at Centro de Congresos y Teatro Metropolitano de Querétaro.
Driving Innovation: Direct Imaging vs. Conventional Exposure
07/01/2025 | Simon Khesin -- Column: Driving InnovationMy first camera used Kodak film. I even experimented with developing photos in the bathroom, though I usually dropped the film off at a Kodak center and received the prints two weeks later, only to discover that some images were out of focus or poorly framed. Today, every smartphone contains a high-quality camera capable of producing stunning images instantly.
Hands-On Demos Now Available for Apollo Seiko’s EF and AF Selective Soldering Lines
06/30/2025 | Apollo SeikoApollo Seiko, a leading innovator in soldering technology, is excited to spotlight its expanded lineup of EF and AF Series Selective Soldering Systems, now available for live demonstrations in its newly dedicated demo room.
Indium Corporation Expert to Present on Automotive and Industrial Solder Bonding Solutions at Global Electronics Association Workshop
06/26/2025 | IndiumIndium Corporation Principal Engineer, Advanced Materials, Andy Mackie, Ph.D., MSc, will deliver a technical presentation on innovative solder bonding solutions for automotive and industrial applications at the Global Electronics A