-
-
News
News Highlights
- Books
Featured Books
- pcb007 Magazine
Latest Issues
Current IssueThe Hole Truth: Via Integrity in an HDI World
From the drilled hole to registration across multiple sequential lamination cycles, to the quality of your copper plating, via reliability in an HDI world is becoming an ever-greater challenge. This month we look at “The Hole Truth,” from creating the “perfect” via to how you can assure via quality and reliability, the first time, every time.
In Pursuit of Perfection: Defect Reduction
For bare PCB board fabrication, defect reduction is a critical aspect of a company's bottom line profitability. In this issue, we examine how imaging, etching, and plating processes can provide information and insight into reducing defects and increasing yields.
Voices of the Industry
We take the pulse of the PCB industry by sharing insights from leading fabricators and suppliers in this month's issue. We've gathered their thoughts on the new U.S. administration, spending, the war in Ukraine, and their most pressing needs. It’s an eye-opening and enlightening look behind the curtain.
- Articles
- Columns
- Links
- Media kit
||| MENU - pcb007 Magazine
IDTechEx: The Future of Sustainable Electronics Manufacturing
December 12, 2022 | PRNewswireEstimated reading time: 5 minutes
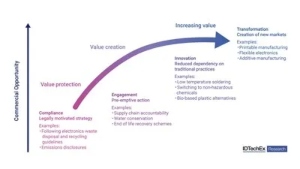
A new wave of electronics manufacturing is on the horizon, aiming to satisfy the increasing demand for sustainability and mitigate the impact of volatile energy prices. With the electronics industry accounting for 4% of global greenhouse gas emissions, it requires substantial innovation to reduce its environmental footprint. Fortunately, this area has a lot of movement, with several potentially revolutionary technologies entering the scene. IDTechEx's report, "Sustainable Electronics Manufacturing 2023-2033", explores the key opportunities for sustainable innovation and the most promising new manufacturing approaches. The report concentrates on the fundamental building blocks of electronics – printed circuit boards (PCBs) and integrated circuits (ICs).
Incentives for Sustainable Electronics Manufacturing
Sustainability within the semiconductor and electronics industries is being driven forward by government mandates and green investment initiatives. Increasingly relevant to the survival of traditional manufacturers is the conscious choice of the public to only purchase from, and even only work for, companies that prioritize sustainable practices.
Environmentalism is often perceived as an obstacle-laden with legislative red tape and burdensome disclosures. However, companies that embrace environmentalism reap long-term rewards, and as such, the negative perception is replaced by one of opportunity. The implementation of low-emission manufacturing processes or the adoption of material recycling and recovery schemes can be the financially astute choice presenting an opportunity to reduce costs associated with energy consumption, waste treatment, and superfluous steps. Prioritizing environmentalism keeps the industry ahead of the curve as legislation becomes stricter while positioning individual companies well to benefit from designated ESG investment.
As energy prices rise globally, low temperatures and rapid processing methods become more attractive. Some of these methods employ additive approaches that substantially cut waste by printing material only where needed. This spares manufacturers the costs and emissions associated with excess materials and etching required in traditional subtractive manufacturing. For example, switching to additive methods of PCB manufacturing can lower water consumption by up to 95% - an outcome that could save the sector hundreds of millions of liters of water annually.
IDTechEx's analysis expects additive manufacturing to be particularly significant to the scaling of flexible printed circuit boards. Flexible PCBs are an important part of the emerging electronics industry as they enable a wider variety of applications than conventional rigid electronics. Flexible PCBs inherently require an overhaul of traditional processing – for example, using plastic or paper rather than conventional FR substrates. Embracing a new technology enables scope for further changes, such as transitioning to new materials and additive methods. Low-temperature processing may also be imperative for PCBs made on plastics such as polyethylene terephthalate (PET), considering that these have relatively low heat tolerances.
Digitization for Smart Manufacturing
Sustainable electronics manufacturing presents many opportunities to be more efficient, reduce waste, and improve cost-effectiveness. Sustainable manufacturing can be facilitated through artificial intelligence and Internet of Things. Using smart digital manufacturing methods to automate processes as well as sensor technology to detect leaks and improper material usage can help companies to minimize waste and cut down on excess costs.
Digital data analysis can help remove superfluous steps and illustrate where to focus efforts to eliminate excess material and energy consumption. Digitization is becoming increasingly popular, with many household name brands adopting similar measures. At the end of 2021, Apple announced it had joined Sustainable Semiconductor Technologies and Systems (SSTS) – a program created by the Belgian research institute, imec, to reduce the environmental impact of semiconductor manufacturing. Imec's SSTS program aims to improve sustainability by employing digital solutions to identify improvements in 3 key areas: energy consumption, greenhouse gas emissions, and water consumption. Many other well-known companies, including Microsoft, Amazon, and ASML, are known to be employing imec's digital analysis.
Reshoring Expected to Reduce Emissions
The past three years have been full of upheaval, with pandemics, trade wars, and energy crises dominating front-page headlines across the world. The turmoil has brought to sharp relief how fragile the multi-billion dollar electronics industry is. The global chip shortage is a salient example of the damaging consequences of supply chain disruption.
While it may not be possible to immunize supply chains against all eventualities fully, there are acts that can be taken to minimize risk and reduce emissions. One method involves reducing dependency on geographic monopolies such as the Asia Pacific region, which currently dominates electronics manufacturing. Re-distribution of the electronics industry is gaining momentum of late, with hundreds of billions of dollars worth of funding going into revitalizing localized electronics manufacturing in the West, as outlined in both the US CHIPS & Science Act and the European Chips Act.
Increasingly, access to renewable energy is becoming a major factor as companies build new fabrication facilities. Samsung has already achieved 100% renewable energy for all of its sites in the US and China, with other household name companies following suit, such as Apple, IBM, Intel, and Nokia. The availability of renewable energy sources varies substantially geographically, with the US and Europe leading the way with clean energy options compared to much of Asia Pacific (AP). Greater access to renewable energy may give the US and Europe a new kind of leverage to encourage local manufacturing. Through substantial energy savings and energy independence, the production of various electronic components is likely to become increasingly cost-competitive with the Asia Pacific region.
Additionally, since 'reshoring' will require the construction of new manufacturing facilities, there's a substantial opportunity to design and equip with sustainability in mind from the outset. In contrast, in existing production lines, much of the equipment is already depreciated, increasing the relative cost of new investments into more sustainable manufacturing methodologies.
Outlook
Government mandates are cracking down on emissions, and public awareness and conscientiousness regarding global warming are growing, with many consumers making active choices to avoid certain companies. The electronics industry requires an overhaul of traditional manufacturing approaches contributing to global warming. Switching to low-toxicity, low-emission chemicals and processes is a key challenge to be addressed in the near future as more companies commit to attaining net-zero targets. Additionally, it is important to stay ahead of the curve as carbon prices may rise, making renewable energy the more reliable energy source to utilize.
Reducing the carbon footprint of the electronics industry is a daunting task, particularly for well-established manufacturers that are reluctant to divert from traditional methods. Across the world, government and consumer pressure are forcing manufacturers to take on greater responsibility in reducing their emissions. IDTechEx's analysis indicates that by embracing sustainable manufacturing methods, companies can benefit financially and demonstrate significant reductions in environmental impact. The rejuvenation of the European semiconductor industry presents the opportunity to build fabrication plants from scratch with sustainability as a priority. This means bypassing traditional legacy manufacturing processes and adopting new methods and equipment that minimize waste and lower emissions, for example, using additive approaches rather than subtractive. A comprehensive analysis and exploration of sustainable innovations within the field can be found in IDTechEx's report, "Sustainable Electronics Manufacturing 2023-2033".
Suggested Items
Wolfspeed Stock Soars After Filing for Chapter 11 Bankruptcy
07/01/2025 | I-Connect007 Editorial TeamOn July 1, Wolfspeed shares doubled following the company’s announcement on June 30 that it had filed for Chapter 11 bankruptcy protection.
Zollner Completes Full Acquisition of Bluechips Microhouse
07/01/2025 | Zollner Elektronik AGZollner Elektronik AG has successfully finalized its com- plete takeover of Bluechips Microhouse Co., Ltd., in Thailand. In the future the company will operate as part of the Zollner Group of companies under the leadership of Thomas Kiefl – strategically networked, technologically focused and internationally oriented.
Inission Acquires the Lithuanian Company Selteka
07/01/2025 | InissionInission AB has signed an agreement to acquire 100% of UAB Selteka. Selteka is a well-respected EMS (electronics manufacturing services) company with operations located in Kaunas, Lithuania.
RTX, Shield AI Partner to Develop New Defense Capabilities
07/01/2025 | RTXRTX and Shield AI announced a new partnership to integrate Shield AI capabilities into select RTX defense products, like loitering munitions and sensors. This collaboration will deliver enhanced, autonomous capabilities to US and allied defense forces.
Lockheed Martin Completes Acquisition of Amentum’s Rapid Solutions Portfolio
07/01/2025 | Lockheed MartinLockheed Martin has closed its acquisition of the Rapid Solutions business of Amentum, an engineering and technology solutions company.