-
- News
- Books
Featured Books
- pcb007 Magazine
Latest Issues
Current IssueSales: From Pitch to PO
From the first cold call to finally receiving that first purchase order, the July PCB007 Magazine breaks down some critical parts of the sales stack. To up your sales game, read on!
The Hole Truth: Via Integrity in an HDI World
From the drilled hole to registration across multiple sequential lamination cycles, to the quality of your copper plating, via reliability in an HDI world is becoming an ever-greater challenge. This month we look at “The Hole Truth,” from creating the “perfect” via to how you can assure via quality and reliability, the first time, every time.
In Pursuit of Perfection: Defect Reduction
For bare PCB board fabrication, defect reduction is a critical aspect of a company's bottom line profitability. In this issue, we examine how imaging, etching, and plating processes can provide information and insight into reducing defects and increasing yields.
- Articles
- Columns
- Links
- Media kit
||| MENU - pcb007 Magazine
Estimated reading time: 1 minute
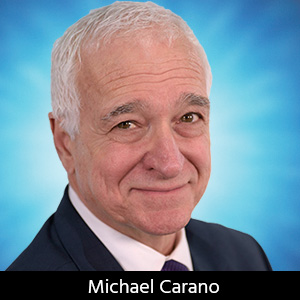
Contact Columnist Form
Lead-free Compatible OSPs: What Does This Really Mean?
Introduction
The setting: Early 2008. Many fabricators and EMS providers are continuing to push programs for RoHs compliance. This, of course, requires electronic assemblies to be, among other things, free of lead-bearing materials. To adopt such a program, the surface finish, component finish and the solder used in assembly must be lead-free. While the questions surrounding these issues are many, one in particular appears more frequently: How do we know that a particular finish is truly lead-free soldering compatible? This particular question is being addressed by one of the IPC standards writing committees responsible for developing an industry standard specification of organic solderability preservatives (OSP).
The Nature of the Beast
The IPC committee made up of a cross-section of suppliers, PWB fabricators, OEMs and EMS companies is working to complete the development of IPC-4555 (standard for OSP). This committee is developing a protocol to test OSP coatings for lead-free (high-temperature) compatibility. The protocol requires that copper coupons coated with the OSP would be subjected to three lead-free reflows, then tested for wettability with an appropriate wetting balance instrument. It should be noted that after the coupons are processed through the OSP solution, the coupons shall be rinsed with DI water and dried at 105°C. Following the protocol of the ANSI-JSTD-003B, the samples shall be fluxed using the standard 0.5% activated flux and immersed in SAC305 at a temperature of 255°C for 10 seconds. Further:
- Ten samples per test shall be run.
- The mean and standard deviation of the maximum force achieved shall be documented.
Interestingly, the committee has also recommended that a second set of test coupons be processed under the same pretreatment conditions. This time, however, without the drying step. Again, the ANSI-JSTD-003B, wetting balance procedure to measure wettability, will be utilized.
Read the full column here.
Editor's Note: This column originally appeared in the November 2014 issue of The PCB Magazine.
More Columns from Trouble in Your Tank
Trouble in Your Tank: Can You Drill the Perfect Hole?Trouble in Your Tank: Yield Improvement and Reliability
Trouble in Your Tank: Causes of Plating Voids, Pre-electroless Copper
Trouble in Your Tank: Organic Addition Agents in Electrolytic Copper Plating
Trouble in Your Tank: Interconnect Defect—The Three Degrees of Separation
Trouble in Your Tank: Things You Can Do for Better Wet Process Control
Trouble in Your Tank: Processes to Support IC Substrates and Advanced Packaging, Part 5
Trouble in Your Tank: Materials for PWB Fabrication—Drillability and Metallization