-
- News
- Books
Featured Books
- pcb007 Magazine
Latest Issues
Current IssueSales: From Pitch to PO
From the first cold call to finally receiving that first purchase order, the July PCB007 Magazine breaks down some critical parts of the sales stack. To up your sales game, read on!
The Hole Truth: Via Integrity in an HDI World
From the drilled hole to registration across multiple sequential lamination cycles, to the quality of your copper plating, via reliability in an HDI world is becoming an ever-greater challenge. This month we look at “The Hole Truth,” from creating the “perfect” via to how you can assure via quality and reliability, the first time, every time.
In Pursuit of Perfection: Defect Reduction
For bare PCB board fabrication, defect reduction is a critical aspect of a company's bottom line profitability. In this issue, we examine how imaging, etching, and plating processes can provide information and insight into reducing defects and increasing yields.
- Articles
- Columns
- Links
- Media kit
||| MENU - pcb007 Magazine
Estimated reading time: 1 minute
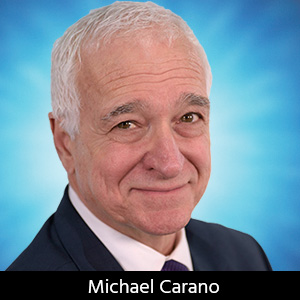
Contact Columnist Form
Oxide Alternatives to Enhance LPI Adhesion to Copper
Introduction
The printed wiring board industry has experienced issues with liquid photoimageable solder masks under various conditions. LPI breakdown or lifting near the copper-mask interface typifies a common defect seen when fabricators institute electroless-nickel immersion gold (ENIG) as a final finish. The aggressive nature of the ENIG process is a particular nuisance for some aqueous-based LPIs. Simply scrubbing the copper surface prior to soldermask application is often not an effective adhesion promotion mechanism for LPI and ENIG. (Please note that not all LPIs exhibit this problem.) A number of factors contribute to mask adhesion issues including acrylate content of the LPI, degree of cross-linking, mask thickness, and adhesion strength of the mask to the surface. Regardless, surface topography plays a unique role in enhancing the adhesion of the LPI. Before exploring surface topography further, it is important to understand outside influences such as ENIG and its effect on adhesion.
Influence of Plating Processes on LPI Adhesion
The electroless-nickel immersion gold plating process places significant stress on the liquid soldermask’s adhesion to the circuit board surface. Generally, there are several things the fabricator can do to ensure proper solder mask adhesion. Of course, proper surface prep is one of them. However, these other critical success factors are important (and will be presented in a future column):
- Thoroughly pre-cleaning of the substrate;
- Ink layer thickness;
- Complete pre-drying of the LPISM;
- Exposure energy;
- Correct adjustment of the developing parameters; and
- Control of the corresponding final curing conditions.
Surface Prep of Copper Prior to Soldermask
In Figure 1, the surface copper of the PWB was prepared with aluminum oxide. Even though the surface roughness appears sufficient, the fabricator experienced issues with LPI breakdown after ENIG. Figure 2 shows the mask peeling from the surface due to marginal adhesion. Most likely, even with less than adequate surface preparation, most surface finishes would not have had such an adverse effect as ENIG.
Read the full column here.
Editor's Note: This column originally appeared in the October 2014 issue of The PCB Magazine.
More Columns from Trouble in Your Tank
Trouble in Your Tank: Can You Drill the Perfect Hole?Trouble in Your Tank: Yield Improvement and Reliability
Trouble in Your Tank: Causes of Plating Voids, Pre-electroless Copper
Trouble in Your Tank: Organic Addition Agents in Electrolytic Copper Plating
Trouble in Your Tank: Interconnect Defect—The Three Degrees of Separation
Trouble in Your Tank: Things You Can Do for Better Wet Process Control
Trouble in Your Tank: Processes to Support IC Substrates and Advanced Packaging, Part 5
Trouble in Your Tank: Materials for PWB Fabrication—Drillability and Metallization