-
- News
- Books
Featured Books
- pcb007 Magazine
Latest Issues
Current IssueSales: From Pitch to PO
From the first cold call to finally receiving that first purchase order, the July PCB007 Magazine breaks down some critical parts of the sales stack. To up your sales game, read on!
The Hole Truth: Via Integrity in an HDI World
From the drilled hole to registration across multiple sequential lamination cycles, to the quality of your copper plating, via reliability in an HDI world is becoming an ever-greater challenge. This month we look at “The Hole Truth,” from creating the “perfect” via to how you can assure via quality and reliability, the first time, every time.
In Pursuit of Perfection: Defect Reduction
For bare PCB board fabrication, defect reduction is a critical aspect of a company's bottom line profitability. In this issue, we examine how imaging, etching, and plating processes can provide information and insight into reducing defects and increasing yields.
- Articles
- Columns
- Links
- Media kit
||| MENU - pcb007 Magazine
Estimated reading time: 1 minute
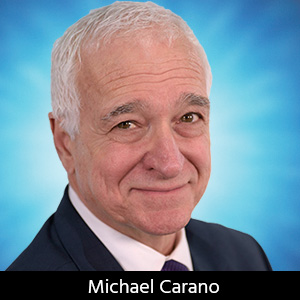
Contact Columnist Form
Root Cause of Failures in PWB Lamination
Introduction
Understanding the interactions of the materials, oxide treatment, and the lamination process will help you get to the root cause failures in multilayer fabrication.
When troubleshooting multilayer defects, it is necessary to again understand the effect certain process parameters have on quality and reliability. Truly, the quality of a multilayer printed circuit board (prior to desmear/metallization) will depend on several factors that will now be presented.
Interlaminar Bond Strength
There are several quality aspects of a multilayer PCB that should be measured on a regular basis. One key determinant of the reliability of the multilayer package is the interlaminar bond strength. The interlaminar bond strength is the strength of the heat-resistant bond between the pre-preg and the copper foil. Ideally, one strives for optimum resin flow encapsulation of the pre-preg with the treated copper innerlayer. The stronger the bond between the pre-preg and treated copper, the lower the chance of delamination. Figure 1 shows an example of delamination. In general, heat excursions increased the stress within the bond and that will lead to failures. So the bond between the copper and the resin needs to be as robust as possible.
The simple definition of delamination is, “a separation between plies within a base material, between a base material and a conductive foil, or any other planar separation within a printed board.” Again, we are referring to a separation. (More on blister and laminate voids in another column.) It is a huge concern that separation of the pre-preg from the copper foil is often misinterpreted for a blister. Indeed it is more serious than that. As an example, higher temperature resin systems may require more adjustments to the printed circuit processes such as: lamination cycle, baking, hole cleaning, drilling and routing. Polyimide resin and cyanate ester are the most commonly used high-temperature resin systems. These resins have Tgs in the 250°C range.
Read the full column here.
Editor's Note: This column originally appeared in the September 2014 issue of The PCB Magazine.
More Columns from Trouble in Your Tank
Trouble in Your Tank: Can You Drill the Perfect Hole?Trouble in Your Tank: Yield Improvement and Reliability
Trouble in Your Tank: Causes of Plating Voids, Pre-electroless Copper
Trouble in Your Tank: Organic Addition Agents in Electrolytic Copper Plating
Trouble in Your Tank: Interconnect Defect—The Three Degrees of Separation
Trouble in Your Tank: Things You Can Do for Better Wet Process Control
Trouble in Your Tank: Processes to Support IC Substrates and Advanced Packaging, Part 5
Trouble in Your Tank: Materials for PWB Fabrication—Drillability and Metallization