-
-
News
News Highlights
- Books
Featured Books
- pcb007 Magazine
Latest Issues
Current IssueThe Hole Truth: Via Integrity in an HDI World
From the drilled hole to registration across multiple sequential lamination cycles, to the quality of your copper plating, via reliability in an HDI world is becoming an ever-greater challenge. This month we look at “The Hole Truth,” from creating the “perfect” via to how you can assure via quality and reliability, the first time, every time.
In Pursuit of Perfection: Defect Reduction
For bare PCB board fabrication, defect reduction is a critical aspect of a company's bottom line profitability. In this issue, we examine how imaging, etching, and plating processes can provide information and insight into reducing defects and increasing yields.
Voices of the Industry
We take the pulse of the PCB industry by sharing insights from leading fabricators and suppliers in this month's issue. We've gathered their thoughts on the new U.S. administration, spending, the war in Ukraine, and their most pressing needs. It’s an eye-opening and enlightening look behind the curtain.
- Articles
- Columns
- Links
- Media kit
||| MENU - pcb007 Magazine
Estimated reading time: 1 minute
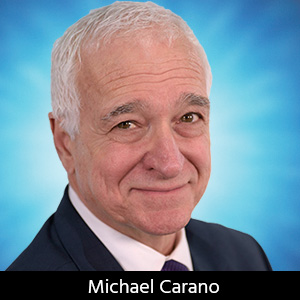
Contact Columnist Form
Oxide Alternative Processes
Introduction
It is all about optimizing the performance of the oxide alternative chemistry. This includes close monitoring of the main reactive ingredients of the process chemistry. And one of the first issues that the industry had to address, whether one is using reduced oxide chemistry or oxide alternatives, is pink ring. While the industry has enjoyed moderate success at minimizing the dreaded pink ring defect with reduced oxides, the desire has long been to simplify the bonding treatment process. Secondly, improving bond strength on high-performance and advanced resin materials is critical to the successful implementation of any interlayer treatment process. While the latter attribute is well documented, the ability of the oxide alternative bonding system to resist pink ring must be established. In all instances, where multilayer PWB test coupons (some fabricated with reduced oxide, others with alternative bonding treatment) were subjected a severe acid test, no pink ring was detected. The coupons were immersed in an aqueous solution of 17% hydrochloric acid for 15 minutes. After removal, the coupons were horizontally ground down to remove the outerlayer pad. Coupons were then inspected under 30x microscope. No pink ring was detected on the coupons fabricated with the organo-metallic (oxide alternative) bonding process. However, the reduced oxide bonding process showed pink ring.
It is important to recognize that the existence of pink ring does not suggest that the PCBs are rejectable. In fact, pink ring is defined in the IPC-600H (acceptability of printed circuit boards) as a process indicator. No evidence exists that pink ring affects functionality. In fact, the presence of pink ring concerns a number of manufacturing processes. The focus of concern should be the quality of the lamination bond, the laminate materials, drilling, desmear metallization processes. As an example, etchback prior to metallization can open up a wedge between the B-stage material and the oxide (or oxide alternative). The wedge defect thus can act as a via allowing acid chemicals to seep in, removing some of the treated copper foil coating leading to the appearance of pink ring.
Read the full column here.
Editor's Note: This column originally appeared in the July 2014 issue of The PCB Magazine.
More Columns from Trouble in Your Tank
Trouble in Your Tank: Yield Improvement and ReliabilityTrouble in Your Tank: Causes of Plating Voids, Pre-electroless Copper
Trouble in Your Tank: Organic Addition Agents in Electrolytic Copper Plating
Trouble in Your Tank: Interconnect Defect—The Three Degrees of Separation
Trouble in Your Tank: Things You Can Do for Better Wet Process Control
Trouble in Your Tank: Processes to Support IC Substrates and Advanced Packaging, Part 5
Trouble in Your Tank: Materials for PWB Fabrication—Drillability and Metallization
Trouble in Your Tank: Supporting IC Substrates and Advanced Packaging, Part 5