-
- News
- Books
Featured Books
- pcb007 Magazine
Latest Issues
Current IssueSales: From Pitch to PO
From the first cold call to finally receiving that first purchase order, the July PCB007 Magazine breaks down some critical parts of the sales stack. To up your sales game, read on!
The Hole Truth: Via Integrity in an HDI World
From the drilled hole to registration across multiple sequential lamination cycles, to the quality of your copper plating, via reliability in an HDI world is becoming an ever-greater challenge. This month we look at “The Hole Truth,” from creating the “perfect” via to how you can assure via quality and reliability, the first time, every time.
In Pursuit of Perfection: Defect Reduction
For bare PCB board fabrication, defect reduction is a critical aspect of a company's bottom line profitability. In this issue, we examine how imaging, etching, and plating processes can provide information and insight into reducing defects and increasing yields.
- Articles
- Columns
- Links
- Media kit
||| MENU - pcb007 Magazine
Estimated reading time: 1 minute
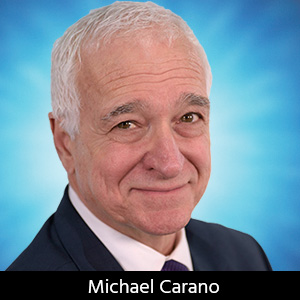
Contact Columnist Form
The Degrees of Nickel Hyper-corrosion and Mitigation Strategies
Introduction
In previous columns, I presented information on electroless nickel-immersion gold and possible concerns with black pad and brittle fracture. I am a firm believer (as well as a stickler) for tight process control. In addition, this also means that understanding the root cause or causes of defects must be pursued with vigor!
As a case in point, in this month’s column, I will present additional information about nickel hyper-corrosion by further defining the five degrees of hyper-corrosion. This implies that certain levels of the attack on the nickel are more detrimental than others. It should be noted that for purposes of this writing, I define hyper-corrosion as a spike or fissure in the nickel deposit evident after immersion gold plating. Finally the root causes of such attack on the base nickel will be presented along with strategies to mitigate these effects.
The Five Degrees of Hyper-corrosion
As the title of this column implies, we have identified five degrees of hyper-corrosion. While somewhat arbitrary, the extent of the corrosion spikes or fissures are responsible for the rating given. We found it necessary to provide this input to the industry as we found that, all too often, the OEM sees a tiny fissure in the nickel deposit and makes the false assumption that the PCB will fail in some way. That is categorically false, and I will explain why. First, however, let’s review the definition of each of the degrees of hyper-corrosion:
- Level 1: Only a few spike-type defects and not on every pad observed.
- Level 2: A few spike-type defects observed on most pads.
- Level 3: More than a few spike-type defects and some spreader/spike defects on most pads observed. At this activity level, more than 99% of the solder surface has not degraded or shown signs of increased phosphorus and as such should not inhibit intermetallic formation.
- Level 4: More spreader/spike defects and some area black band defects on most pads observed. This activity level may degrade solder joint integrity.
- Level 5: Mostly large areas of continuous black band on many pads observed. This level of defect activity will affect solder joint integrity.
Read the full column here.
Editor's Note: This column originally appeared in the June 2014 issue of The PCB Magazine.
More Columns from Trouble in Your Tank
Trouble in Your Tank: Can You Drill the Perfect Hole?Trouble in Your Tank: Yield Improvement and Reliability
Trouble in Your Tank: Causes of Plating Voids, Pre-electroless Copper
Trouble in Your Tank: Organic Addition Agents in Electrolytic Copper Plating
Trouble in Your Tank: Interconnect Defect—The Three Degrees of Separation
Trouble in Your Tank: Things You Can Do for Better Wet Process Control
Trouble in Your Tank: Processes to Support IC Substrates and Advanced Packaging, Part 5
Trouble in Your Tank: Materials for PWB Fabrication—Drillability and Metallization