-
- News
- Books
Featured Books
- pcb007 Magazine
Latest Issues
Current IssueSales: From Pitch to PO
From the first cold call to finally receiving that first purchase order, the July PCB007 Magazine breaks down some critical parts of the sales stack. To up your sales game, read on!
The Hole Truth: Via Integrity in an HDI World
From the drilled hole to registration across multiple sequential lamination cycles, to the quality of your copper plating, via reliability in an HDI world is becoming an ever-greater challenge. This month we look at “The Hole Truth,” from creating the “perfect” via to how you can assure via quality and reliability, the first time, every time.
In Pursuit of Perfection: Defect Reduction
For bare PCB board fabrication, defect reduction is a critical aspect of a company's bottom line profitability. In this issue, we examine how imaging, etching, and plating processes can provide information and insight into reducing defects and increasing yields.
- Articles
- Columns
- Links
- Media kit
||| MENU - pcb007 Magazine
Estimated reading time: 1 minute
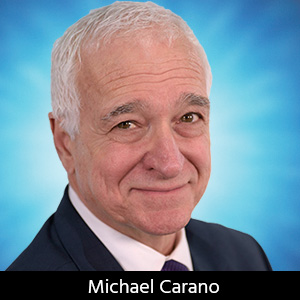
Contact Columnist Form
Oxide vs. Oxide Alternative, Part 2
In last month’s column, I presented an overview of conventional oxide chemistry and the critical success factors of the process. In this column, we begin our review of the oxide alternative process that is often referred to as an organo-metallic coating process. The reason for this alternative name will be explained in this column.
With continued emphasis on long-term reliability and vastly improved electrical performance, manufacturers of high layer-count multilayer printed wiring boards are beginning to abandon the reduced oxide bonding process in favor of alternative methods. One such method, presented here as an organo-metallic adhesion promotion system, increases the bond strength of the resin to the copper by modifying the topography of the copper surface and simultaneously depositing an organic layer that acts as an adhesion promoter. The surface area or topography of the copper is enhanced by the selective micro-etching along the grain boundaries of the copper. (This mechanism will be discussed further below.) This is in contrast to the oxide-based chemical processes in that the oxide processes are designed to “grow a crystal structure” on the copper surface. The concern with oxide processes (even the formulations designed to give a denser shorter crystal structure) is that the higher pressures and temperatures of lamination required for higher performance laminate materials will fracture the oxide crystal structure reducing the bond strength. With that said, let’s discuss oxide alternative or organo-metallic chemistry and how it all works.
Read the full column here.
Editor's Note: This column originally appeared in the March 2014 issue of The PCB Magazine.
More Columns from Trouble in Your Tank
Trouble in Your Tank: Can You Drill the Perfect Hole?Trouble in Your Tank: Yield Improvement and Reliability
Trouble in Your Tank: Causes of Plating Voids, Pre-electroless Copper
Trouble in Your Tank: Organic Addition Agents in Electrolytic Copper Plating
Trouble in Your Tank: Interconnect Defect—The Three Degrees of Separation
Trouble in Your Tank: Things You Can Do for Better Wet Process Control
Trouble in Your Tank: Processes to Support IC Substrates and Advanced Packaging, Part 5
Trouble in Your Tank: Materials for PWB Fabrication—Drillability and Metallization