-
- News
- Books
Featured Books
- pcb007 Magazine
Latest Issues
Current IssueSales: From Pitch to PO
From the first cold call to finally receiving that first purchase order, the July PCB007 Magazine breaks down some critical parts of the sales stack. To up your sales game, read on!
The Hole Truth: Via Integrity in an HDI World
From the drilled hole to registration across multiple sequential lamination cycles, to the quality of your copper plating, via reliability in an HDI world is becoming an ever-greater challenge. This month we look at “The Hole Truth,” from creating the “perfect” via to how you can assure via quality and reliability, the first time, every time.
In Pursuit of Perfection: Defect Reduction
For bare PCB board fabrication, defect reduction is a critical aspect of a company's bottom line profitability. In this issue, we examine how imaging, etching, and plating processes can provide information and insight into reducing defects and increasing yields.
- Articles
- Columns
- Links
- Media kit
||| MENU - pcb007 Magazine
Basic Principles of Polymer Thick Film Flexible Circuits
August 7, 2014 | Joe Fjelstad, Verdant ElectronicsEstimated reading time: 1 minute
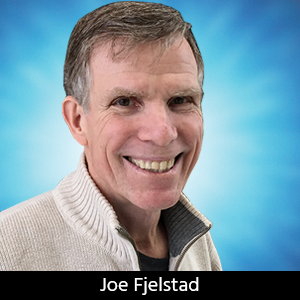
Polymer thick film (PTF) technologies have been used to manufacture printed circuits for decades. In fact, some of the very first circuits ever produced in volume were made by printing conductive inks patterned on an insulating substrate using a stencil. While the versatile nature of the materials used and the simplicity of the manufacturing process have made possible its continued use for more than six decades. In more recent decades, the technology has seen extensive use in the manufacture of inexpensive, polyester film-based membrane switches for electronic devices of every imaginable type, from hand-held calculators and computer keyboards to household appliances including microwave ovens and washers and dryers and beyond.
Polymer thick film circuits are similar in many ways to their rigid and flexible counterparts; however, because of the materials and processes, they have their own very specific design rules. Because most PTF processing is most commonly based on screen printing technology, the limits of design are intrinsically linked to the printed ink’s processing considerations and limitations. For example, there are the unique processing properties for conductive and resistive as well as insulating inks in terms of their thixotropy, which influence their printability. There is also the important consideration of the final values for the conductivity and/or resistivity of the ink used when cured. In addition, there are also the limits of the screen printing materials and the processes used.
Traditional screen printing methods are typically limited to the production of relatively course features (e.g., 250 µm). However, very fine-featured screen printed circuit technology has been reported down to ranges closer to 125 µm. For the foreseeable future, screen printing will remain an important technology for the manufacture of PTF circuits, both rigid and flexible. That said, inkjet printing is well positioned to augment time honored screen print methods. It also opens the door to realizing the possibility of producing circuits economically at a run unit of one, which has been one of the ideals of manufacturing.
Read the full article here.
Editor's Note: This article originally appeared in the June 2014 issue of The PCB Magazine.
Suggested Items
Microchip Enters into Partnership Agreement with Delta Electronics on Silicon Carbide Solutions
07/18/2025 | Globe NewswireThe growth of artificial intelligence (AI) and the electrification of everything are driving an ever-increasing demand for higher levels of power efficiency and reliability.
ViTrox’s HITS 5.0 Empowers Global Partners with Innovative Solutions and Stronger Bonds
07/16/2025 | ViTroxViTrox, strives to be the World’s Most Trusted Technology Company, proudly announces the successful conclusion of its fifth edition of High Impact Training for Sales (HITS 5.0), held from 23rd to 27th June 2025 at ViTrox Campus 2.0 and 3.0, located in Batu Kawan Industrial Park, Penang, Malaysia.
Global Citizenship: The Global Push for Digital Inclusion
07/16/2025 | Tom Yang -- Column: Global CitizenshipIt can be too easy to take the technology at our fingertips for granted: high-speed internet, cloud-based collaboration, and instant video calls across continents. Yet, for billions of people, access to these digital tools is a distant dream. As a global community, we must ensure that technology is available to all. Here is how technology is bridging physical, economic, and educational gaps in underserved regions and profoundly reshaping lives.
Microchip Expands Space-Qualified FPGA Portfolio with New RT PolarFire® Device Qualifications and SoC Availability
07/10/2025 | MicrochipContinuing to support the evolving needs of space system developers, Microchip Technology has announced two new milestones for its Radiation-Tolerant (RT) PolarFire® technology: MIL-STD-883 Class B and QML Class Q qualification of the RT PolarFire RTPF500ZT FPGA and availability of engineering samples for the RT PolarFire System-on-Chip (SoC) FPGA.
Infineon Advances on 300-millimeter GaN Manufacturing Roadmap as Leading Integrated Device Manufacturer (IDM)
07/10/2025 | InfineonAs the demand for gallium nitride (GaN) semiconductors continues to grow, Infineon Technologies AG is poised to capitalize on this trend and solidify its position as a leading Integrated Device Manufacturer (IDM) in the GaN market.