-
- News
- Books
Featured Books
- pcb007 Magazine
Latest Issues
Current IssueSales: From Pitch to PO
From the first cold call to finally receiving that first purchase order, the July PCB007 Magazine breaks down some critical parts of the sales stack. To up your sales game, read on!
The Hole Truth: Via Integrity in an HDI World
From the drilled hole to registration across multiple sequential lamination cycles, to the quality of your copper plating, via reliability in an HDI world is becoming an ever-greater challenge. This month we look at “The Hole Truth,” from creating the “perfect” via to how you can assure via quality and reliability, the first time, every time.
In Pursuit of Perfection: Defect Reduction
For bare PCB board fabrication, defect reduction is a critical aspect of a company's bottom line profitability. In this issue, we examine how imaging, etching, and plating processes can provide information and insight into reducing defects and increasing yields.
- Articles
- Columns
- Links
- Media kit
||| MENU - pcb007 Magazine
Estimated reading time: 1 minute
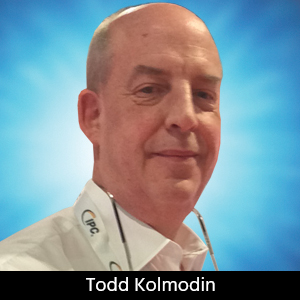
A Summary of Various Test Requirements
IPC Class 3
The PCB industry has advanced significantly in the recent millennium. OEM specifications and requirements have also advanced due to the maturing of technologies, which has caused the requirements of electrical test of these higher technology products to advance and increase in intensity. Obviously, the more mature a technology, the finer the lines and spaces must be, the more hole and vias must be present, and the more complex the testing must become. There is just more to test in a smaller amount of space.
Long gone are the “pin-in-hole” technology PCBs, which are now surpassed by the large multilayer, blind/buried and rigid-flex technologies. For the suppliers of electrical test, be it in-house test departments or sub-contracted, the industry specifications can be confusing, and at times incomprehensible.
The OEMs direct the IPC specification (6012, 9252A, AS9100, etc.) for their fabrication to the manufacturer, but in many cases do the OEMs or CMs really know what they are asking for? Do they really understand what they are requiring and how complicated it may be?
There are many variables associated with these specifications and requirements to their designated classes regarding electrical test. OEMs often overlook the electrical properties associated with IPC class performance requirement, and of course, this can be a problem. Manufacturing, plating, etching and all those processes may be within the class requirements.
During the coming months, I will discuss various aspects and intricacies of electrical test. To get started, I will address IPC class 1, 2, and 3
Class I: General Electronic Products
This class includes consumer products, some computer products and computer peripherals suitable for applications where cosmetic imperfections are not important, and the major requirement is function of the completed board.
Read the full column here.
Editor's Note: This column originally appeared in the April 2014 issue of The PCB Magazine.
More Columns from Testing Todd
Testing Todd: Why 4-wire Kelvin?Testing Todd: Why TDR?
Testing Todd: Positivity Boosts Employee Morale
Testing Todd: Preparing Employees for the Long Haul
Testing Todd: Where Can We Improve?
Testing Todd: Turning Into the Wind
Testing Todd: Coming Back to Life—Design Recovery
Testing Todd: Decision Time—Invest or Delegate?