-
- News
- Books
Featured Books
- pcb007 Magazine
Latest Issues
Current IssueThe Hole Truth: Via Integrity in an HDI World
From the drilled hole to registration across multiple sequential lamination cycles, to the quality of your copper plating, via reliability in an HDI world is becoming an ever-greater challenge. This month we look at “The Hole Truth,” from creating the “perfect” via to how you can assure via quality and reliability, the first time, every time.
In Pursuit of Perfection: Defect Reduction
For bare PCB board fabrication, defect reduction is a critical aspect of a company's bottom line profitability. In this issue, we examine how imaging, etching, and plating processes can provide information and insight into reducing defects and increasing yields.
Voices of the Industry
We take the pulse of the PCB industry by sharing insights from leading fabricators and suppliers in this month's issue. We've gathered their thoughts on the new U.S. administration, spending, the war in Ukraine, and their most pressing needs. It’s an eye-opening and enlightening look behind the curtain.
- Articles
- Columns
- Links
- Media kit
||| MENU - pcb007 Magazine
Estimated reading time: 2 minutes
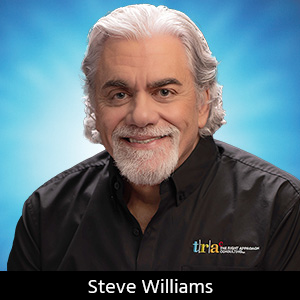
Best Practices 101, Part 3
As we deep dive into the four critical steps of value stream mapping, (VSM), by now you should have a good understanding of just how powerful some of these tools and techniques can be. And the best part? It is not rocket science; it’s just common sense!
Step 1: Identify the Proper Process
This step cannot be stressed enough because it is often overlooked by many companies new to Lean. Fresh out of training, the VSM team often runs out and starts mapping the first process they see. While VSM, if anything, is better than nothing, efforts should be focused on the critical processes having the greatest impact on the product.
Let’s look at a typical supply chain transaction from the point of a customer order through delivery of the product. Figure 1 example shows a macro view of the supply chain cycle to illustrate how VSM works. This high-level view would be one way to drive Lean down through the supply chain to sub-suppliers. Of course, discrete processes within each supplier would need to be value stream mapped to enable reductions in their respective lead times. This product depicts a process with an eight-week lead time, which, after value stream mapping the process, reveals that there are only seven hours of value-added time on this product. As unbelievable as these results sound, most organizations experience a similar disparity in their processes. The key takeaway of this scenario is that the excessive lead time has created enough customer dissatisfaction that the business is in jeopardy.
Now let’s turn this diagram into a current state value stream map. The original working session for developing a VSM is very manual, and as I mentioned earlier, is best done on a white board or with Post-it Notes. As the name implies, the goal is to find out how the processing is currently operating today, not how the SOP says things should be or how it was designed to be. The goal is to capture reality onto a piece of paper—the current state. Use a stopwatch for the time studies and determine the actual times where practical. While the VSM will eventually be finalized with software, the initial map should be created with Post-it Notes because there will be frequent changes as the team goes through this process. Once the process has been defined, the Post-it Notes map can be digitized with flowcharting software. Value stream maps use a variety of unique symbols that are not used in traditional flowcharts and diagrams, as shown in Figure 2. Word and Excel can be used for flowcharting, but for ease of use, professional flowcharting software like Visio should be used.
Read the full column here.
Editor's Note: This column originally appeared in the October 2014 issue of The PCB Magazine.
More Columns from The Right Approach
The Right Approach: ‘Twas the Night Before Christmas (Harley-style)The Right Approach: I Hear the Train A Comin'
The Right Approach: Culture Change is Key to a QMS
The Right Approach: Leadership 101—Be a Heretic, Not a Sheep
The Right Approach: Leadership 101—The Law of Legacy
The Right Approach: Leadership 101: The Law of Explosive Growth
The Right Approach: Leadership 101—The Law of Timing
The Right Approach: The Law of Sacrifice