-
-
News
News Highlights
- Books
Featured Books
- pcb007 Magazine
Latest Issues
Current IssueThe Hole Truth: Via Integrity in an HDI World
From the drilled hole to registration across multiple sequential lamination cycles, to the quality of your copper plating, via reliability in an HDI world is becoming an ever-greater challenge. This month we look at “The Hole Truth,” from creating the “perfect” via to how you can assure via quality and reliability, the first time, every time.
In Pursuit of Perfection: Defect Reduction
For bare PCB board fabrication, defect reduction is a critical aspect of a company's bottom line profitability. In this issue, we examine how imaging, etching, and plating processes can provide information and insight into reducing defects and increasing yields.
Voices of the Industry
We take the pulse of the PCB industry by sharing insights from leading fabricators and suppliers in this month's issue. We've gathered their thoughts on the new U.S. administration, spending, the war in Ukraine, and their most pressing needs. It’s an eye-opening and enlightening look behind the curtain.
- Articles
- Columns
- Links
- Media kit
||| MENU - pcb007 Magazine
Estimated reading time: 2 minutes
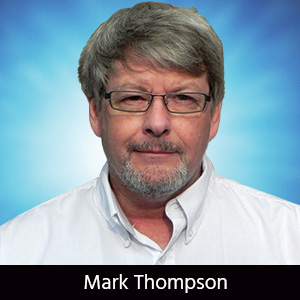
Understanding the Typical CAM Process
CAM vs. Capability
Many new customers have some misconceptions about what a typical fab shop can and cannot do. There are levels of manufacturing that need to be well understood by the buyer. The PCB buyer needs to know where a board will be a good fit based on the parts’ complexity. How does this happen? How does the PCB buyer or a contract manufacturer know who is (or is not) a good fit based on a myriad of different designs, from simple 2 to 4 layer RF parts to high-layer count HDI, blind and buried via parts? If the part is of medium complexity, it can be built by virtually any mid to higher level PCB fabricator. Many times it boils down to things like quote response time. More diligent buyers may use a tool such as The PCB List where they can compare technology levels side-by-side and make good decisions about where a part should go. Not all PCB buyers need a shop that can do 2 mil lines and spaces or laser stacked vias. Sometimes the product dictates a shop of this type must be used; other times, when a given design does not “push” the fabricator’s limits, more fabricators obviously have an opportunity to show what they can do.
What is CAM?
Not all board fabricators have the ability to have both CAD and CAM. You may say to yourself, “But a CAM tool should be able to do some, if not all, CAD functions,” and that is true; but if you are really getting to the design level, you need to have a design team. Many PCB fabricators do not have design capabilities but do have the ability to understand the customers’ needs and recognize design attributes.
Let me give you some examples of this from simple CAM assumptions to more complex ones. Let’s say a design has copper poured right to the edge of the part, but is NOT a Z-axis or edge-plated part. A good CAM department may do a very minimal clip of the metal around the periphery like 0.003 to 0.004”. This is imperceptible to the end user as it appears metal is right to the edge and if the metal would have been left alone there may be burring at final rout (functional, but not cosmetically the best ). Again, this is where a good CAM person comes into play: When would they NOT do something like a minimal clip for rout? RF launches on an obvious RF part; here, we know the intention is to literally have metal right to the edge and that any burring at final rout is acceptable with the customer. This is where their understanding of electrical function comes in as well, plus years of practical experience.
Read the full column here.
Editor's Note: This column originally appeared in the February 2014 issue of The PCB Magazine.
More Columns from The Bare (Board) Truth
The Bare (Board) Truth: My Top Six Design ChallengesThe Bare (Board) Truth: Via Basics
The Bare (Board) Truth: 5 Questions About Improving Thermal Management
The Bare (Board) Truth: Teaching the Next Generation—An Overview of Today’s University Courses
The Bare (Board) Truth: Fabrication Starts With Solid Design Practices
Board Negotiations: Design Rules and Tolerances
The Bare (Board) Truth: Eliminate Confusion
The Bare (Board) Truth: Getting on the Same Page—A Data Story