-
-
News
News Highlights
- Books
Featured Books
- pcb007 Magazine
Latest Issues
Current IssueThe Hole Truth: Via Integrity in an HDI World
From the drilled hole to registration across multiple sequential lamination cycles, to the quality of your copper plating, via reliability in an HDI world is becoming an ever-greater challenge. This month we look at “The Hole Truth,” from creating the “perfect” via to how you can assure via quality and reliability, the first time, every time.
In Pursuit of Perfection: Defect Reduction
For bare PCB board fabrication, defect reduction is a critical aspect of a company's bottom line profitability. In this issue, we examine how imaging, etching, and plating processes can provide information and insight into reducing defects and increasing yields.
Voices of the Industry
We take the pulse of the PCB industry by sharing insights from leading fabricators and suppliers in this month's issue. We've gathered their thoughts on the new U.S. administration, spending, the war in Ukraine, and their most pressing needs. It’s an eye-opening and enlightening look behind the curtain.
- Articles
- Columns
- Links
- Media kit
||| MENU - pcb007 Magazine
Estimated reading time: 4 minutes
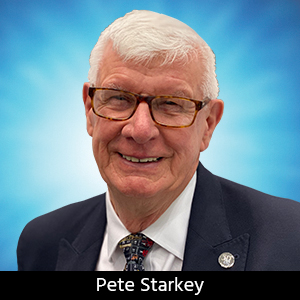
Contact Columnist Form
ECWC 2014: The Embedded Technology Session
The 13th Electronic Circuits World Convention in Nuremberg, Germany, provided an exceptional diversity of information and knowledge, through 123 presentations in 26 sessions.
The Embedded Technology session on the second day attracted an enthusiastic audience, keen to learn about PCBs with embedded RFID and embedded magnetic cores, interposers with embedded thin-film capacitors, and flexible microsystems with ultra-thin embedded silicon chips. The session was introduced and moderated by Dr. Eric Maiser of VDMA Productronic.
The first presentation was delivered by Martin Cotton, long-standing expert in embedded RFID, who demonstrated the scope offered by the technology beyond basic identification and product tracking. Reviewing the fundamental benefits of RFID, and its advantages over bar-code labeling, he stressed that he was describing a process for creating a wireless communication portal within the structure of, and if necessary electrically connected to, the PCB, which could achieve very much more in functionality than simply acting as a traceability device and could effectively become part of the “internet of things”. Read ranges of 9 to 10 metres were now attainable, at up to 200 devices per second, and line-of-sight was not a necessity. Bar codes, by comparison, could hold only limited data, could not be written-back to and could only provide a reference to be used with a database.
Embedded RFID devices could be could be connected to various sensors to enable additional functional features regarding safety, traceability, and working environment, and could be activated when a device was powered-up, for example, to lock the device against unauthorised use. Cotton listed and discussed many applications including reporting of performance data for maintenance planning and failure prediction, providing a complete cradle-to-grave information pipeline, and enabling the best security and anti-counterfeit strategies.
Next to speak was Chun Chen from Shenzen King Brother Electronics Technology, describing a method of manufacturing multilayer PCBs with embedded magnetic cores. He explained that embedded core technology was an effective route to achieving miniaturisation of power modules, but that certain fabrication difficulties had to be overcome.
For the core to function effectively, it was necessary to position it precisely within the multilayer construction, then to form insulated plated-via-hole conductors through the core by drilling clearance holes, vacuum plugging with resin, drilling concentric holes leaving insulating resin sleeves, then metallising these holes to become part of the windings of the inductor, with printed circuit features taking the place of wires. Chen explained the details of the lay-up and laminating technique and how the positional tolerances and bond strengths had been achieved. The magnetic cores were very fragile and the through-drilling of clearance holes was a critical operation for which drilling parameters had been optimised by serial DOE procedures. Problems of micro-cracking of the resin fill had been overcome by careful choice of materials and an enhanced vacuum lamination process. Other processing challenges which had been addresd included step-etching of asymmetric copper thicknesses.
Page 1 of 2
More Columns from The European Angle
CircuitData: A New Open Standard for PCB Fab Data ExchangeI Never Realised It Was So Complicated!
The European Angle: Institute of Circuit Technology 43rd Annual Symposium
Ventec International Group's Martin Cotton Celebrates 50 Years in PCB Design
Reporting on the Institute of Circuit Technology Spring Seminar
EuroTech: Raw Materials Supply Chain—Critical Challenges Facing the PCB Industry
EuroTech: ENIPIG—Next Generation of PCB Surface Finish
EuroTech: Institute of Circuit Technology Northern Seminar 2016, Harrogate