-
- News
- Books
Featured Books
- pcb007 Magazine
Latest Issues
Current IssueThe Hole Truth: Via Integrity in an HDI World
From the drilled hole to registration across multiple sequential lamination cycles, to the quality of your copper plating, via reliability in an HDI world is becoming an ever-greater challenge. This month we look at “The Hole Truth,” from creating the “perfect” via to how you can assure via quality and reliability, the first time, every time.
In Pursuit of Perfection: Defect Reduction
For bare PCB board fabrication, defect reduction is a critical aspect of a company's bottom line profitability. In this issue, we examine how imaging, etching, and plating processes can provide information and insight into reducing defects and increasing yields.
Voices of the Industry
We take the pulse of the PCB industry by sharing insights from leading fabricators and suppliers in this month's issue. We've gathered their thoughts on the new U.S. administration, spending, the war in Ukraine, and their most pressing needs. It’s an eye-opening and enlightening look behind the curtain.
- Articles
- Columns
- Links
- Media kit
||| MENU - pcb007 Magazine
DSG Invests in the Future
January 28, 2015 | Barry Matties, I-Connect007Estimated reading time: 1 minute
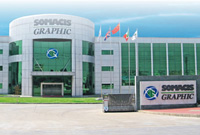
I was recently invited for another tour of Dongguan Somacis Graphic PCB Co. Ltd (DSG) in Dongguan, China. The last time I was there, COO Mauro Dallora gave me a tour of their facility. I was very impressed then. Now, nearly four years later, Mauro led the tour again, and I was even more impressed.
It is very clear that they have continued to invest in new equipment, with a keen focus on automation. In the last year alone, DSG invested more than USD$10 million in equipment. Mauro explained that with the increasing labor rates and the demand for higher-quality products, the key to long-term success in China is automation and tight process control. They have plans to invest about the same amount in 2015.
DSG has also increased its annual revenue by USD$20M since my last visit. To do so, they have only hired about 70 additional employees. Mauro said that the company has plans to double its revenue without hiring additional people. That would mean that they would be doing more than $100M with a team of approximately 500 people, or more than $200,000 per employee. That’s a strong ratio.
But DSG’s strategy does not rely on manufacturing automation alone. They have also focused on efficiencies and cost savings in all aspects of their business. For example, with their green initiative, all the lighting in the facility has been converted to low-cost lighting solutions.
DSG is becoming a paperless factory, and this speeds up the information transfer and reduces cost. The waste treatment area recycles 65% of the company’s wastewater. And when you tour DSG, you will see one of the cleanest PCB manufacturing facilities in the world.
Mauro will tell you that good housekeeping increases the quality of the products. With all of the above, coupled with the drive from Mauro and the leadership team, DSG should remain highly competitive.
The following video interview will give you some more insight into the DSG story:
Suggested Items
Meet the Author Podcast: Martyn Gaudion Unpacks the Secrets of High-Speed PCB Design
07/10/2025 | I-Connect007In this special Meet the Author episode of the On the Line with… podcast, Nolan Johnson sits down with Martyn Gaudion, signal integrity expert, managing director of Polar Instruments, and three-time author in I-Connect007’s popular The Printed Circuit Designer’s Guide to... series.
Intervala Hosts Employee Car and Motorcycle Show, Benefit Nonprofits
08/27/2024 | IntervalaIntervala hosted an employee car and motorcycle show, aptly named the Vala-Cruise and it was a roaring success! Employees had the chance to show off their prized wheels, and it was incredible to see the variety and passion on display.
KIC Honored with IPC Recognition for 25 Years of Membership and Contributions to Electronics Manufacturing Industry
06/24/2024 | KICKIC, a renowned pioneer in thermal process and temperature measurement solutions for electronics manufacturing, is proud to announce that it has been recognized by IPC for 25 years of membership and significant contributions to electronics manufacturing.
Boeing Starliner Spacecraft Completes Successful Crewed Docking with International Space Station
06/07/2024 | BoeingNASA astronauts Barry "Butch" Wilmore and Sunita "Suni" Williams successfully docked Boeing's Starliner spacecraft to the International Space Station (ISS), about 26 hours after launching from Cape Canaveral Space Force Station.
KIC’s Miles Moreau to Present Profiling Basics and Best Practices at SMTA Wisconsin Chapter PCBA Profile Workshop
01/25/2024 | KICKIC, a renowned pioneer in thermal process and temperature measurement solutions for electronics manufacturing, announces that Miles Moreau, General Manager, will be a featured speaker at the SMTA Wisconsin Chapter In-Person PCBA Profile Workshop.