-
- News
- Books
Featured Books
- pcb007 Magazine
Latest Issues
Current IssueSales: From Pitch to PO
From the first cold call to finally receiving that first purchase order, the July PCB007 Magazine breaks down some critical parts of the sales stack. To up your sales game, read on!
The Hole Truth: Via Integrity in an HDI World
From the drilled hole to registration across multiple sequential lamination cycles, to the quality of your copper plating, via reliability in an HDI world is becoming an ever-greater challenge. This month we look at “The Hole Truth,” from creating the “perfect” via to how you can assure via quality and reliability, the first time, every time.
In Pursuit of Perfection: Defect Reduction
For bare PCB board fabrication, defect reduction is a critical aspect of a company's bottom line profitability. In this issue, we examine how imaging, etching, and plating processes can provide information and insight into reducing defects and increasing yields.
- Articles
- Columns
- Links
- Media kit
||| MENU - pcb007 Magazine
Are There Advantages to Changing Your Registration System?
March 22, 2015 | Barry Matties, I-Connect007Estimated reading time: 9 minutes
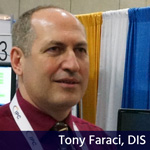
I recently had a conversation with DIS's Tony Faraci at IPC APEX EXPO 2015, to learn more about their pinless registration system. What was most interesting to me are the potential advantages a pinless system offers and if so, why the process has not been widely adopted.
Barry Matties: Hello, Tony. Thanks for sitting down with me today. Could you please tell us about the DIS pinless registration system?
Tony Faraci: Yes, thanks, Barry. What is happening with this type of a system, as opposed to a conventional pin lamination technology, is that we are optically aligning all the internal layers of a panel. Conventional wisdom used to be that you would post-etch punch all your cores and then pin. Now, you are eliminating that whole process. You are eliminating pinning, you're eliminating all of that punching and all of that pin tooling and now we are optically aligning all the layers and tack bonding them together.
By optically aligning, all those mechanical pin tolerances are eliminated, and of course you are not limited to certain panel sizes. The layers are aligned optically and then we use an induction bonding system that actually bonds the layers together. The advantage here is that the registration can be checked before lamination, which really can't be done with any type of pinning system.
You can kind of do it with a riveting system, let's say, or eyelets, but with this type of system, now you can check your registration before going into the lamination press, then you laminate the panel, come out, and now you can again check the registration of that panel. Having the data immediately before and after lamination can show what's happening inside the press.
Besides this valuable data set, this is also telling you what our system is doing. It's giving you an overall view at different points of the process which they've never been able to do before. You can kind of do it with a riveting system but you're not going to do such high layer counts and it will not be repeatable. So DIS pinless technology is the next step up from pin because it eliminates all those mechanical problems.
Matties: For those who already have a pin system in place, are there any special processes or changes that they have to make?
Faraci: It changes a little bit in the process. What you're doing is using similar targets like they do on a punching machine, but now they are adding these welding coupons. They are just a quarter-inch by three-quarter-inch solid copper pads at four points on the panel that we'll use to tack bond.
Where it really changes is the reduced handling and lay-up. The machine is basically an optical lay-up machine, so instead of handling the panel once at post-etch punch and then going through oxide or oxide alternative, where there is some more stretching of the layer, and then laying up on mechanical pins, where most of the bulk error is, we’re only handling it once, at optical lay-up.
We're not selling a product that's competing against the post-etch punch; it's a process change. It eliminates that pin-up process and instead is optically aligning the layers; this really is the biggest change.
It's a little bit different in the process, so there is a learning curve. But the benefit for the customer is great, because now they can start looking at what's happening in the press. Today, most high-end shops work with pins, so what do they do, they lay up a book and you don't know if there's a shift -did it happen at lay-up, did it happen in the press, did it happen at transport?
So, that's one of the biggest changes. Another product that we developed about six years ago was a multi-camera system that allows us to check the layers front to back, in order to figure out where the best fit positions are for that layer. That also works well with our systems, because that data gets captured and it goes into our alignment systems.
Matties: How does that benefit?
Faraci: Let's say a customer is running higher-end boards. They can, if they have an LDI process for example, print a 2D bar code on every layer, serialize the core, and then our multi-camera system can actually measure that core and capture the positional data. And of course it's tied to that serial number.
Then when it gets to our alignment machines, they read that barcode and they know the positional data of that core, based on the eight targets, and now we can process the panel. So it enables all our existing two-camera machines—for example, what they have at DSG—once customers buy this unit, they’re able to have it work like an eight-camera system. Or you could use it off line just to measure panels to make sure that the layers are within tolerance before you use them at lay-up.
Matties: So, with your system the border is now smaller?Page 1 of 2
Suggested Items
I-Connect007 Editor’s Choice: Five Must-Reads for the Week
07/18/2025 | Nolan Johnson, I-Connect007It may be the middle of the summer, but the news doesn’t quit, and there’s plenty to talk about this week, whether you’re talking technical or on a global scale. When I have to choose six items instead of my regular five, you know it’s good. I start by highlighting my interview with Martyn Gaudion on his latest book, share some concerning tariff news, follow that up with some promising (and not-so-promising) investments, and feature a paper from last January’s inaugural Pan-European Design Conference.
Elephantech Launches World’s Smallest-Class Copper Nanofiller
07/17/2025 | ElephantechJapanese deep-tech startup Elephantech has launched its cutting-edge 15 nm class copper nanofiller – the smallest class available globally. This breakthrough makes Elephantech one of the first companies in the world to provide such advanced material for commercial use.
Copper Price Surge Raises Alarms for Electronics
07/15/2025 | Global Electronics Association Advocacy and Government Relations TeamThe copper market is experiencing major turbulence in the wake of U.S. President Donald Trump’s announcement of a 50% tariff on imported copper effective Aug. 1. Recent news reports, including from the New York Times, sent U.S. copper futures soaring to record highs, climbing nearly 13% in a single day as manufacturers braced for supply shocks and surging costs.
I-Connect007 Editor’s Choice: Five Must-Reads for the Week
07/11/2025 | Andy Shaughnessy, Design007 MagazineThis week, we have quite a variety of news items and articles for you. News continues to stream out of Washington, D.C., with tariffs rearing their controversial head again. Because these tariffs are targeted at overseas copper manufacturers, this news has a direct effect on our industry.I-Connect007 Editor’s Choice: Five Must-Reads for the Week
Digital Twin Concept in Copper Electroplating Process Performance
07/11/2025 | Aga Franczak, Robrecht Belis, Elsyca N.V.PCB manufacturing involves transforming a design into a physical board while meeting specific requirements. Understanding these design specifications is crucial, as they directly impact the PCB's fabrication process, performance, and yield rate. One key design specification is copper thieving—the addition of “dummy” pads across the surface that are plated along with the features designed on the outer layers. The purpose of the process is to provide a uniform distribution of copper across the outer layers to make the plating current density and plating in the holes more uniform.