-
-
News
News Highlights
- Books
Featured Books
- pcb007 Magazine
Latest Issues
Current IssueThe Hole Truth: Via Integrity in an HDI World
From the drilled hole to registration across multiple sequential lamination cycles, to the quality of your copper plating, via reliability in an HDI world is becoming an ever-greater challenge. This month we look at “The Hole Truth,” from creating the “perfect” via to how you can assure via quality and reliability, the first time, every time.
In Pursuit of Perfection: Defect Reduction
For bare PCB board fabrication, defect reduction is a critical aspect of a company's bottom line profitability. In this issue, we examine how imaging, etching, and plating processes can provide information and insight into reducing defects and increasing yields.
Voices of the Industry
We take the pulse of the PCB industry by sharing insights from leading fabricators and suppliers in this month's issue. We've gathered their thoughts on the new U.S. administration, spending, the war in Ukraine, and their most pressing needs. It’s an eye-opening and enlightening look behind the curtain.
- Articles
- Columns
- Links
- Media kit
||| MENU - pcb007 Magazine
Splitting Hairs: The Manufacture of HDI and Substrate Test Fixtures
May 14, 2015 | Todd Kolmodin, Gardien ServicesEstimated reading time: 2 minutes
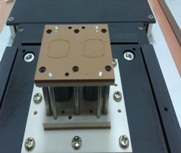
Testing of higher-density product has become ever more challenging with the advancement of chip technology. BGAs, CCDs and other active components have decreased in size so much that historical industry accepted test methodology can no longer effectively test these newer substrates incorporating this higher technology.
Universal grid test machines in North America, for the most part, are limited to single and double-density grids. Dedicated (wired) fixtures can combat some of the density issues faced in today’s test arena, but to successfully succeed in the high-volume demand market a test solution must be found to efficiently test the product and also provide automation to reduce cost.
Universal multi-plate fixtures routinely use test pins down to .3 mm. As pin size decreases, the need for extra plates in the fixture increases, so as to stabilize the pin and provide accurate loading of the pin. However, critical mass is soon reached as the fixture can no longer be solved due to inadequate grid contact availability. Further, as the density is maximized the fixture loses internal support and finally becomes unstable producing false defects, excessive troubleshooting and lost time.
Additionally, there is an ever-increasing demand for 4WK measurement especially on HDI boards, requiring two probes contacting the same pad simultaneously, which can only be tackled, especially for volume production, with this or similar technology.
HDI Fixtures vs. Substrate Fixtures
Quad and octal density universal equipment is used for standard HDI fixturing. Pin sizes for this type of fixturing are usually 90–110μm with a length of 20–30mm, therefore much smaller and shorter than standard universal grid fixtures.
To put this in to perspective the human hair has an average diameter of about 70μm (micron.) Pins in a substrate fixture of current generation typically are 70–50μm; the next generation under development will reach 40–25μm.
Substrate fixtures are typically not used with universal test machines. They require a much higher grid density; therefore the grid itself is generated as a wired solution either to standard connectors or to a universal one-touch interface depending on the final machine used.
HDI fixture usually test a complete test array, whereas substrate fixtures usually test only one or two images of the entire array and the machine will step the board through in multiple tests. That is mainly done to achieve the high accuracy required to test those kinds of boards and the extreme cost and time involved to make these fixture.
HDI fixture typically can be produced within 48 hours, the manufacturing time for a substrate fixture is usually 100–200 hours, and extreme cases can even take longer.
The manufacturing process for the substrate fixture is much more complex than the standard universal fixture. Accuracy is absolutely critical for the success of registering the product to the fixture.
There are basically six steps in the manufacturing process whether it is a hybrid design or a tension probe design:
1. DFM—Engineering
2. Drill
3. Electrode level—wiring, electroplating
4. Probe level—adding probes (wires)
5. Final assembly
6. Final QC and test setup
Editor's Note: This article originally appeared in the April issue of The PCB Magazine.
Suggested Items
Magnalytix and Foresite to Host Technical Webinar on SIR Testing and Functional Reliability
06/26/2025 | MAGNALYTIXMagnalytix, in collaboration with Foresite Inc., is pleased to announce an upcoming one-hour Webinar Workshop titled “Comparing SIR IPC B-52 to Umpire 41 Functional & SIR Test Method.” This session will be held on July 24, 2025, and is open to professionals in electronics manufacturing, reliability engineering, and process development seeking insights into new testing standards for climatic reliability.
Defense Speak Interpreted: Is DARPA Still Around After CHIPS?
06/24/2025 | Dennis Fritz -- Column: Defense Speak InterpretedWhen I first published my Defense Speaks Interpreted column in January 2019 on the Defense Advanced Research Projects Agency (DARPA ERI), the agency advocated for an expanded Defense emphasis on closing the growing technology gap in microelectronics. The emphasis was on “resurgence.”
I-Connect007 Editor’s Choice: Five Must-Reads for the Week
06/13/2025 | Marcy LaRont, I-Connect007Today is Friday the 13th, and in much of Western folklore, this is a day when bad luck is lurking. But while Friday the 13th may top Western superstition charts, the global calendar is sprinkled with its own unlucky legends. In Spain and Greece, the bad juju lands on Tuesday the 13th—a day linked to Mars, the god of war, and naturally, chaos. In Italy, it’s Friday the 17th that is feared, thanks to the Roman numeral XVII, which can be rearranged to spell VIXI—Latin for “I have lived” (a poetic way of saying you’re dead).
TTCI Celebrates Melanie Rutkauskas’ 10-Year Anniversary and Her Leadership of New Training Division
06/12/2025 | TTCIThe Test Connection Inc. (TTCI), a leading provider of electronic test and manufacturing solutions, is proud to celebrate Melanie Rutkauskas on her 10-year anniversary with the company.
Bridging the Knowledge Gap in Test: A Conversation with Bert Horner
06/11/2025 | Barry Matties, I-Connect007Bert Horner is a seasoned industry veteran and co-creator of The Test Connection, Inc. (TTCI), a test and inspection company spanning over 45 years. In this candid conversation, Bert reflects on the challenges our industry faces with the retirement of career professionals and the subsequent loss of critical tribal knowledge. As he unveils The Training Connection’s innovative training initiatives, Bert emphasizes the importance of evolving educational programs that align with industry needs, particularly in design for test (DFT), and sheds light on strategies being implemented to foster the next generation of engineers.