-
-
News
News Highlights
- Books
Featured Books
- pcb007 Magazine
Latest Issues
Current IssueThe Hole Truth: Via Integrity in an HDI World
From the drilled hole to registration across multiple sequential lamination cycles, to the quality of your copper plating, via reliability in an HDI world is becoming an ever-greater challenge. This month we look at “The Hole Truth,” from creating the “perfect” via to how you can assure via quality and reliability, the first time, every time.
In Pursuit of Perfection: Defect Reduction
For bare PCB board fabrication, defect reduction is a critical aspect of a company's bottom line profitability. In this issue, we examine how imaging, etching, and plating processes can provide information and insight into reducing defects and increasing yields.
Voices of the Industry
We take the pulse of the PCB industry by sharing insights from leading fabricators and suppliers in this month's issue. We've gathered their thoughts on the new U.S. administration, spending, the war in Ukraine, and their most pressing needs. It’s an eye-opening and enlightening look behind the curtain.
- Articles
- Columns
- Links
- Media kit
||| MENU - pcb007 Magazine
Estimated reading time: 3 minutes
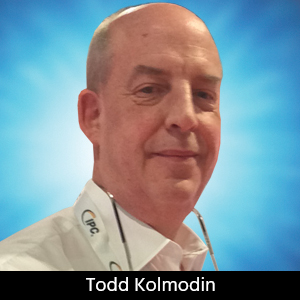
Electrical Test: Surface Finish vs. Water Marks
After a brief time off and a successful IPC APEX EXPO, I’m here to field your questions and get back to business. Thank you to all that stopped by to see me at the show. It was a good year in San Diego and the weather (as usual) mostly cooperated. Looks like we’ll all be heading back to Vegas next year!
This month we will look at the ballet of sorts, performed by electrical test vs. surface finishes— namely witness marks. Over time, new finishes have come to market. Some allow better conductivity while others reduce overall cost of precious materials. Regardless of the finish, electrical test must be performed on these circuits. With that comes the caveat of how much of a witness mark can be left on any given landing pad and still be acceptable to the CM or the final OEM user.
First, we must understand what a witness mark actually is. In “down home” terms, when building a fence the old-fashioned way, you typically hammer the planks of the fence to the supporting framework. When the hammer hits the nail, the hammer leaves (unless you are really good) a round indentation into the board you are attaching, a.k.a. a witness mark! This is a mark indicating the historic process that was applied. Witness marks in electrical test are much the same. When an electrical test is performed, a physical contact is made from the machine to the PCB. This works the same whether it is from a translator fixture on a bed of nails or the direct contact from a flying probe. The combination of the surface finish being used and the type of electrical tester being used can produce a wide array of witness marks. Most of these marks are benign and acceptable, but in severe cases they can be destructive resulting in costly rework or even worse, scrap!
Some finishes are more critical than others. These range from HASL, immersion tin and ENIG, to the critical finishes such as immersion gold, immersion silver, soft gold and the ultimately delicate wire-bond. Customer requirements and industry specifications have guidelines regarding what acceptable witness marks may be. In the general specification for the manufacture of PWBs, the specification references the “pristine area” of the landing pad when gauging the acceptability of the witness mark. For a rectangle SMT landing pad, the pristine area is defined by the central 80% of the land width x 80% of the land length. For round SMT landing pads, the pristine area is defined as the central 80% of the diameter. Electrical test probe witness marks within the pristine area for Class I, Class II and Class III are considered cosmetic in nature and are acceptable provided the requirements of the final finish are met (IPC-6012C).
As noted earlier, witness marks may be different depending on the type of test solution being used. Fixtures use either solid pins or spring pins with different options for head styles. These can be round (conical), spear point or even chisel point. The main goal for Electrical test is to perform the test required while minimizing the witness mark to the PCB. Many are under of the opinion that fixtures are the main source of pad damage resulting from electrical test and in many cases this is true. Due to the mechanics of the fixture, translator pins, stripper plates (cassettes) there are many factors in play that can cause a pin to “lock” and apply excessive pressure/force to the delicate landing pad.
Editor's Note: This article originally appeared in the April issue of The PCB Magazine.
More Columns from Testing Todd
Testing Todd: Why 4-wire Kelvin?Testing Todd: Why TDR?
Testing Todd: Positivity Boosts Employee Morale
Testing Todd: Preparing Employees for the Long Haul
Testing Todd: Where Can We Improve?
Testing Todd: Turning Into the Wind
Testing Todd: Coming Back to Life—Design Recovery
Testing Todd: Decision Time—Invest or Delegate?